Interior design office fit-out for ST Micro, Edinburgh
Office relocation and refurbishment is an experience that once completed, no-one is ever in a hurry to repeat any time soon.
Traditionally, a range of professional services along with trades and furniture/hardware suppliers are engaged by various means including word of mouth, tender and incumbent suppliers.
Interior design office fit out Tanfield Edinburgh
Time-Lapse Video
When ST Microelectronics from Edinburgh, decided that they would move rather than refurbish their existing premises, they took an early decision that they wanted to deal with one supplier only.
A one stop solution provider on a interior design and office fit-out project of this scale means you need a serious business to deliver – especially when this also had to include specialist removal and hoisting work which involved lifting equipment weighing 1000kg and clearance tolerances of less than 5mm!
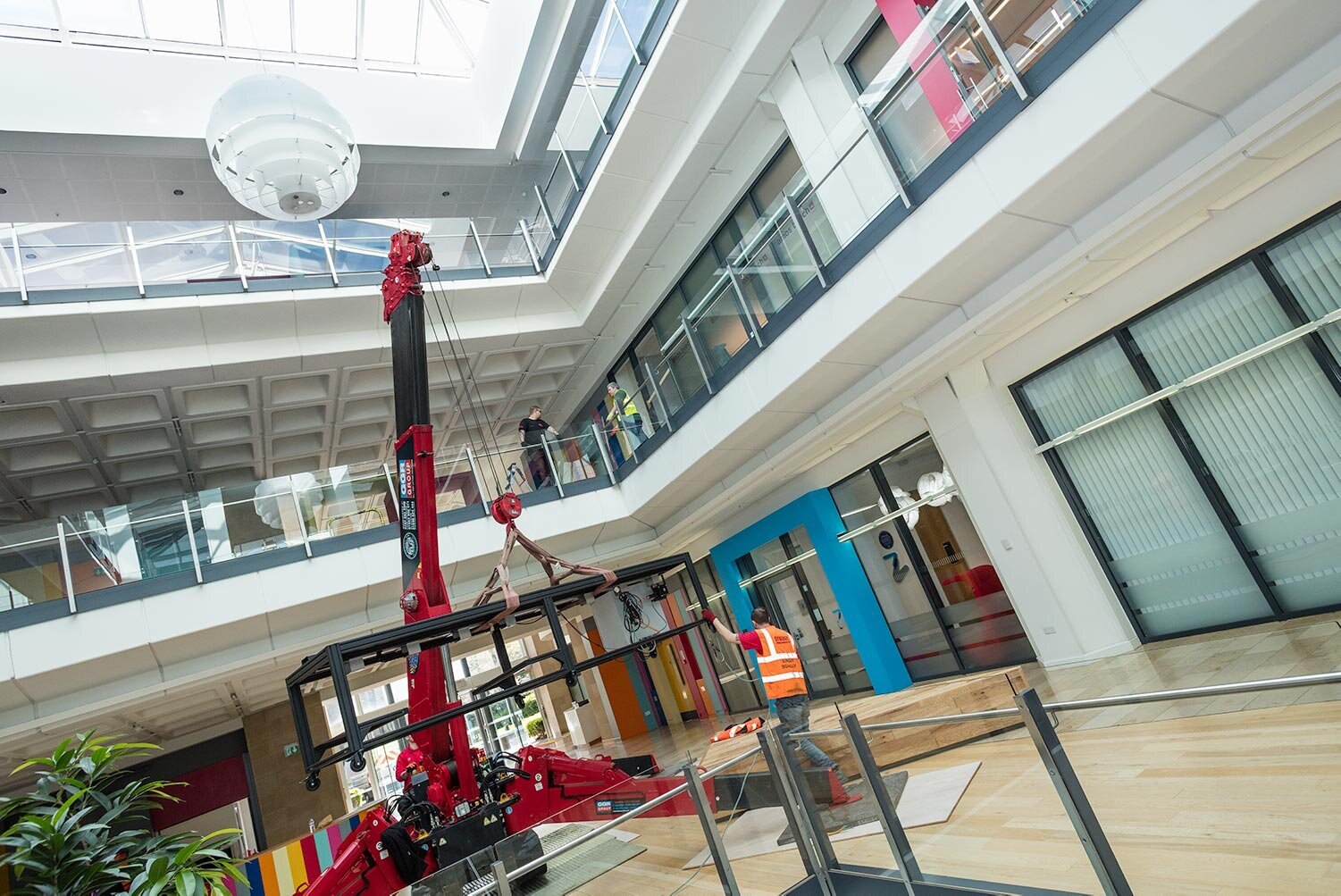
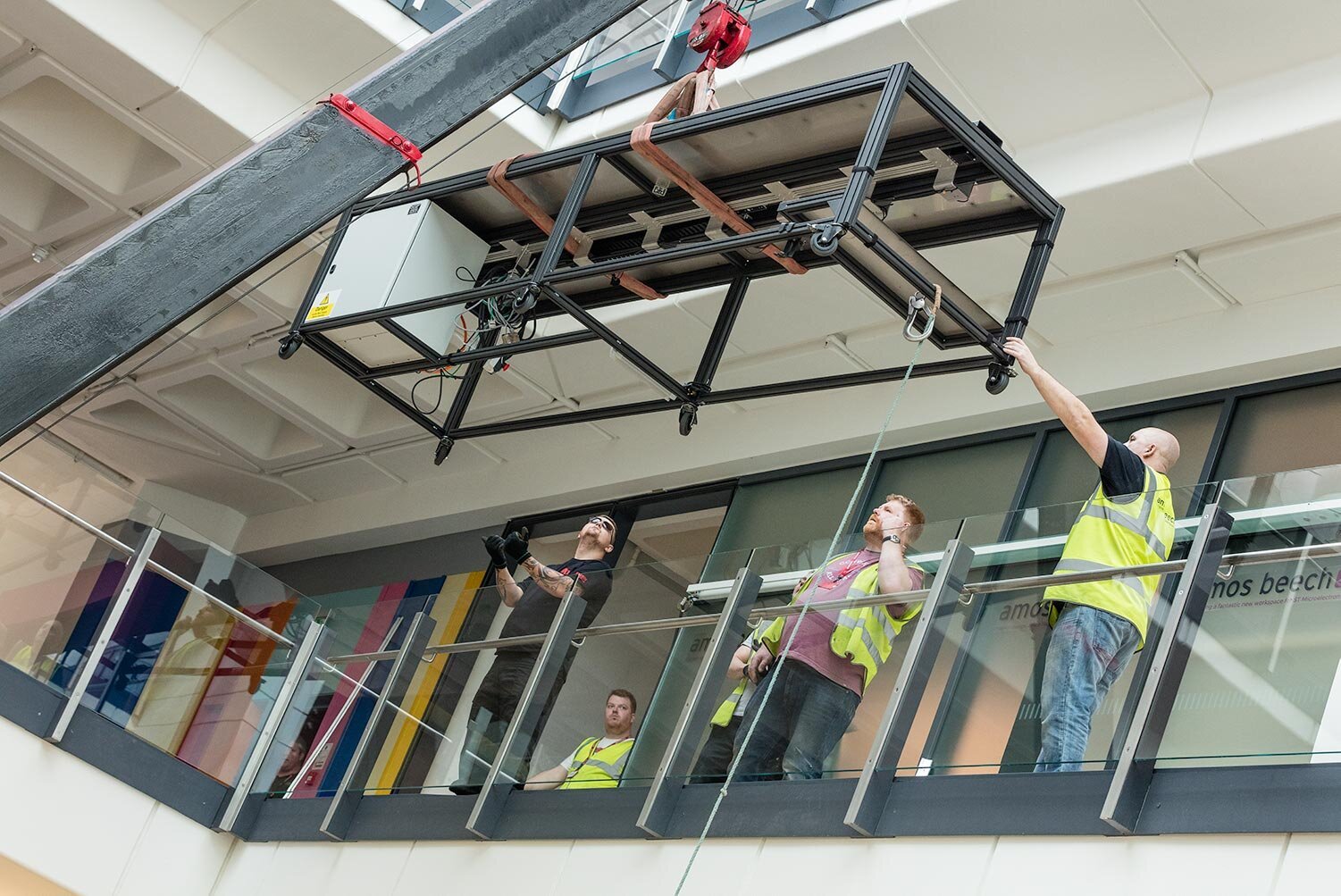
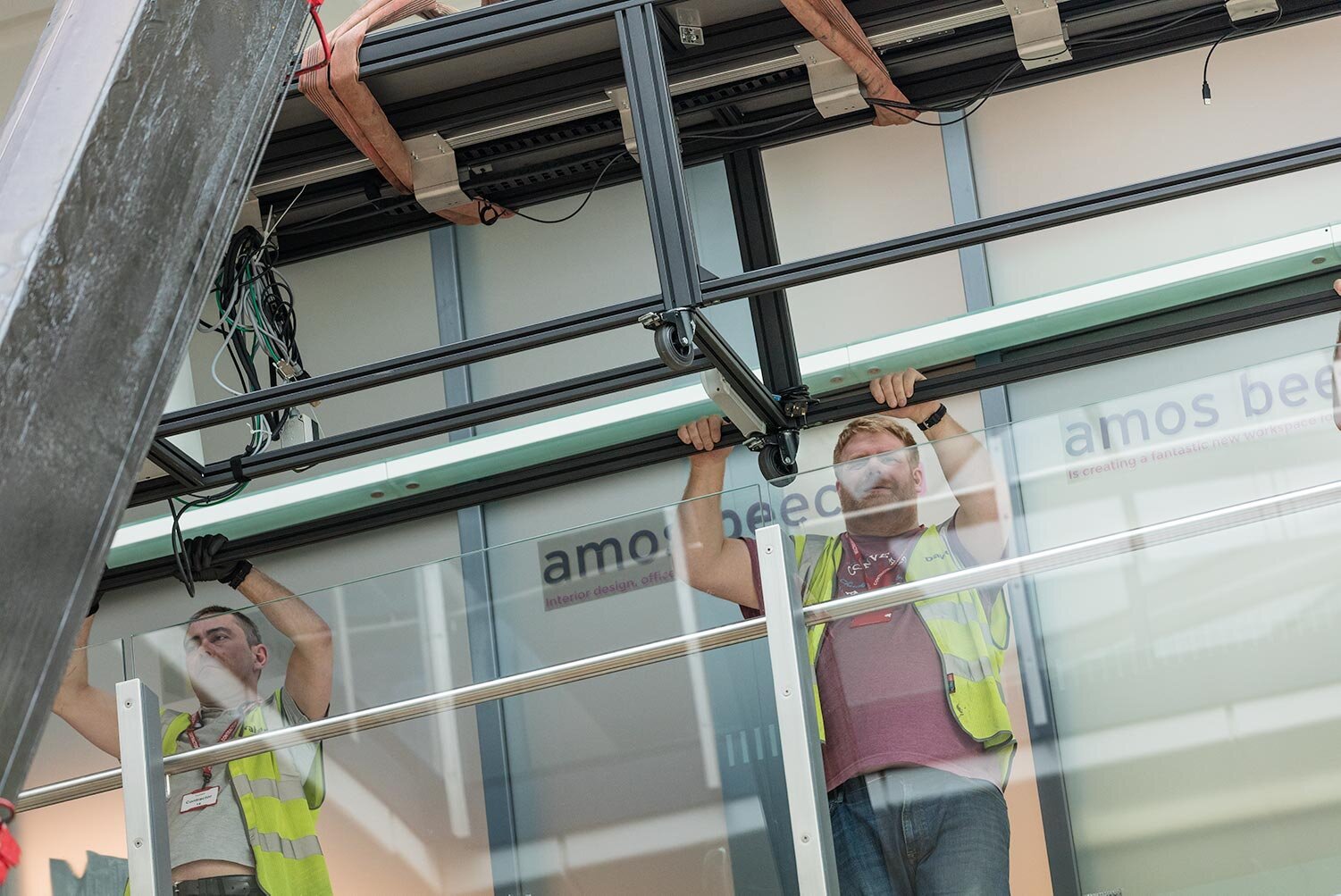
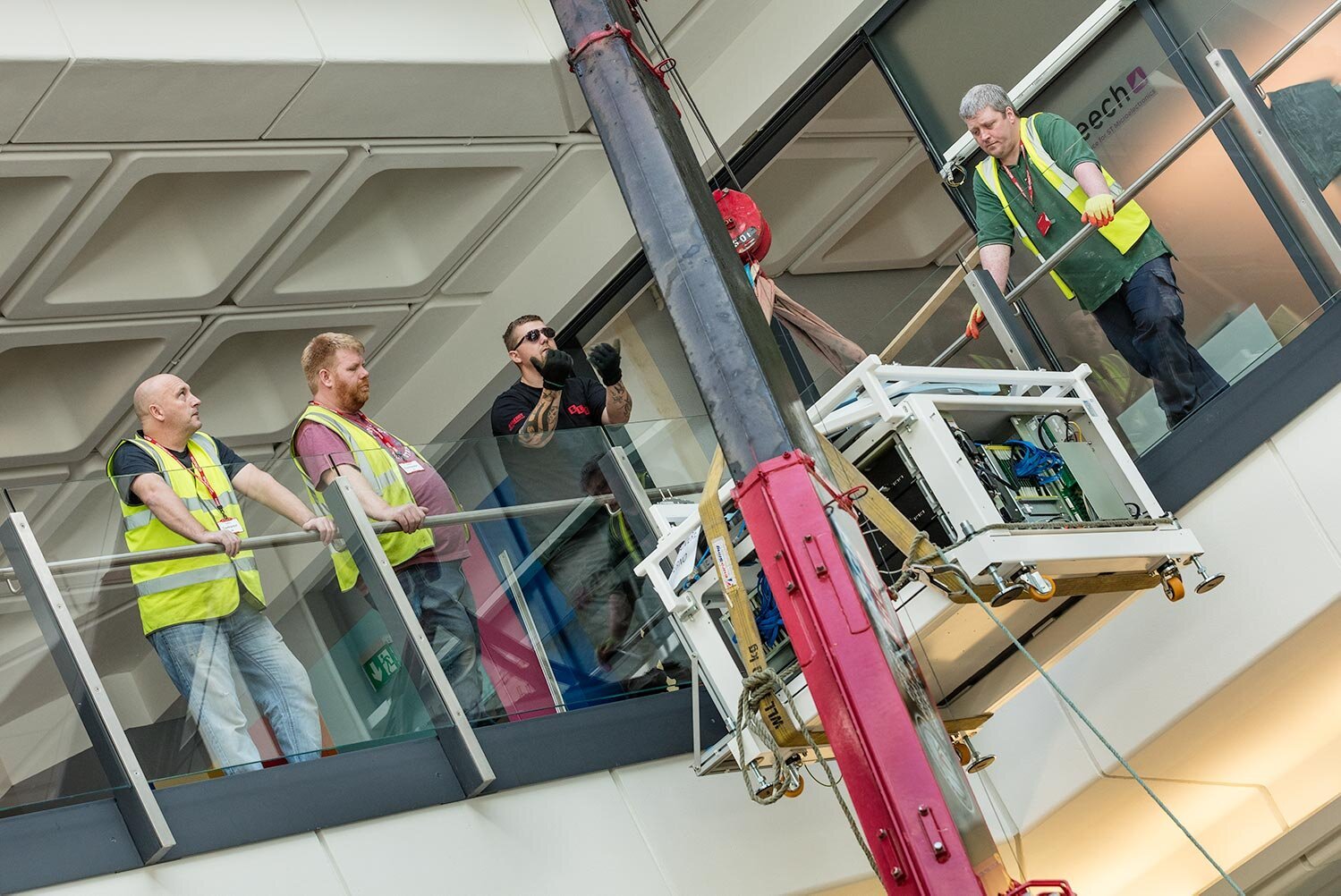
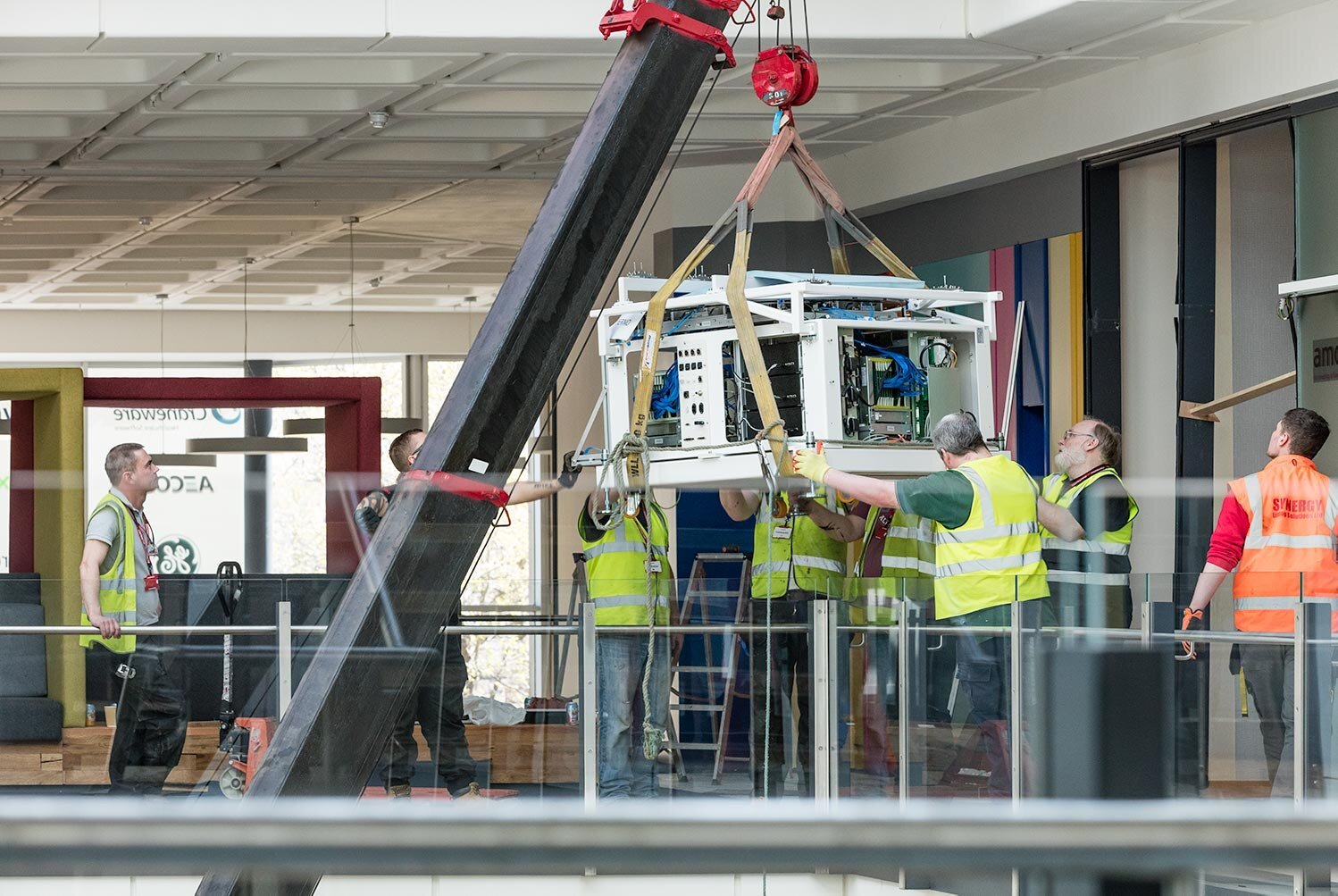
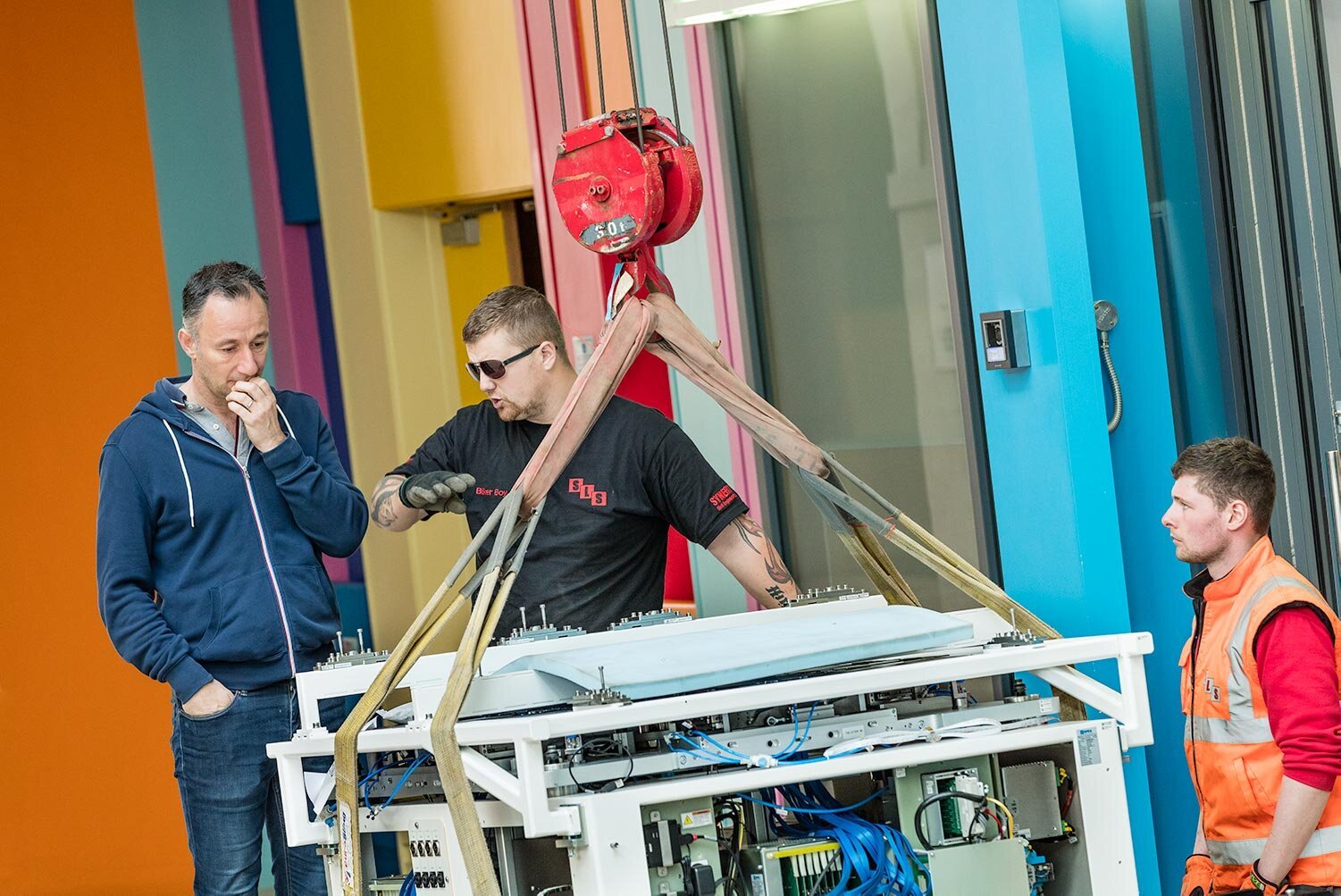
Step up Amos Beech and the team. Having worked with ST in Edinburgh for the previous 15 years in their old offices, their track record meant that they were invited to tender for the project along with two other firms. Demonstrating a deep understanding of the ST requirements and combining this with a highly effective theme that accurately reflects their branding, they duly won the contract to fit-out the new Tanfield office space in Ediburgh.
As with any project, a tight timeframe was expected and the Amos Beech team of Commercial Interior Designers Edinburgh were under the cosh. Working with our Construction Team and Quantity Surveyors, design integrity was maintained whilst keeping a firm eye on the budgetted office fit out costs.
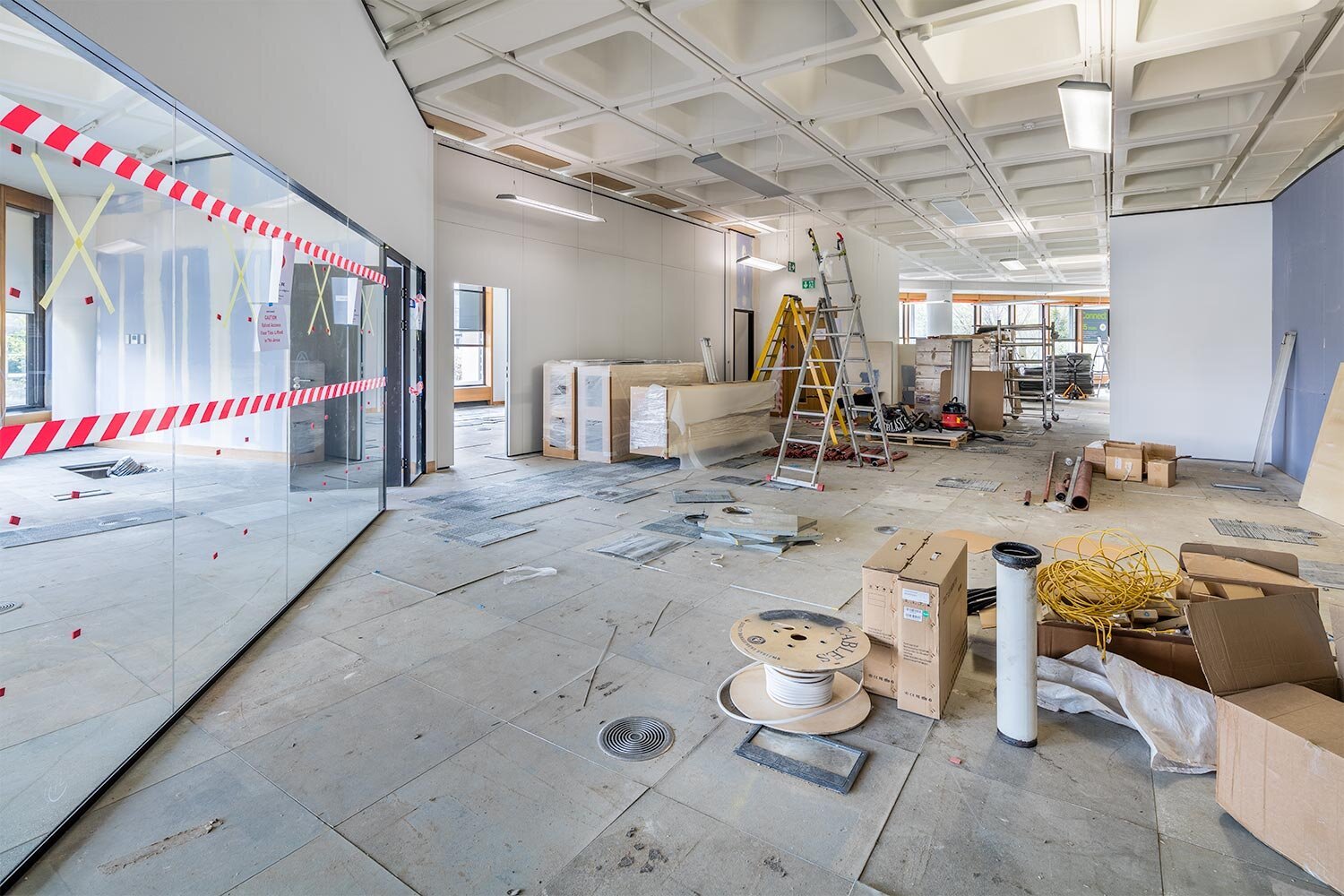
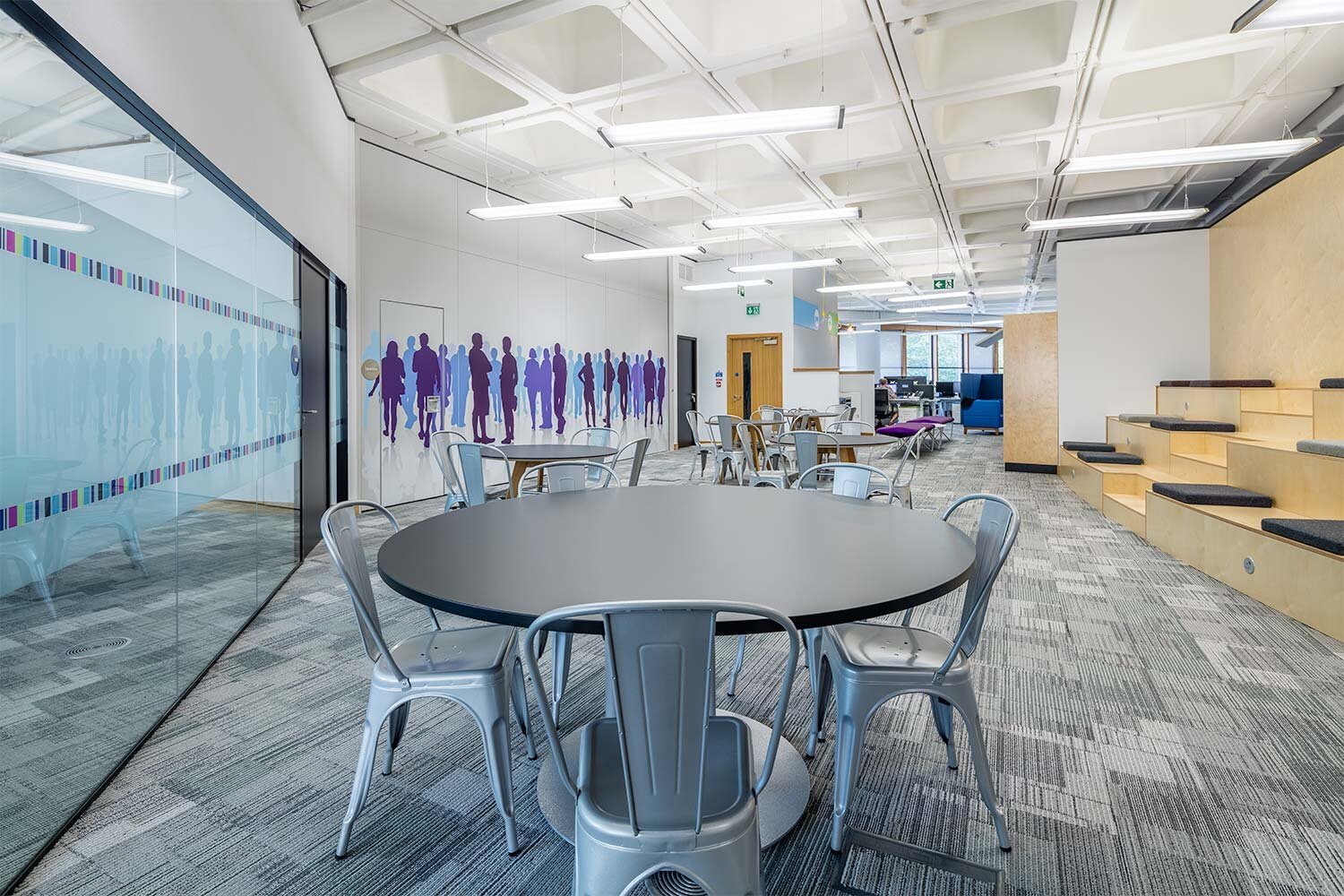
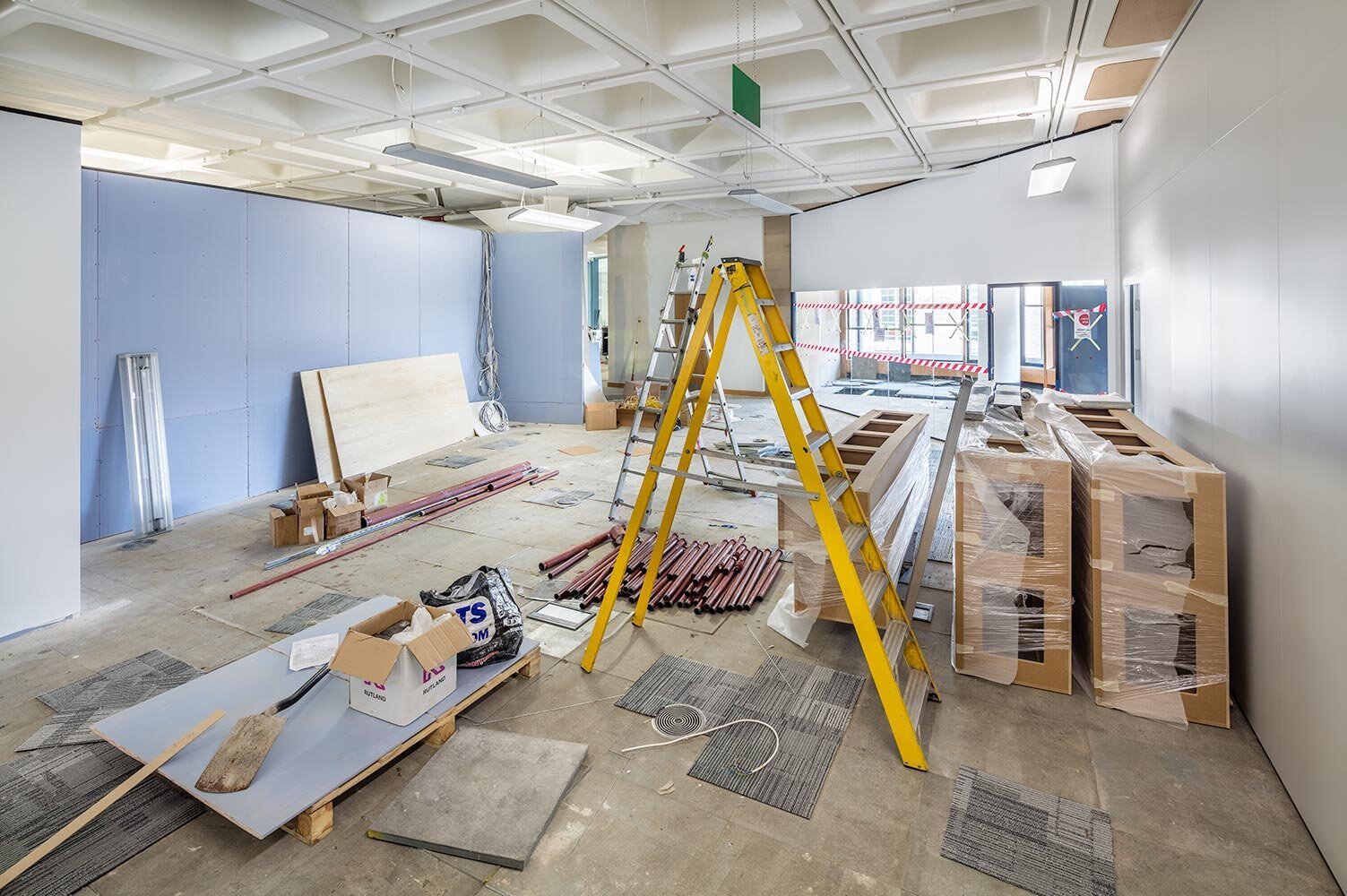
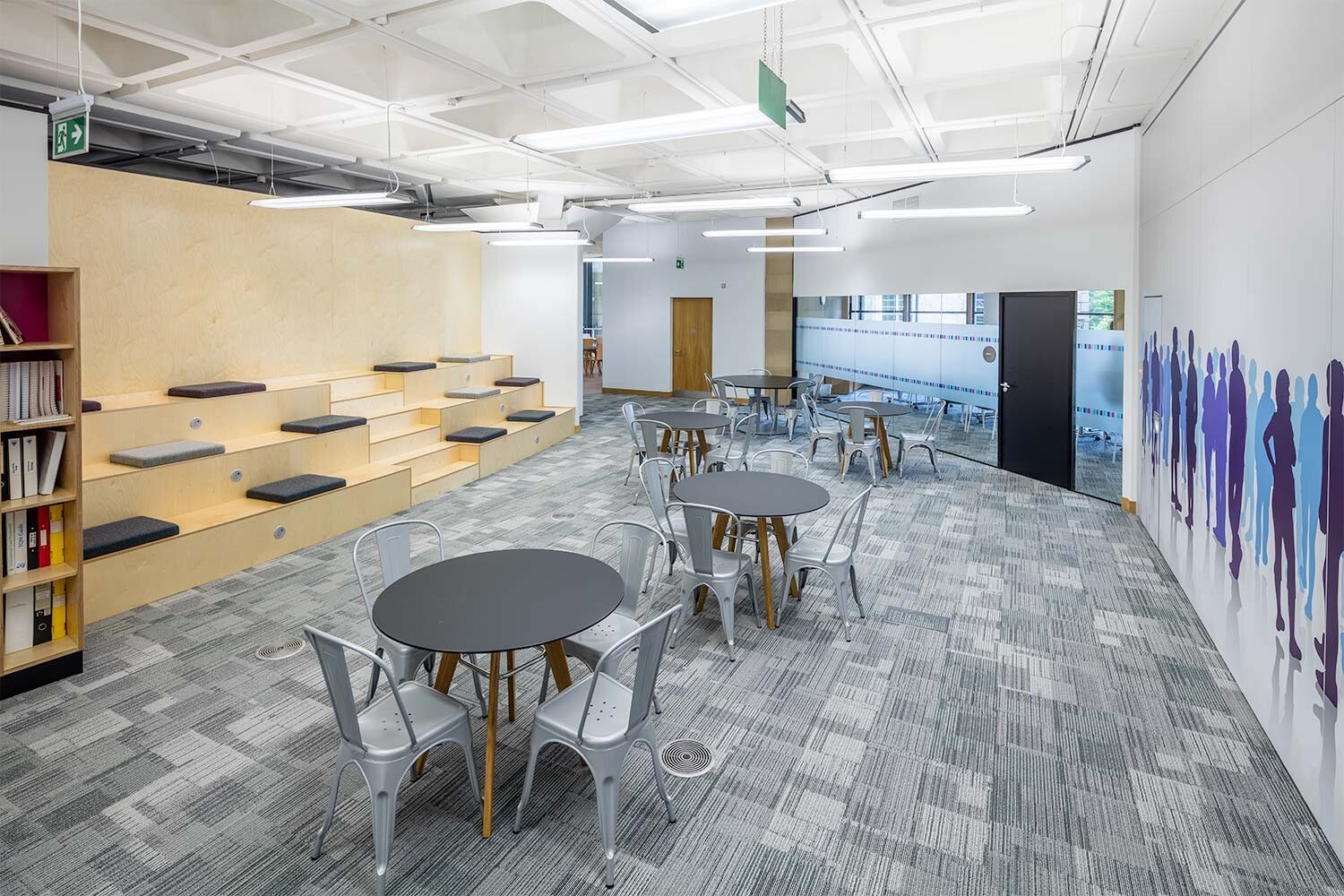
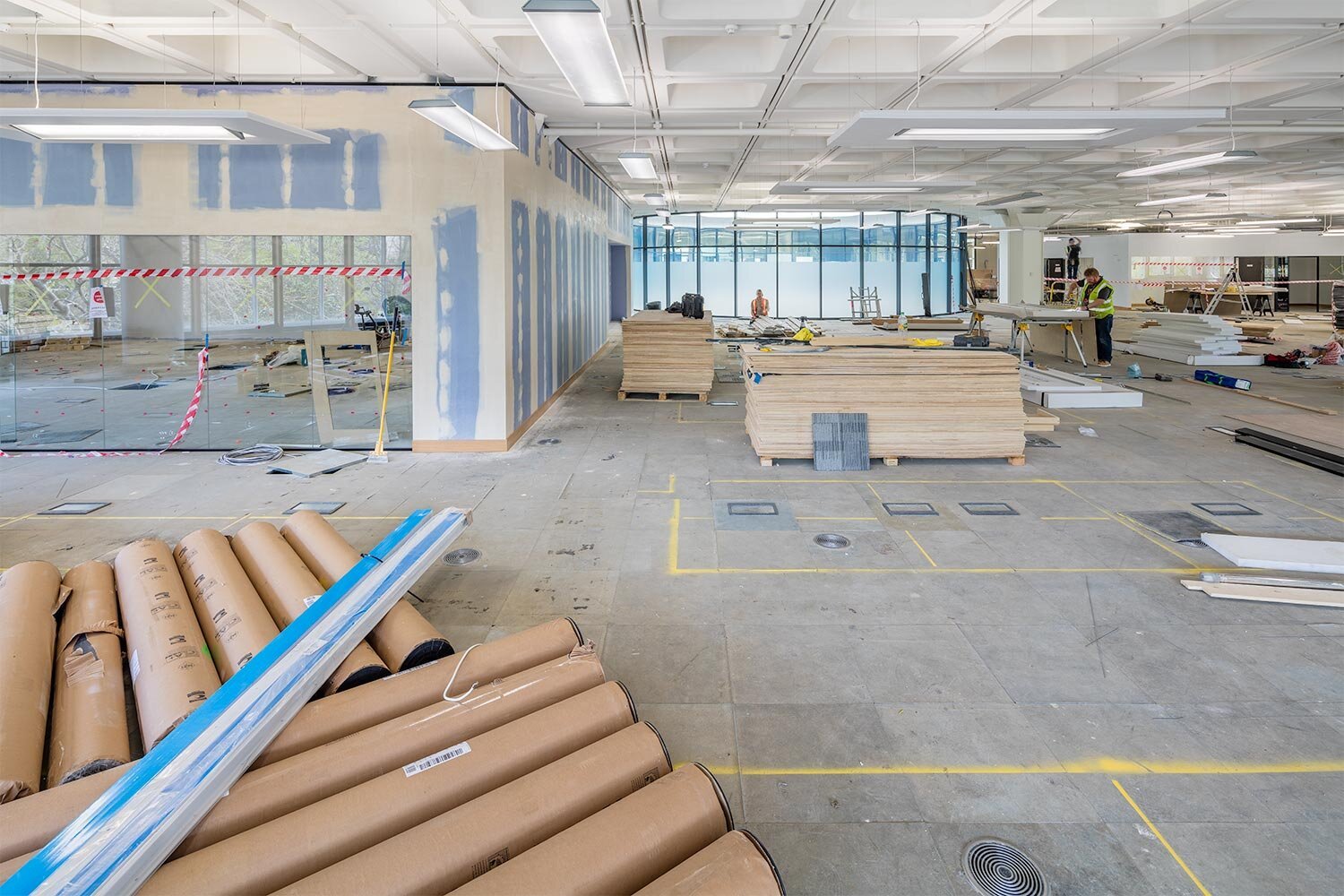
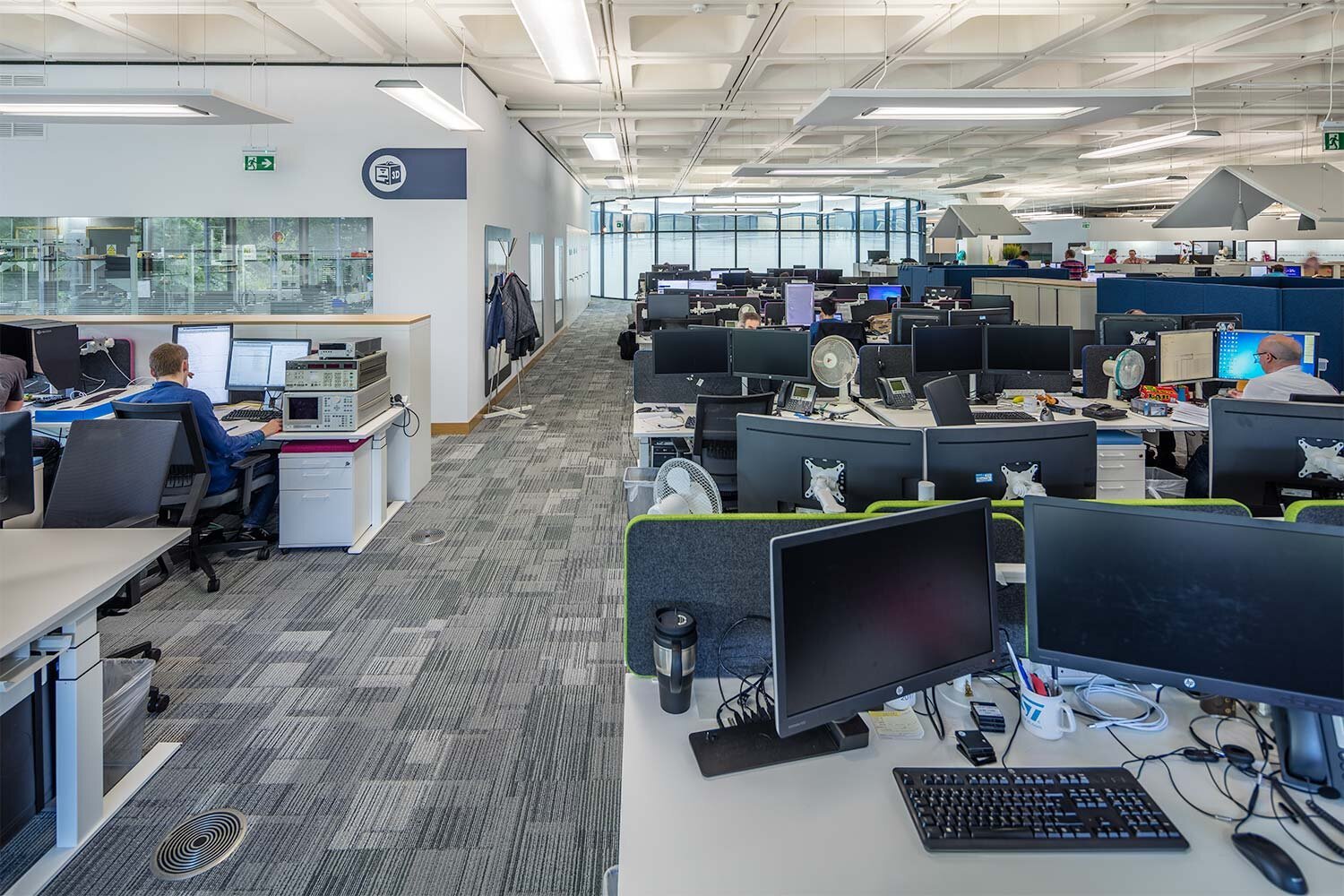
Key to the project being heralded as a success was keeping the staff on board and committed to the move. Along with this, a similar narrative meant that the new environment delivered on prospective employees’ vision of what a hi-tech firm like ST should appear like. Andy Price (Edinburgh Module Director) stated himself that he didn’t want to hear that the reason a recruit didn’t join was because of poor quality office was ever repeated!
Canteen and break out area
A large portion of the available space was carefully designed around the laboratory and dark room requirements. Specifications included compressed air, clean power and uprated flooring to take the heavy equipment that was to come. As part of this, a fire strategy had to be incorporated so that staff can escape from a darkroom in the event of a general evacuation alarm being given.
An advantage of the Tanfield space in Edinburgh is rather than being spread over 2 floors (which was the case in their old offices), all of the staff are on the same level and already the benefits are being reaped. A spread of informal and formal meeting spaces have been incorporated into the design. This allows staff to meet and discuss projects much more informally in a selection of spaces. Research tells us that when given a variety of spaces, both in terms of location and style, staff are much more likely to benefit both in terms of communication and positive outcomes.
There were 1 or 2 pieces in the puzzle that were picked up on very early in the interior design and office fit out project and the Amos Beech team were keen to preserve them. The first was table tennis, in the early days there was a table tennis table and this had disappeared as lack of available space dictated. This has been reinstated and it is use almost continuously throughout the day.
Operable Moving Wall
The second point was a space where all of the staff could gather for company announcements. A town hall space has been incorporated complete with tiered seating which when used with an operable wall, the whole space can be opened up to seat 150 staff every 4-6 months.
Wall closed
Wall open
All staff sit at electrically adjustable sit/stand workstations and it is interesting to see how this added functionality is actually being used by everyone.
What is more interesting is that previously the staff worked from old fashioned ‘corner’ desks with side extensions giving them 2.4m x 2.2m footprints and now they all work from 1600x800 workstations with dual monitor arms. And there are no complaints! Feedback has been nothing but positive and it is clear that everyone is very proud of their new environment.
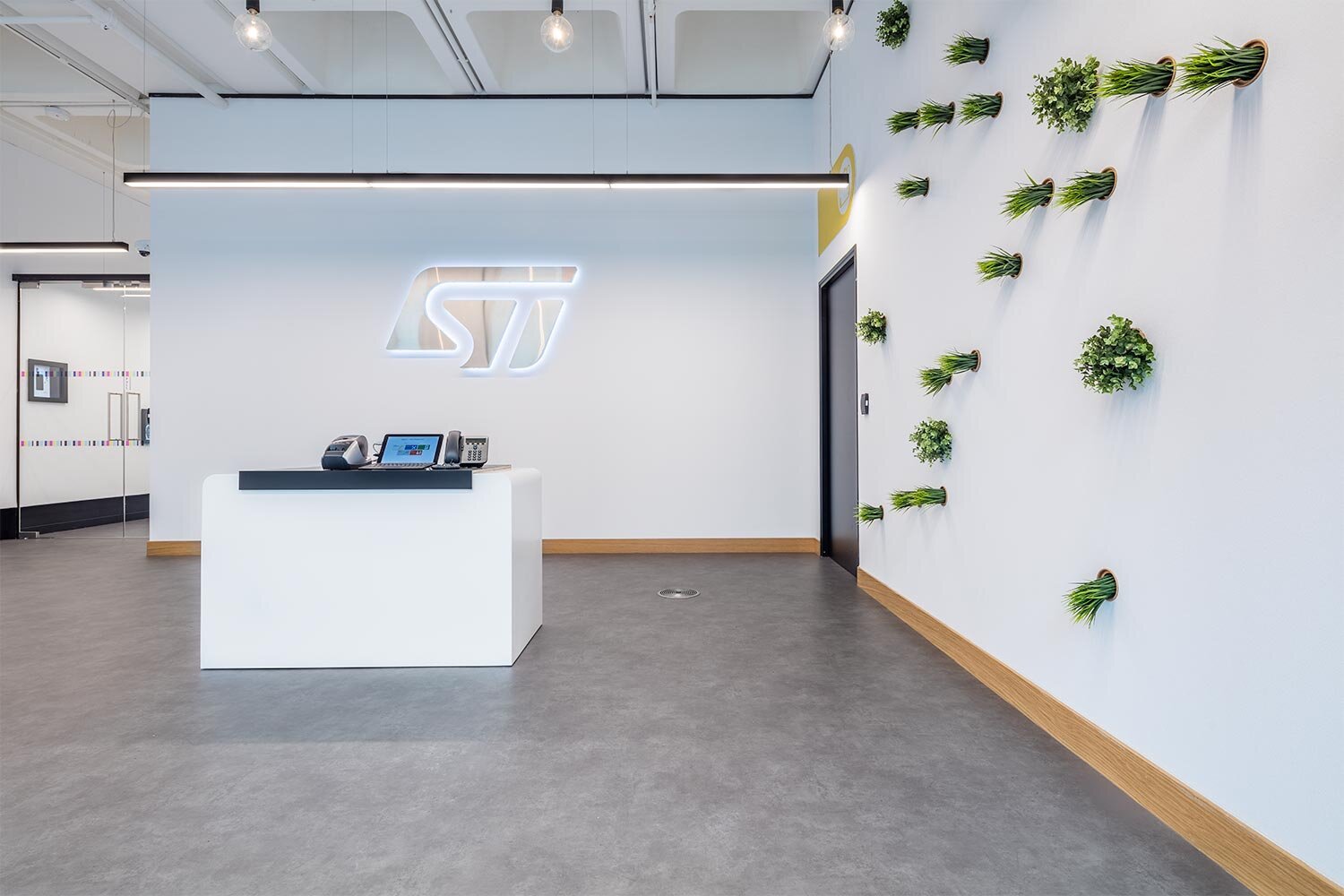
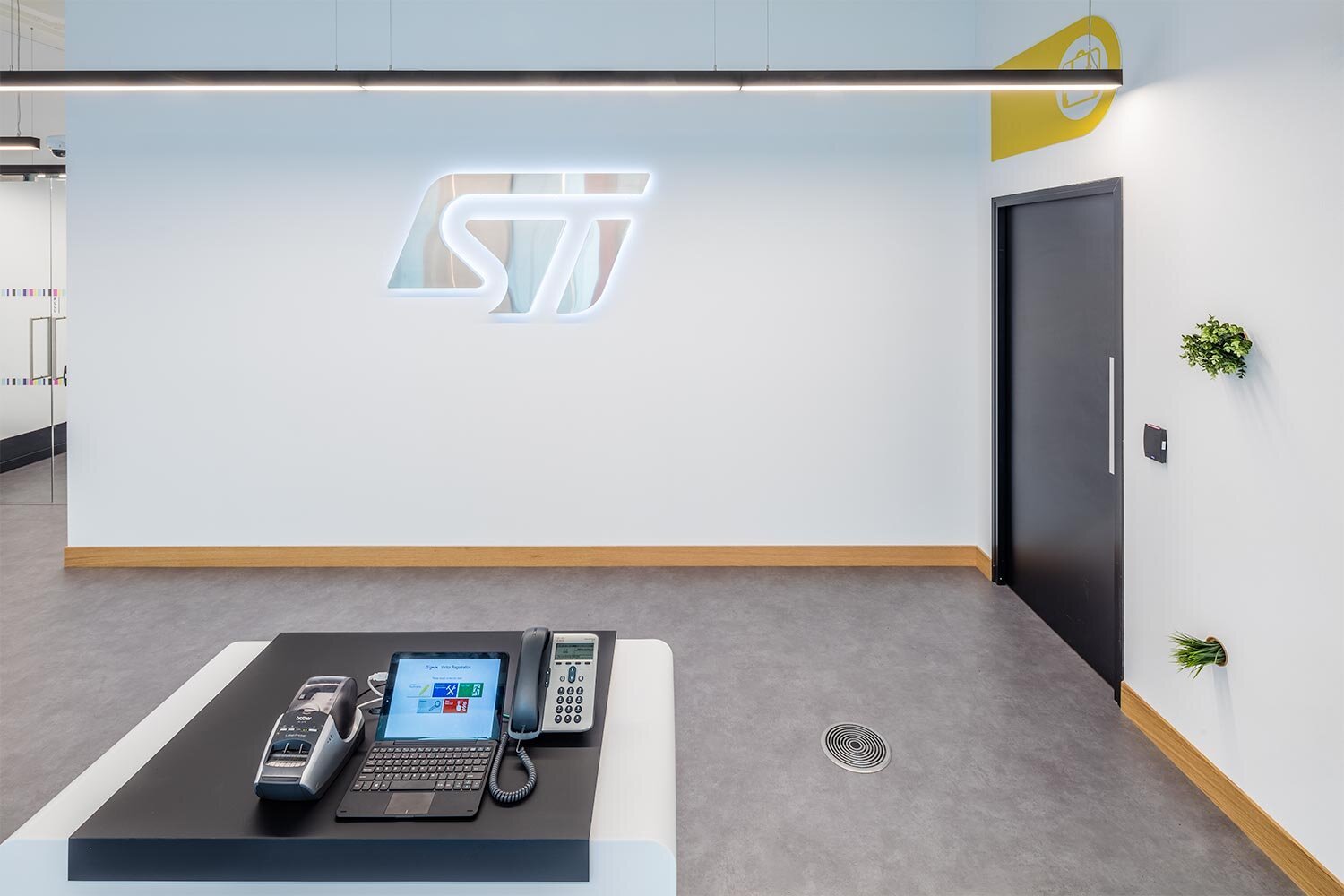
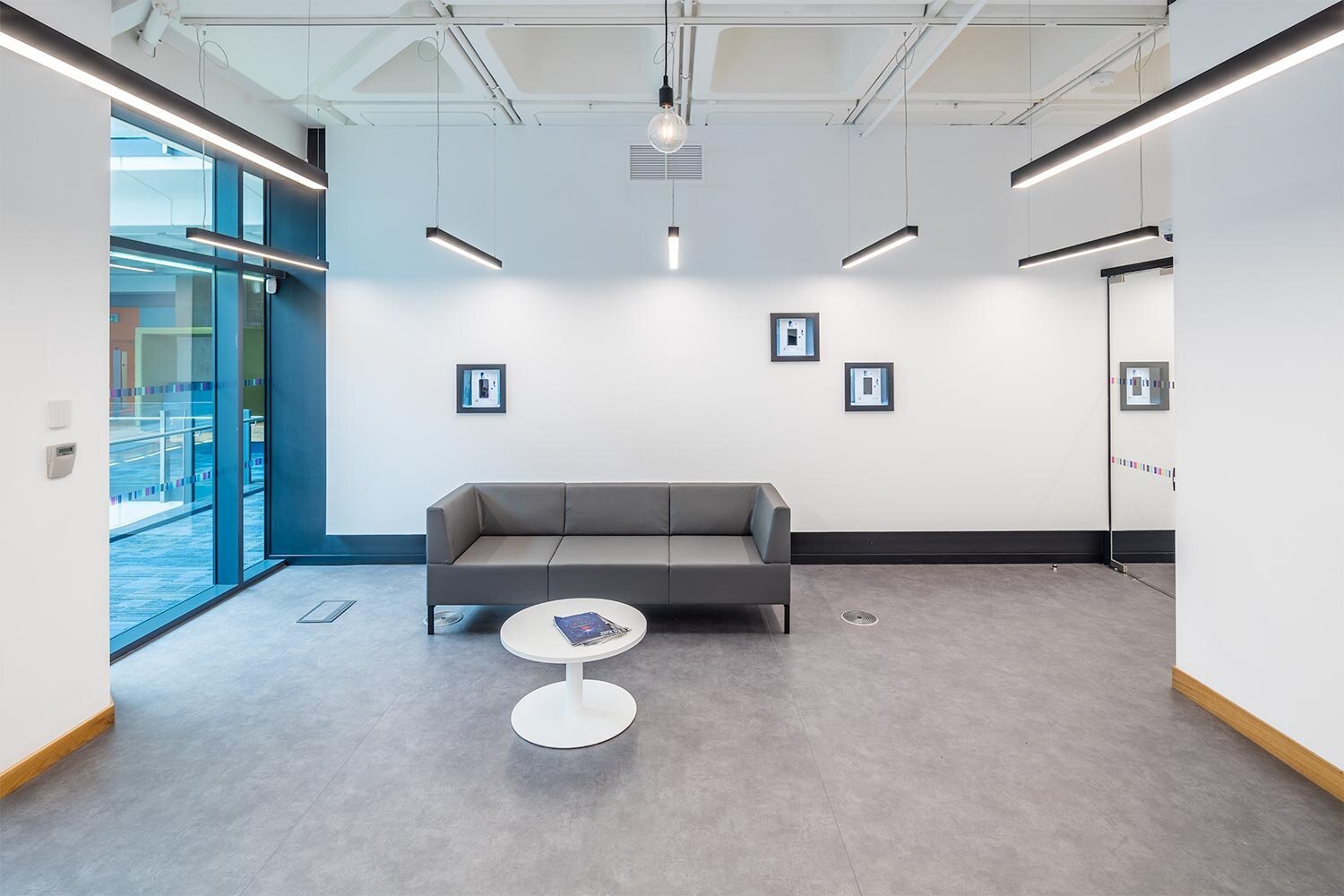
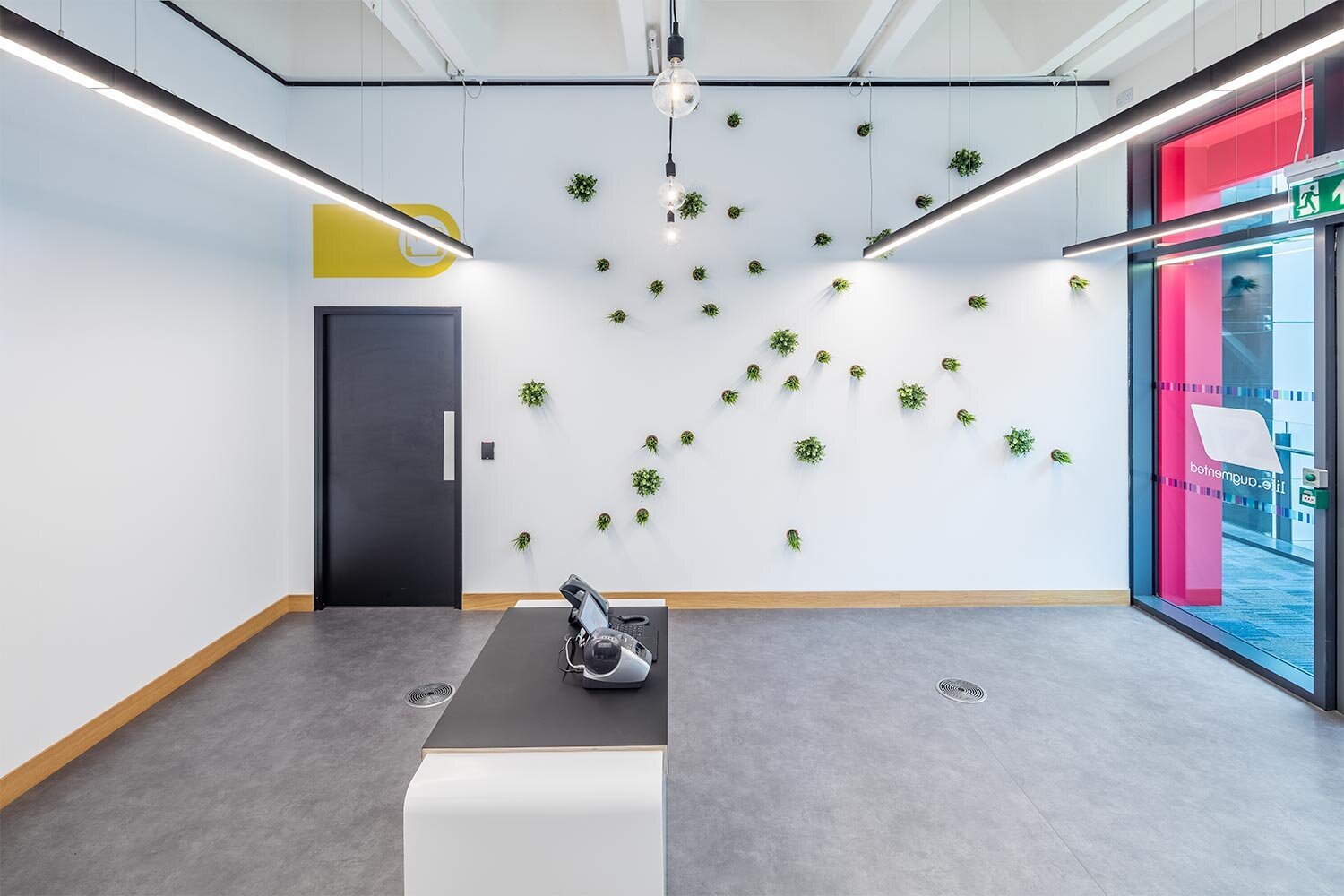
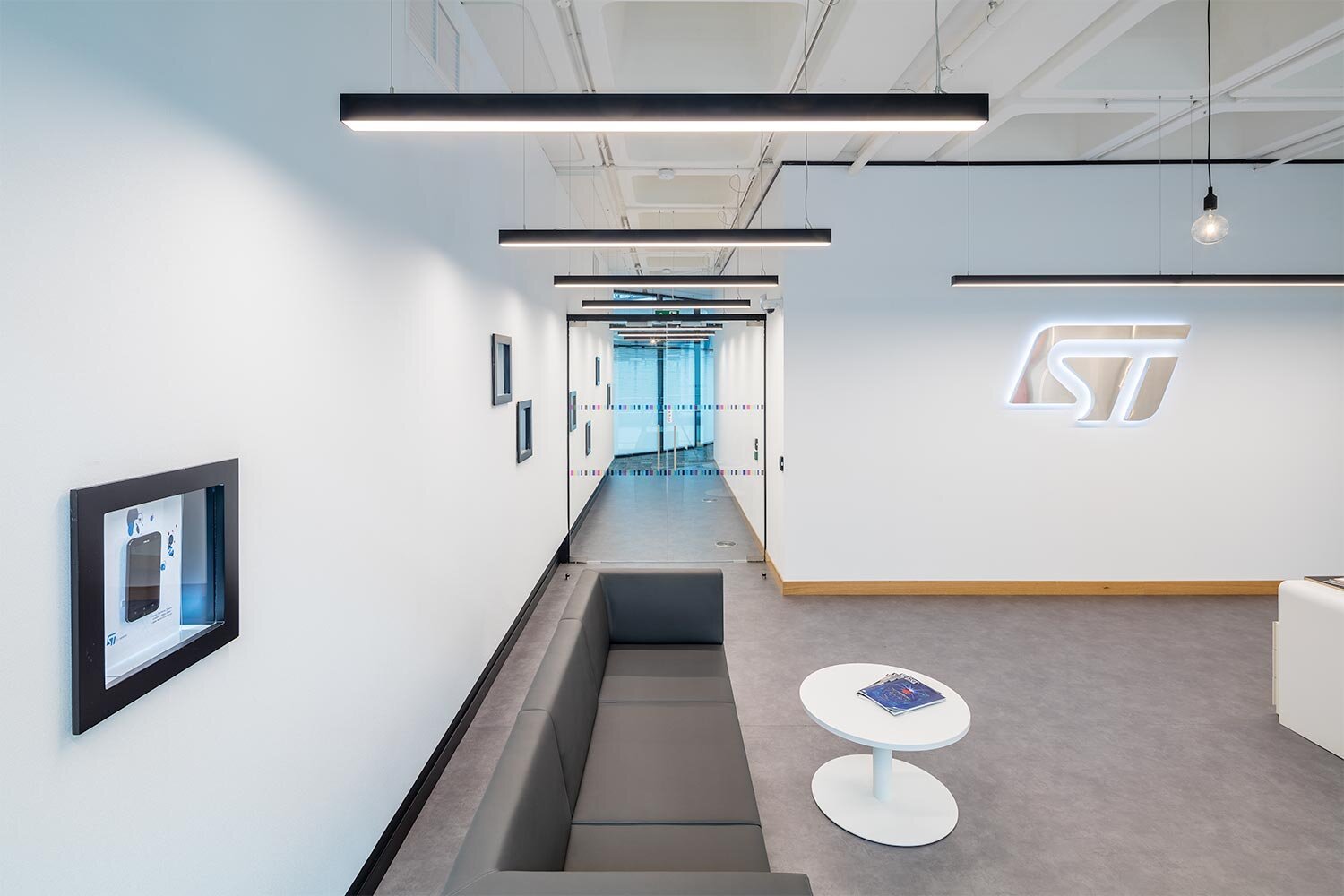
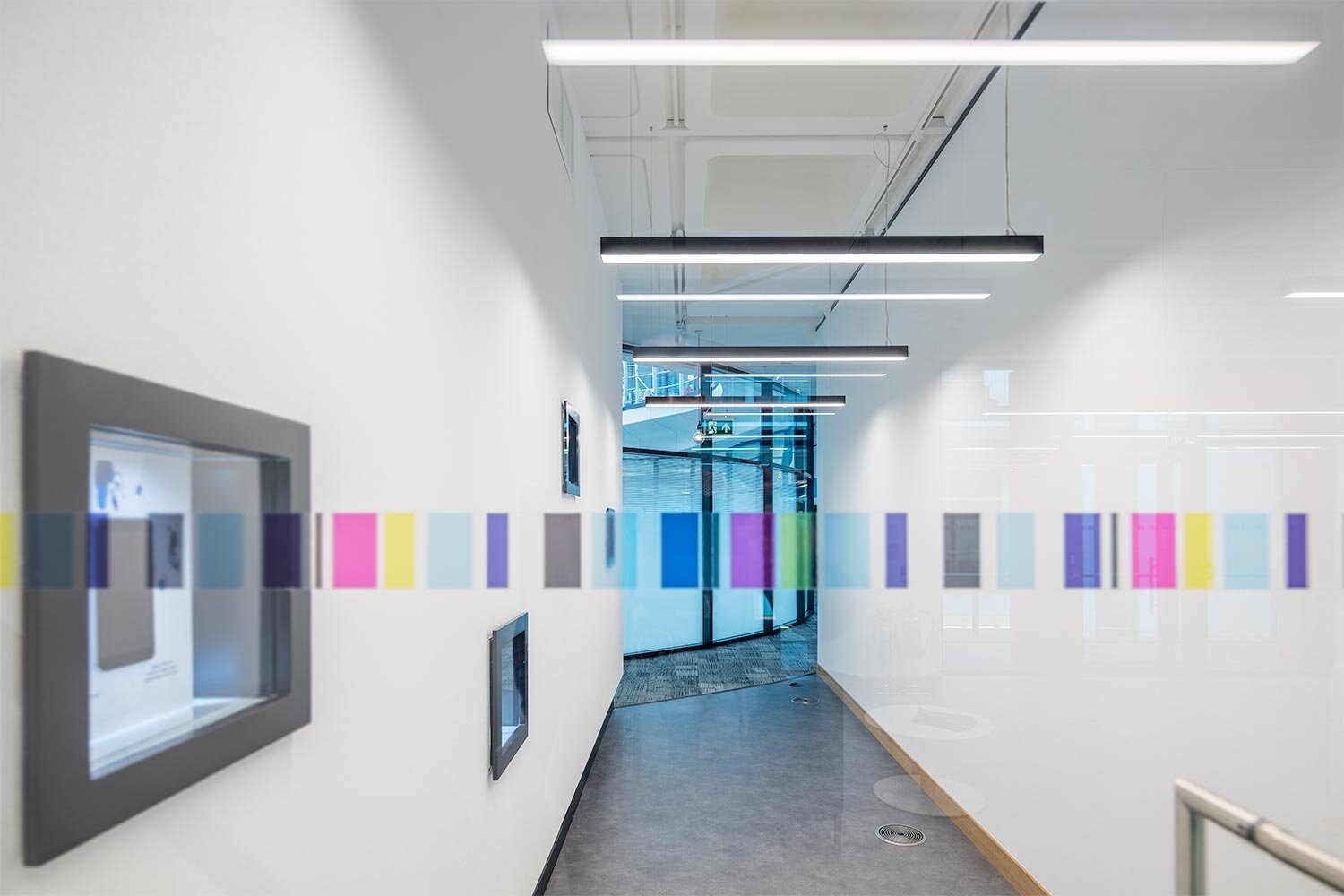
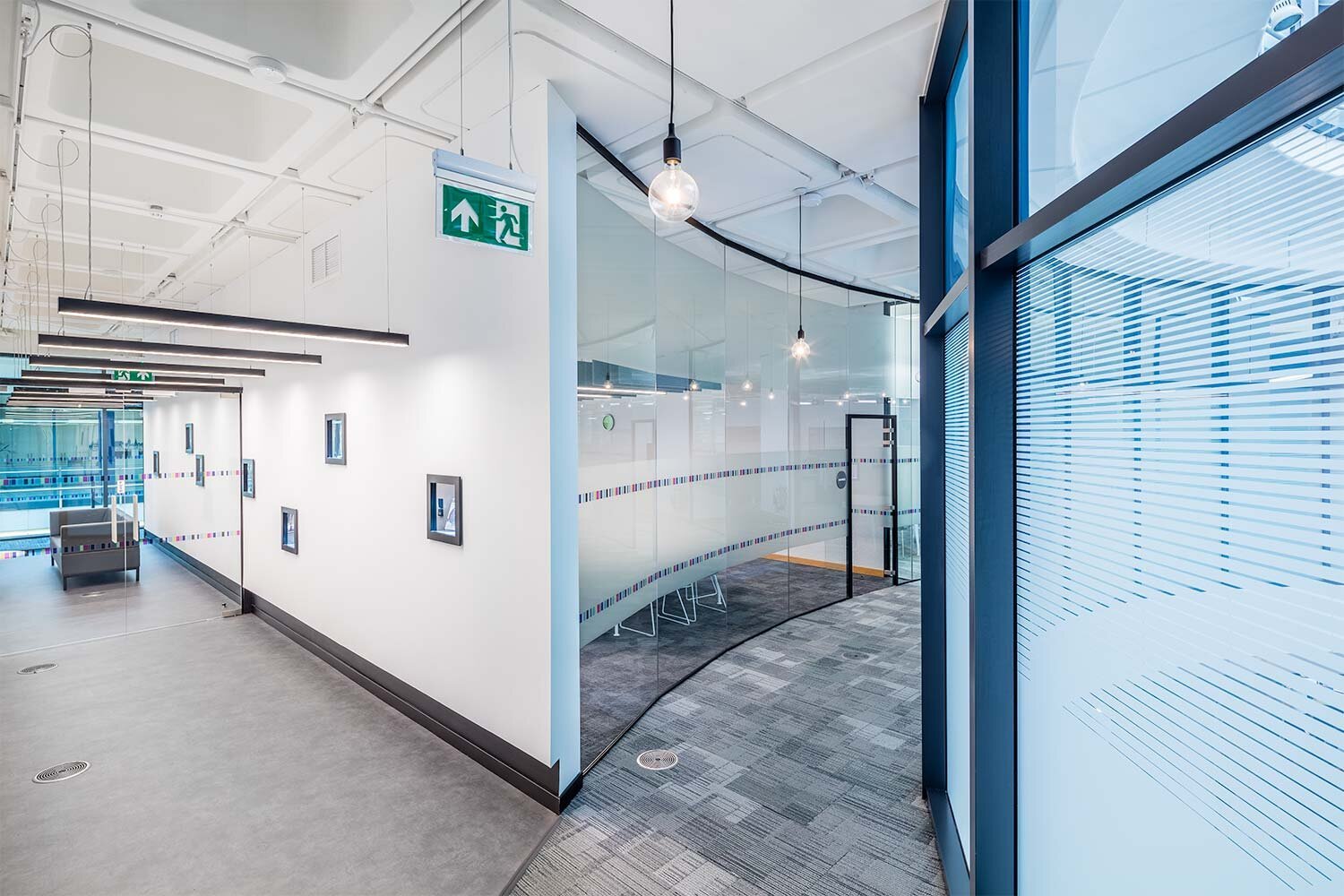
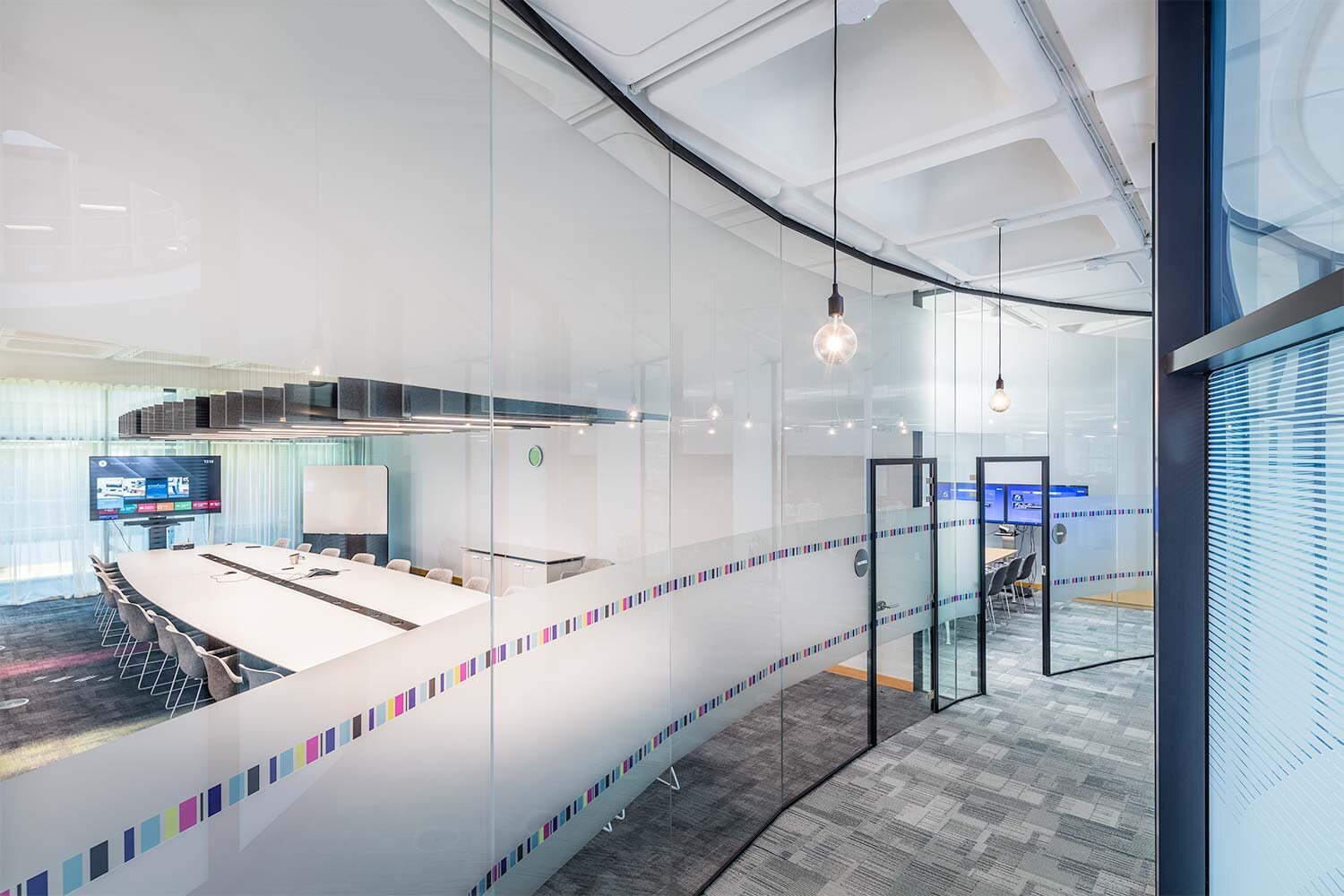
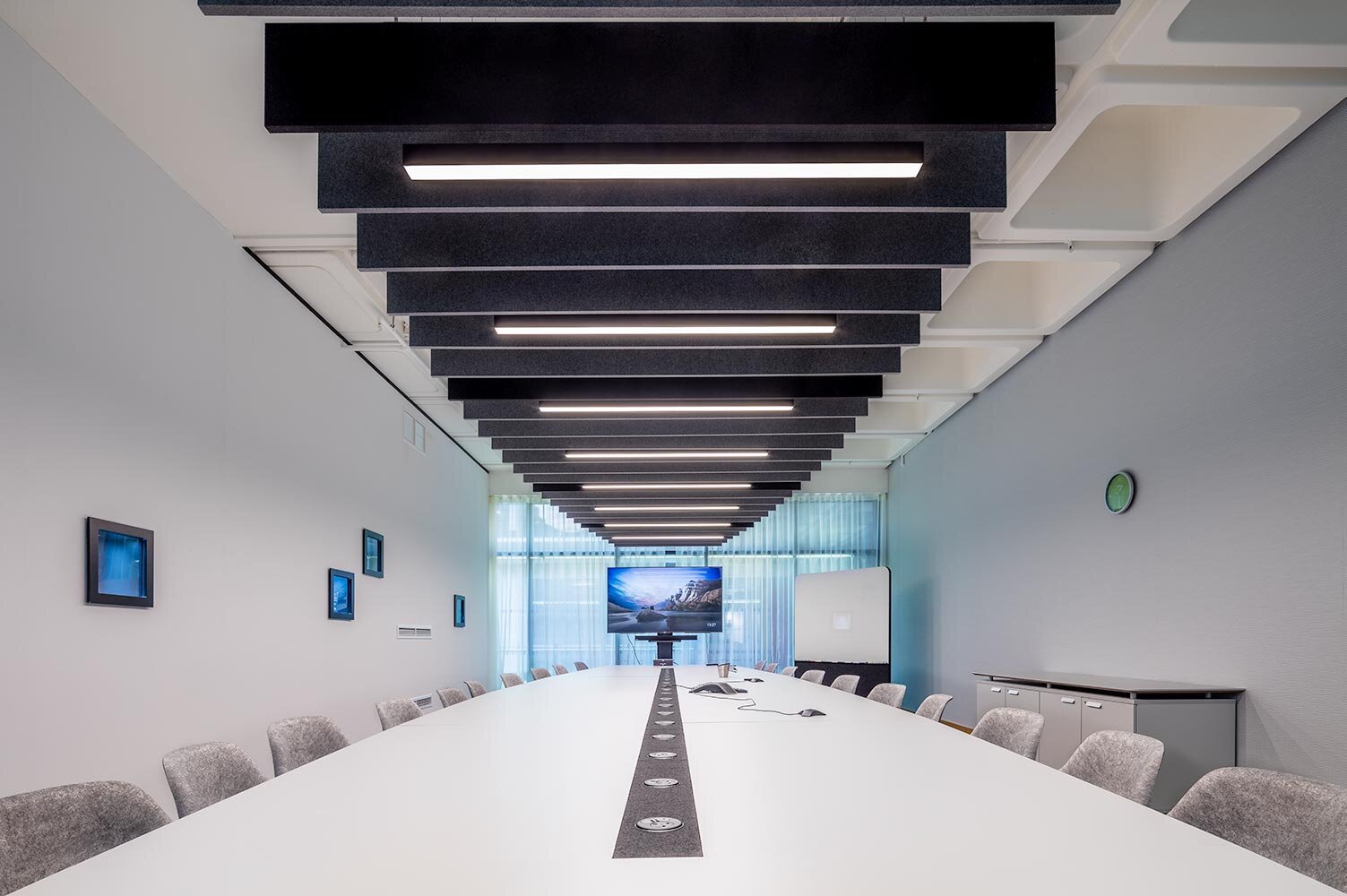
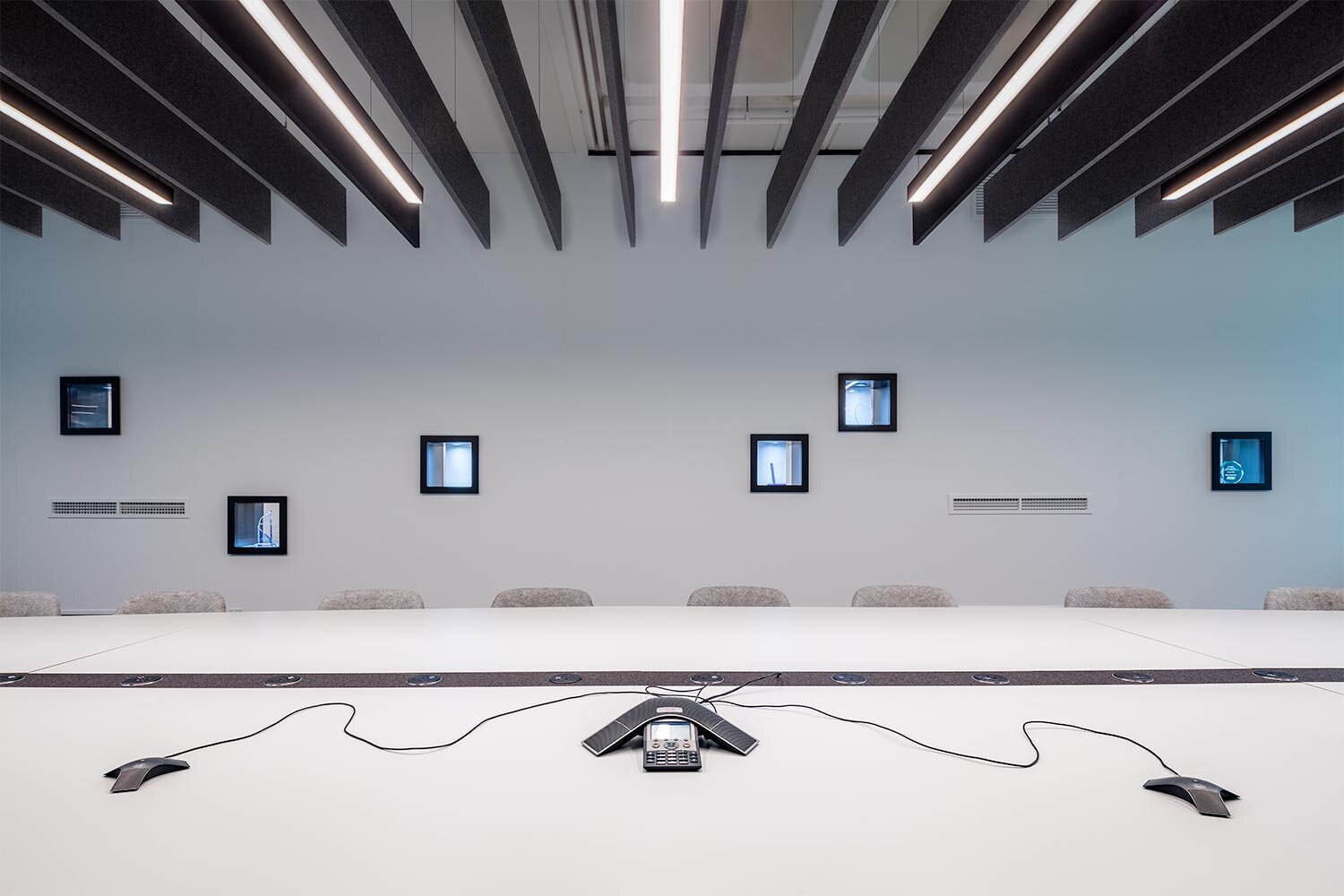
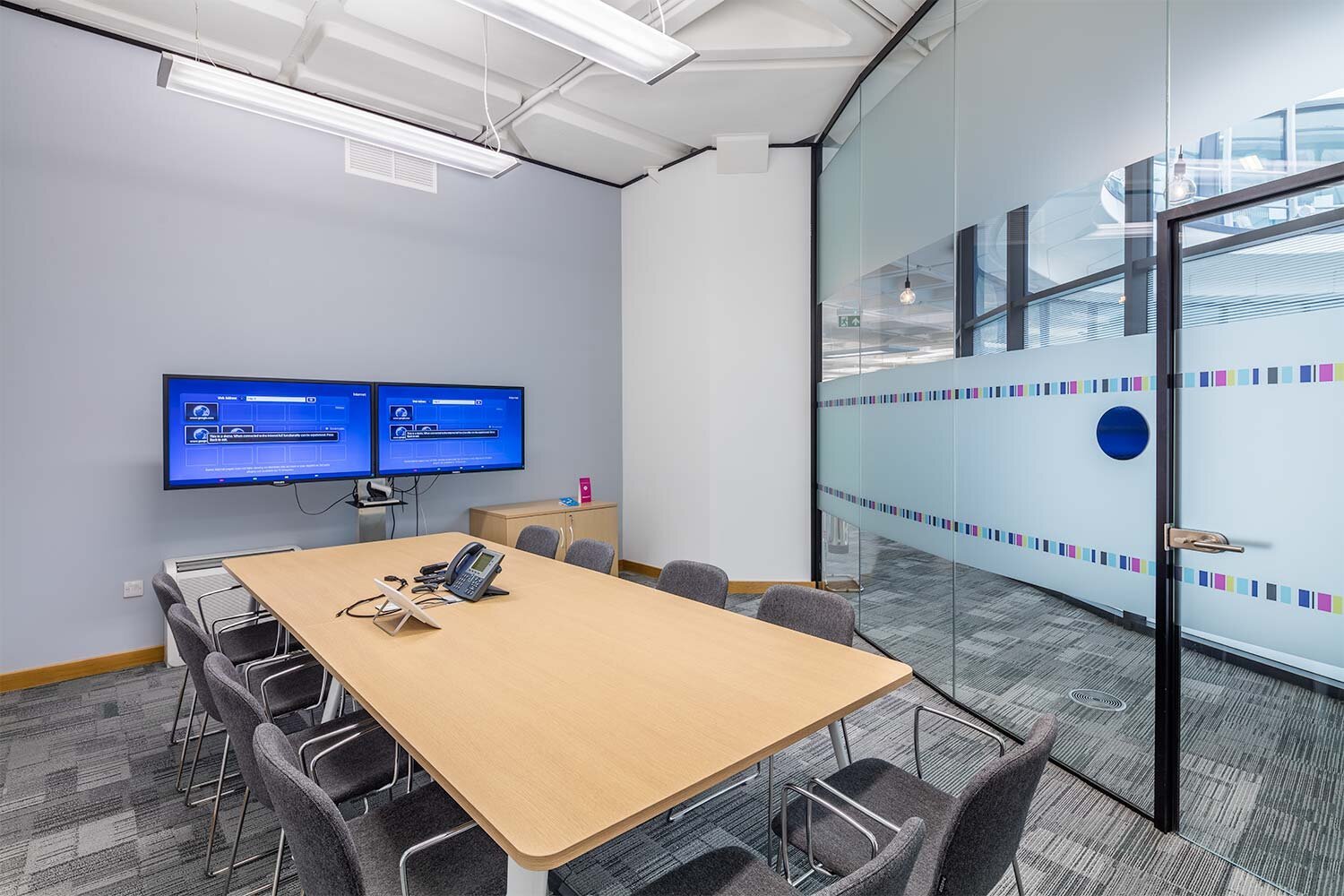
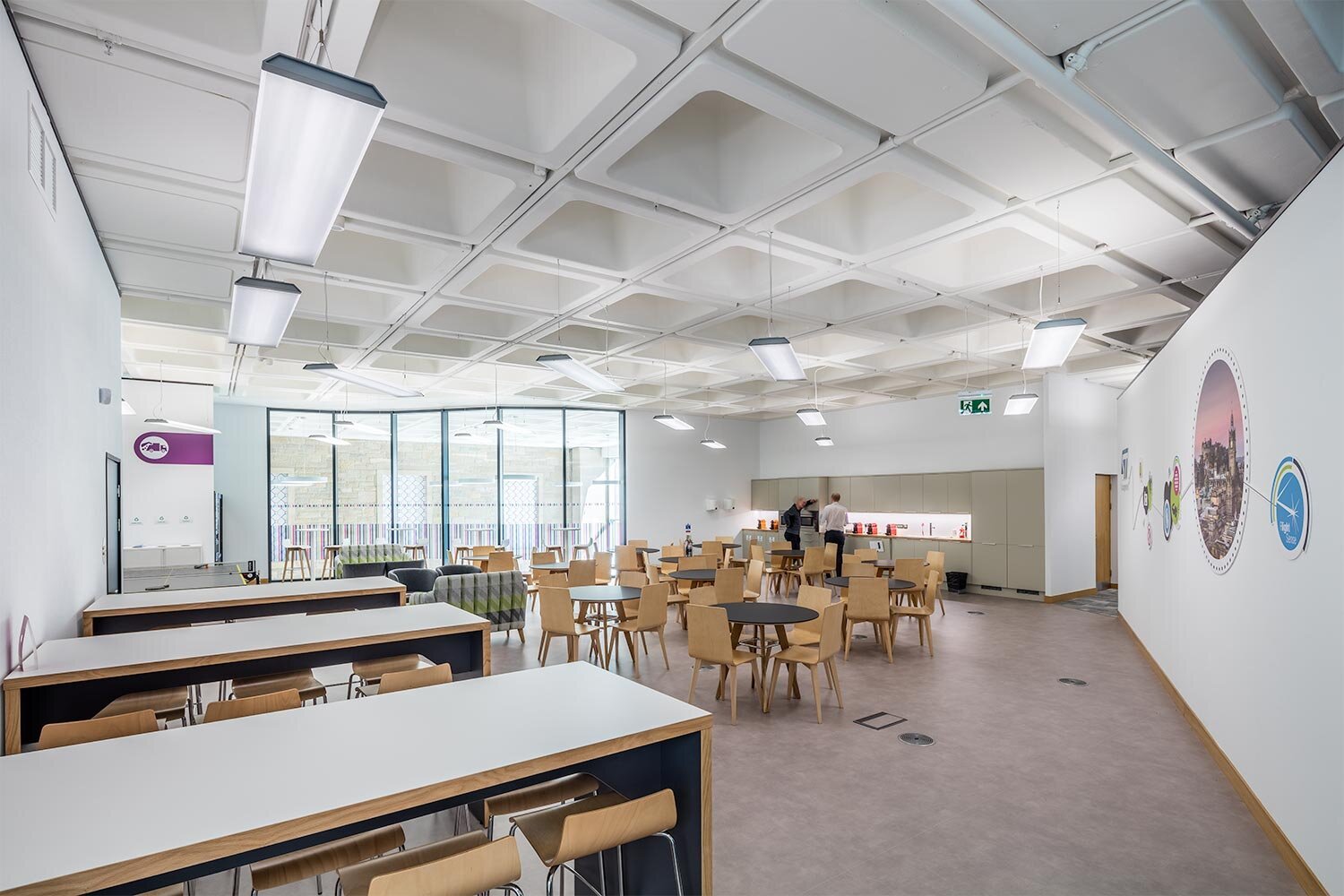
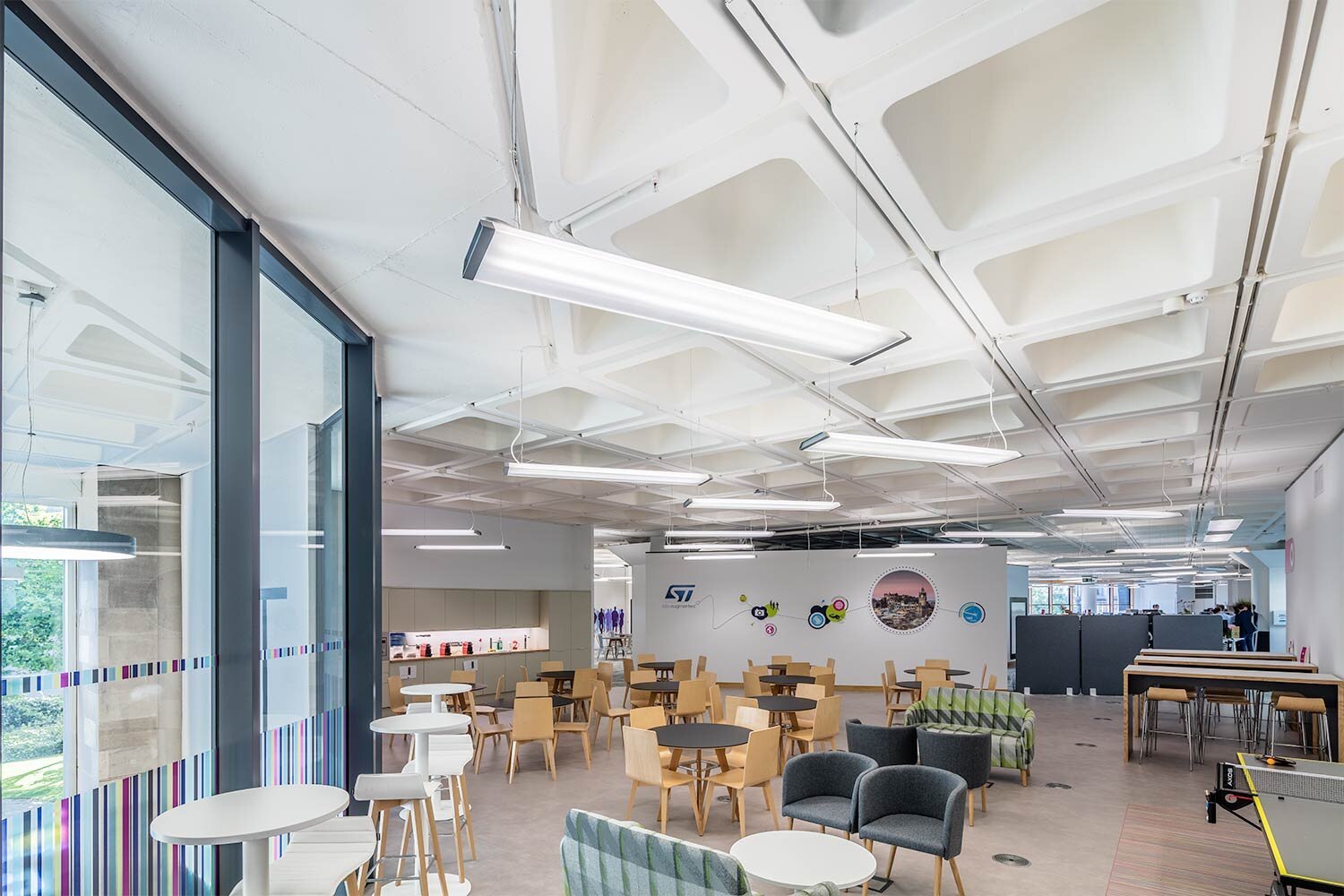
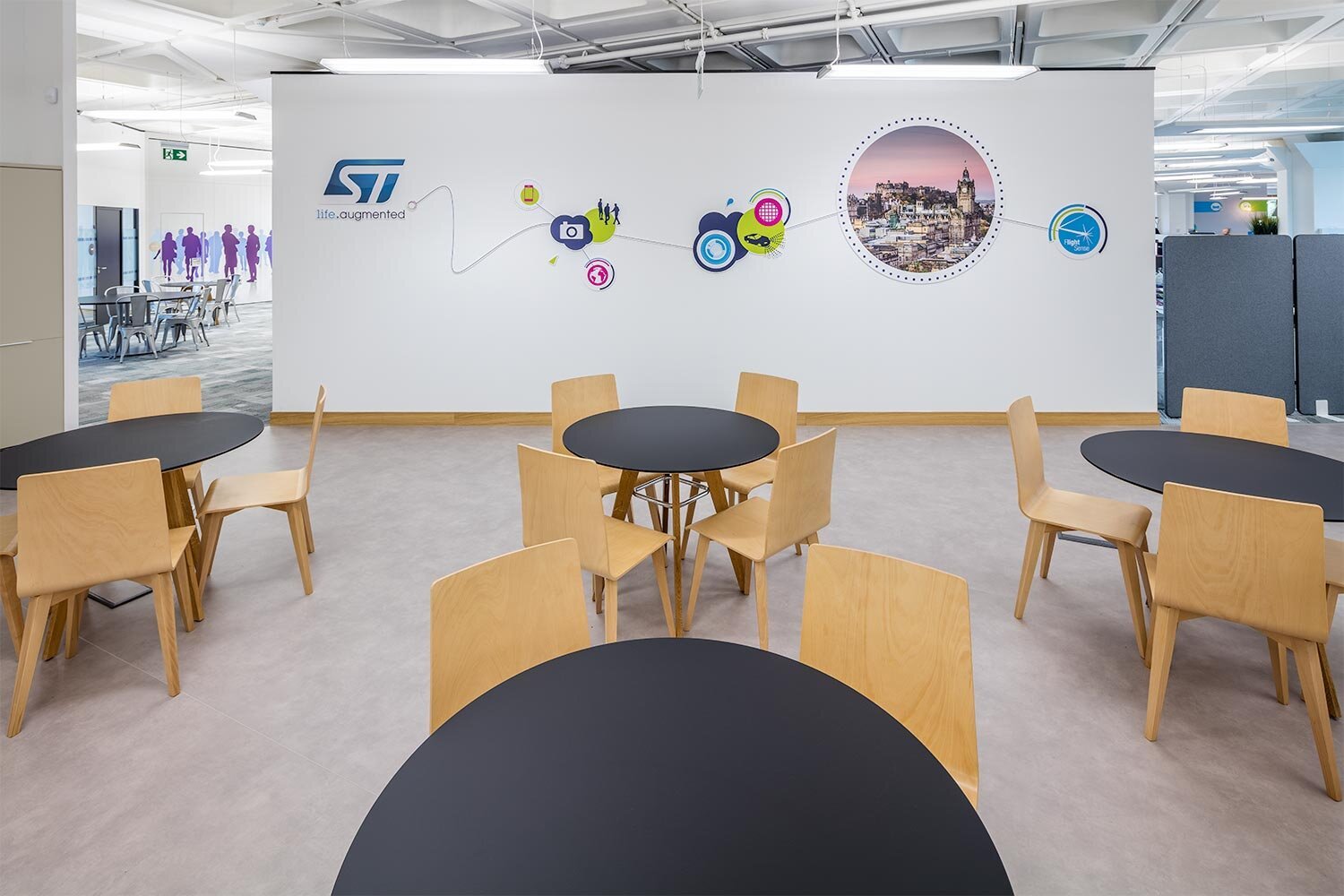
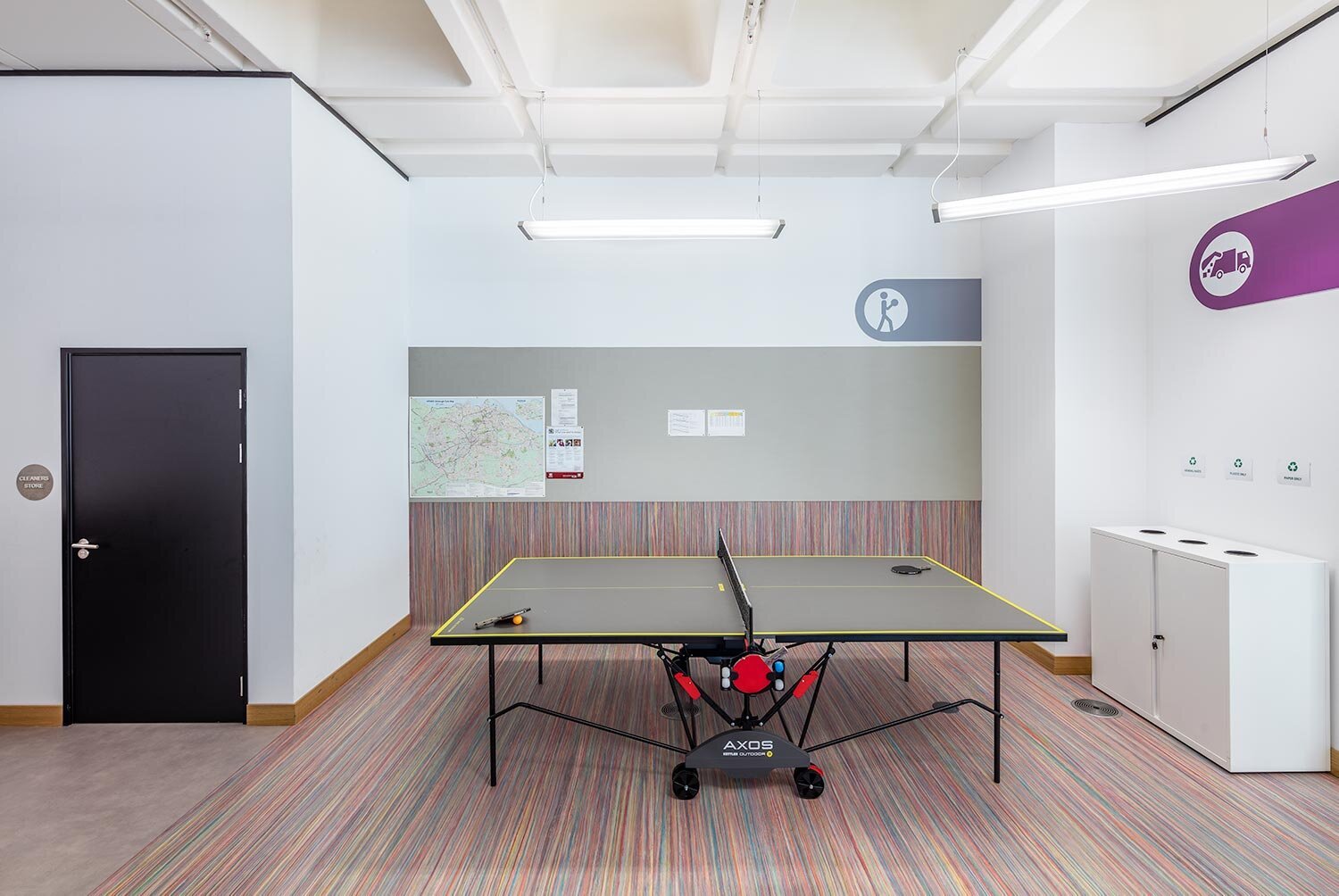
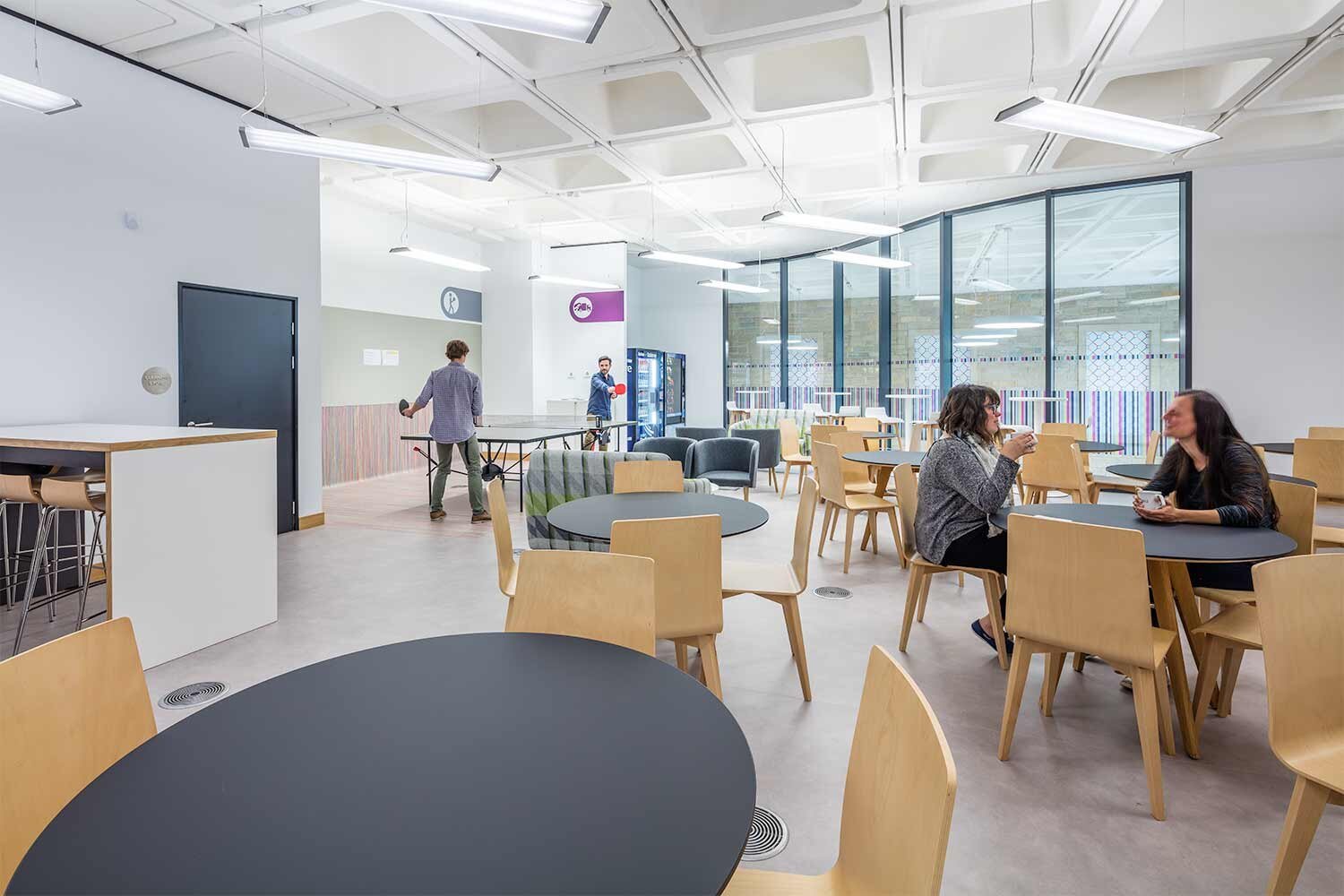
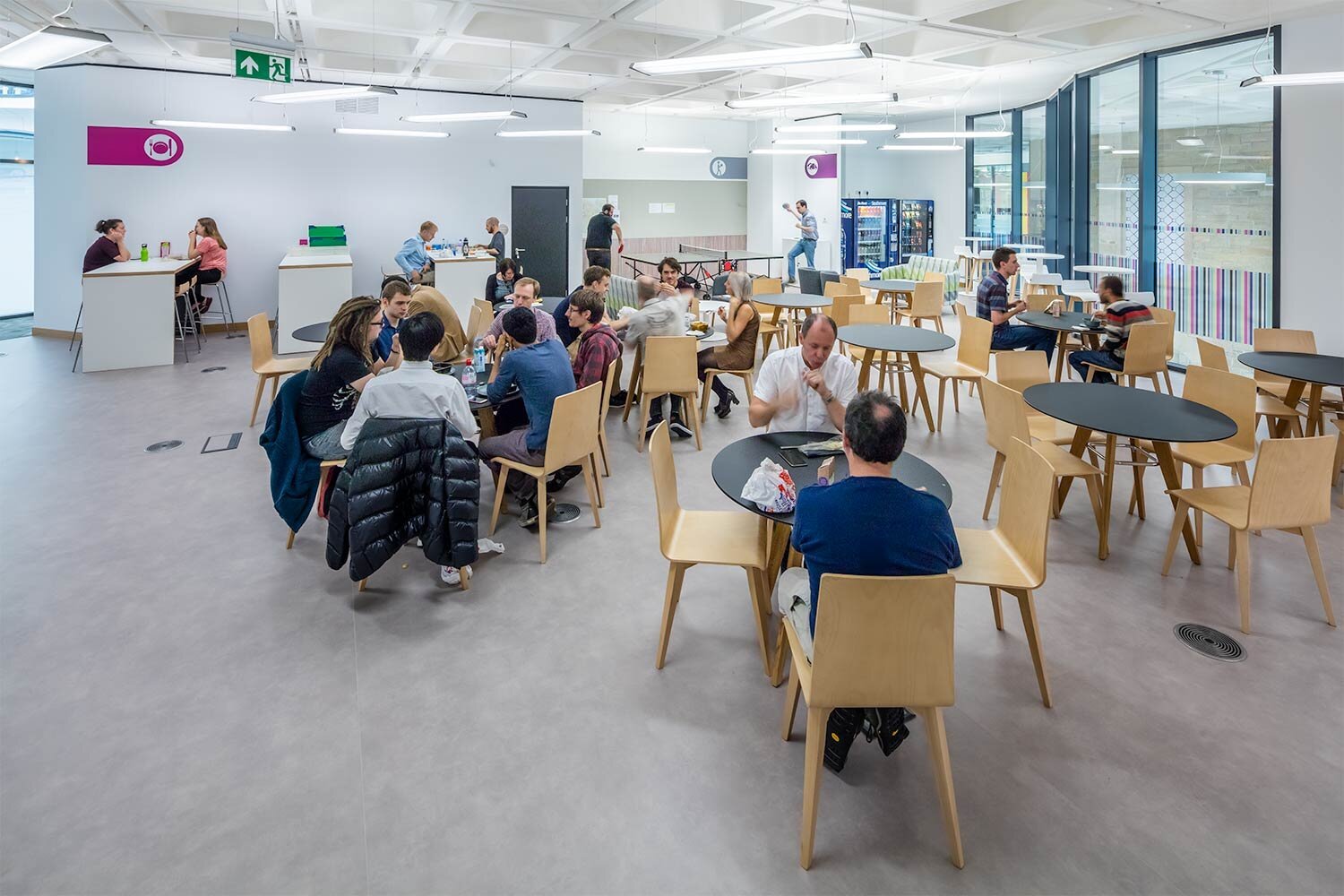
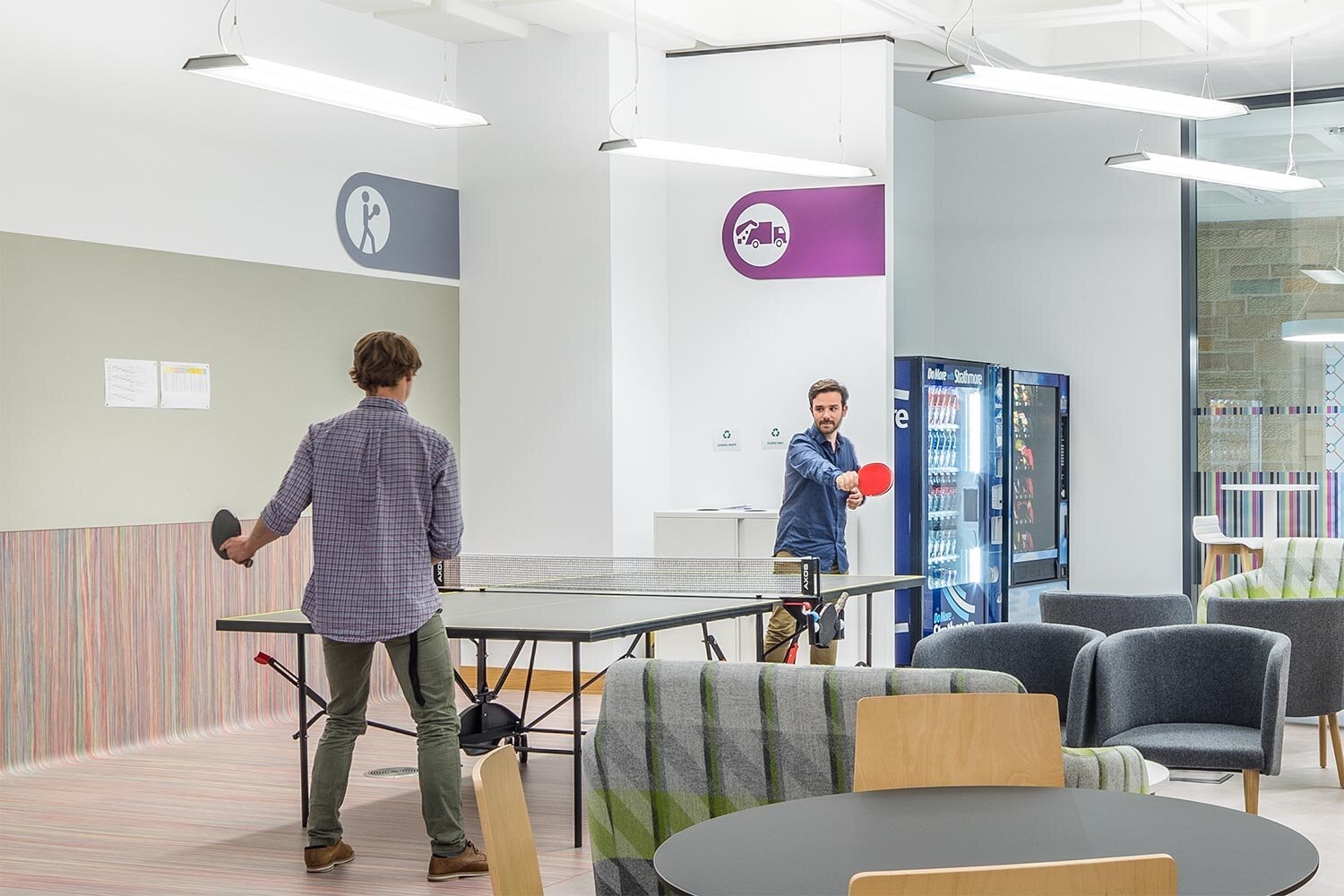
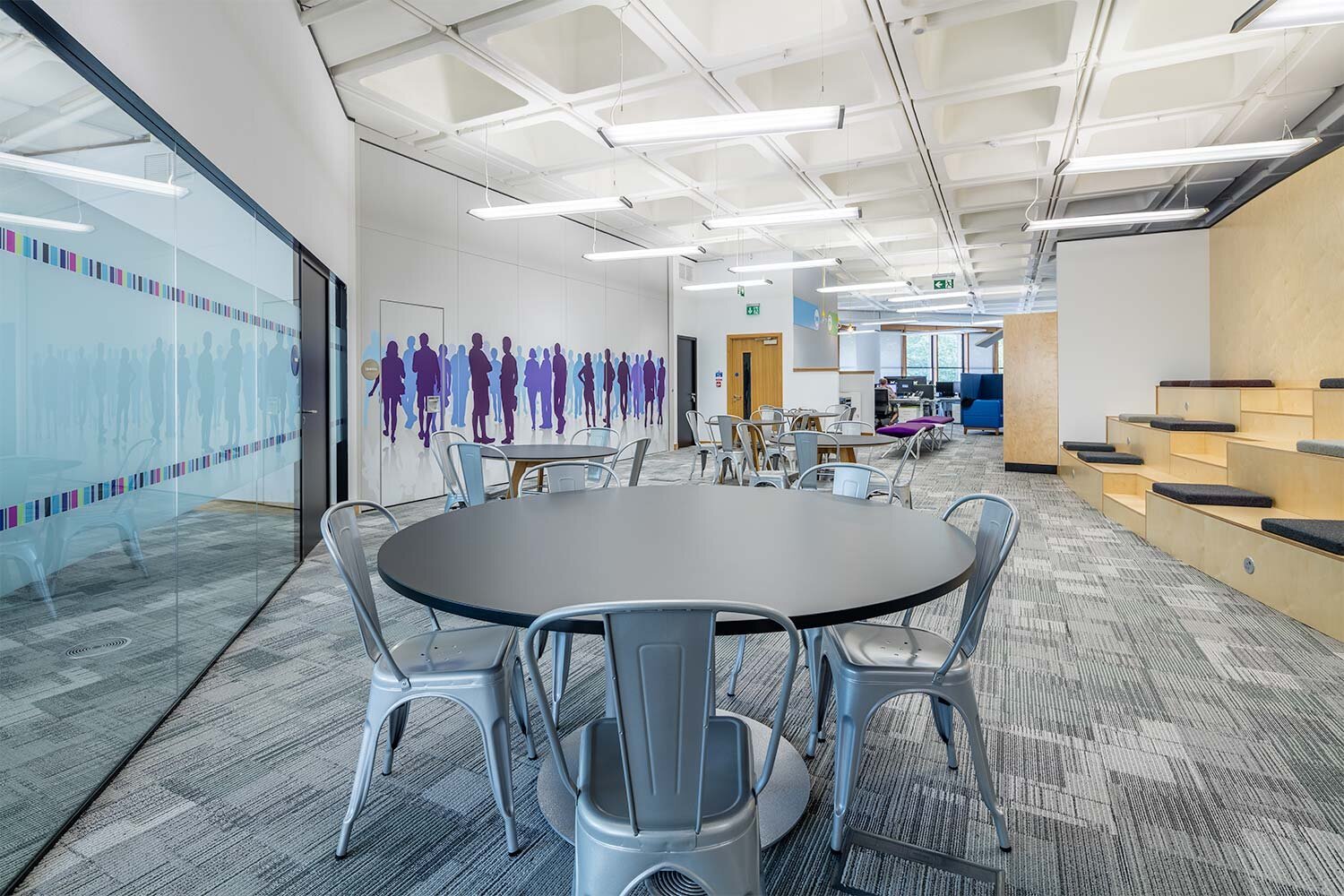
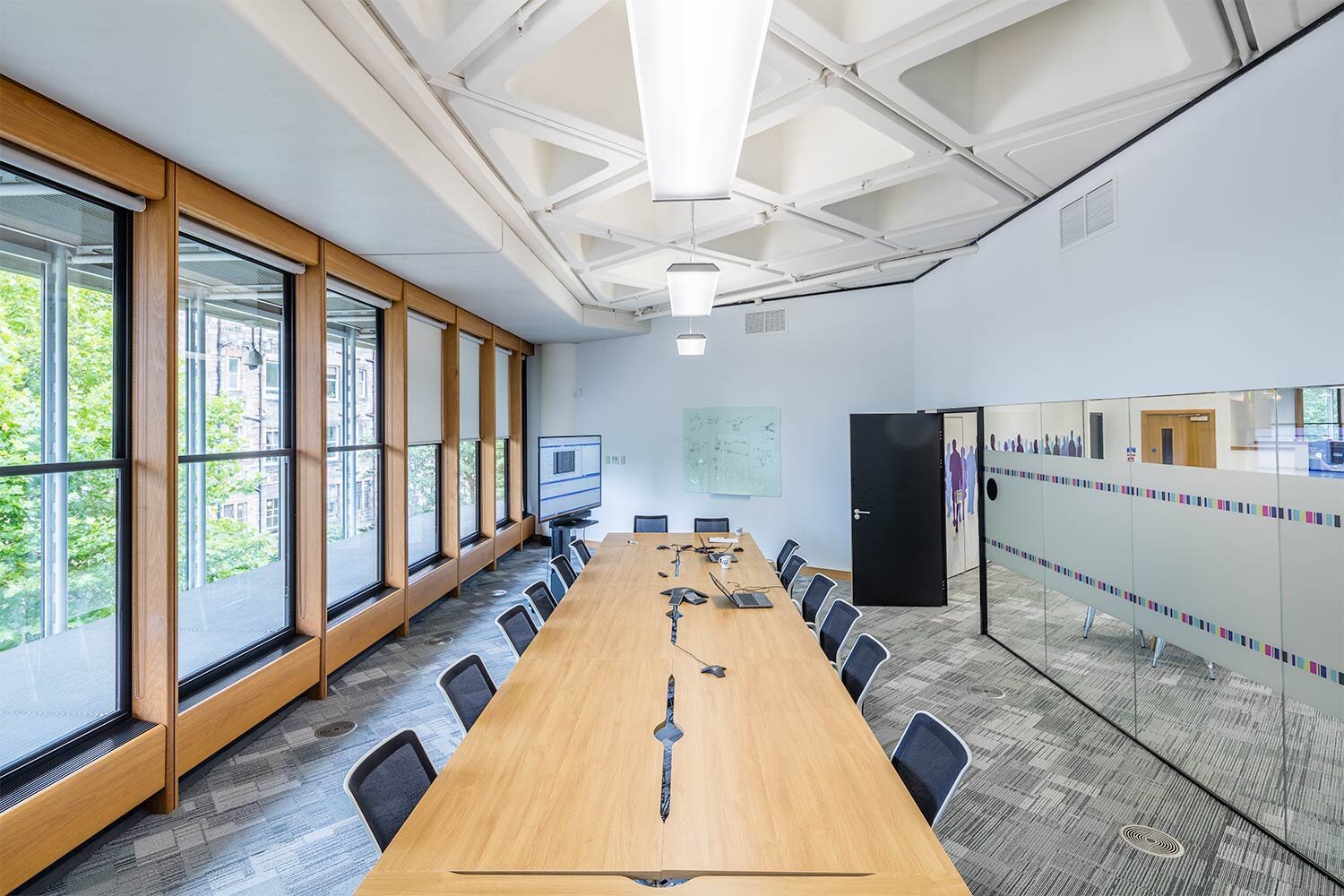
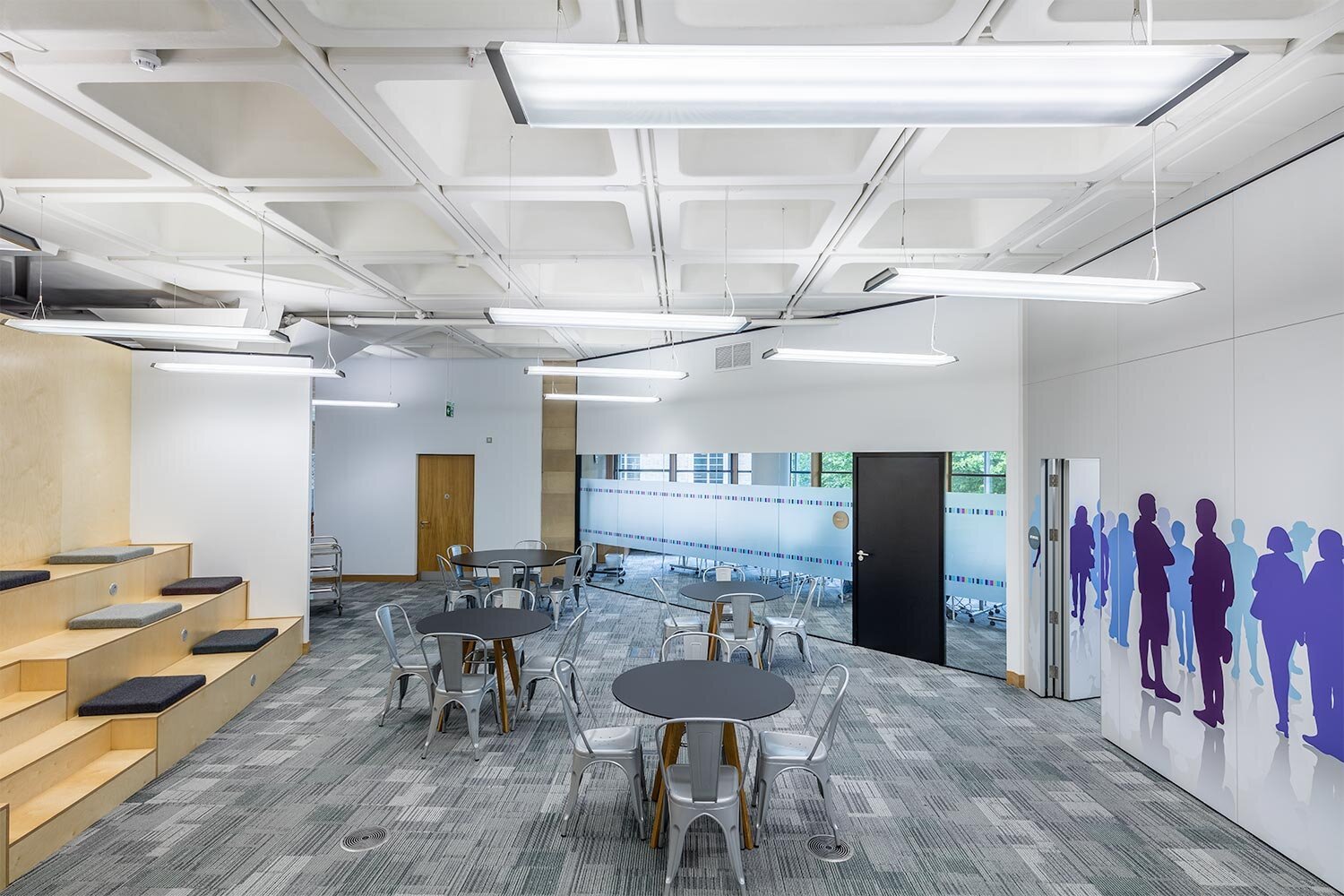
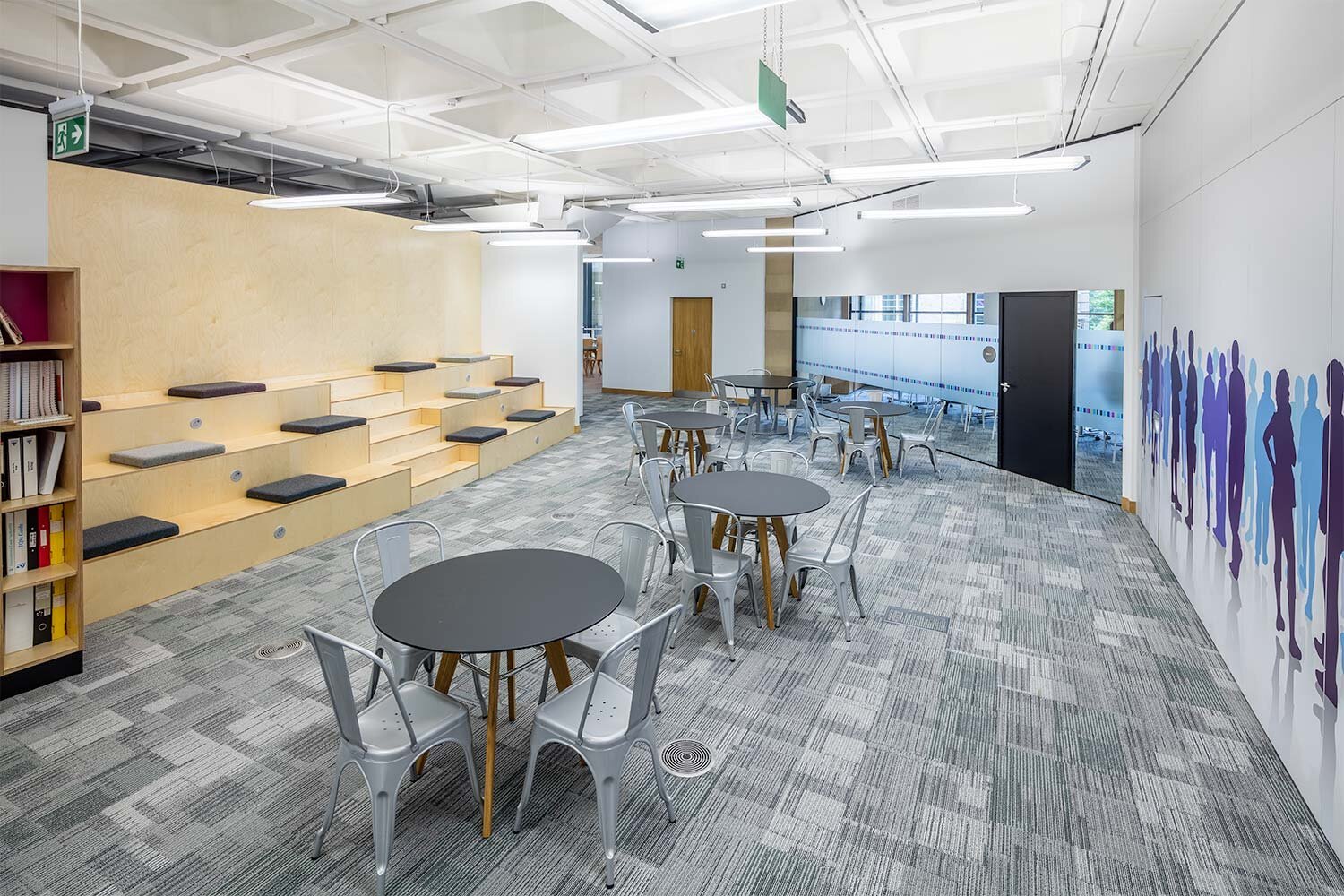
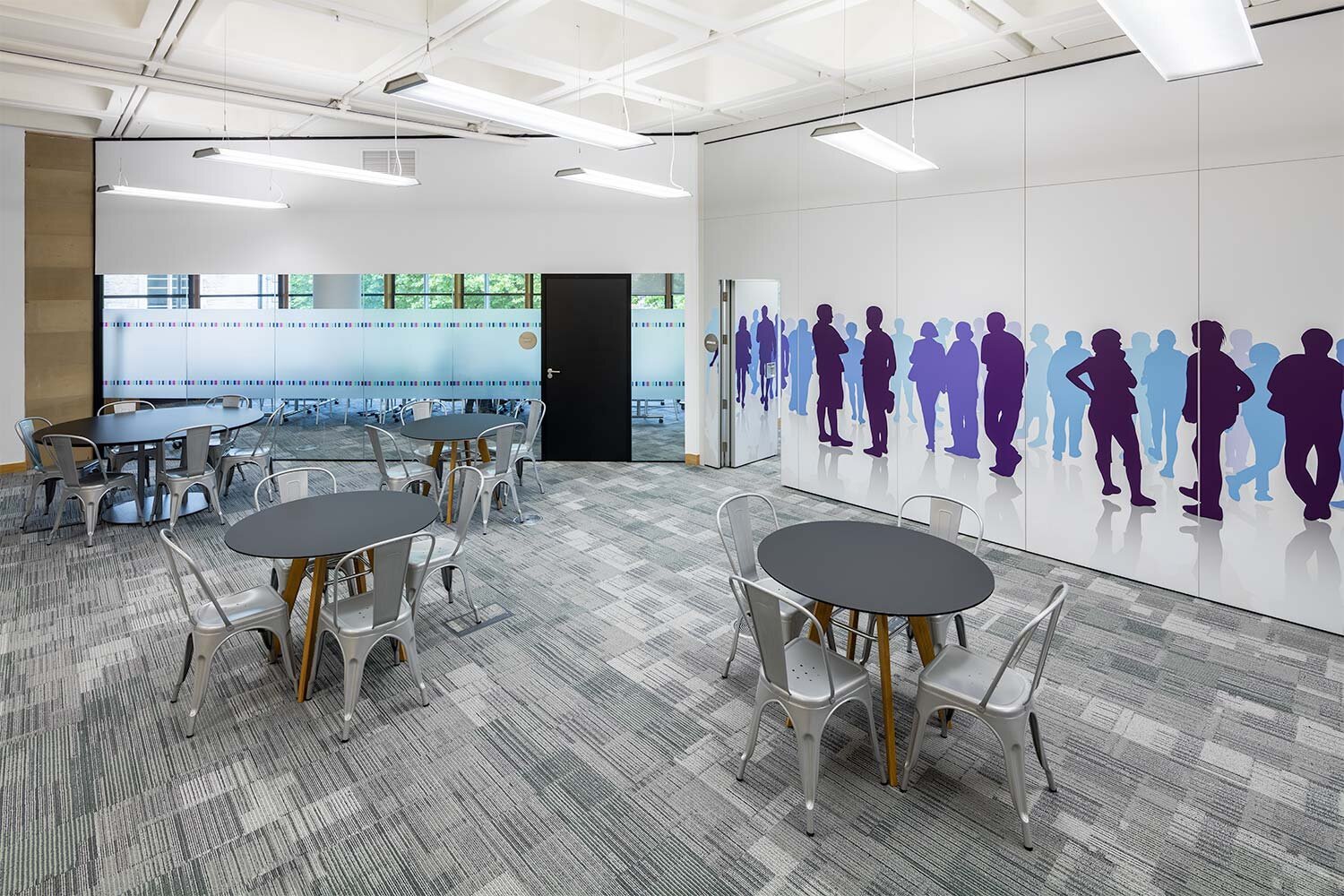
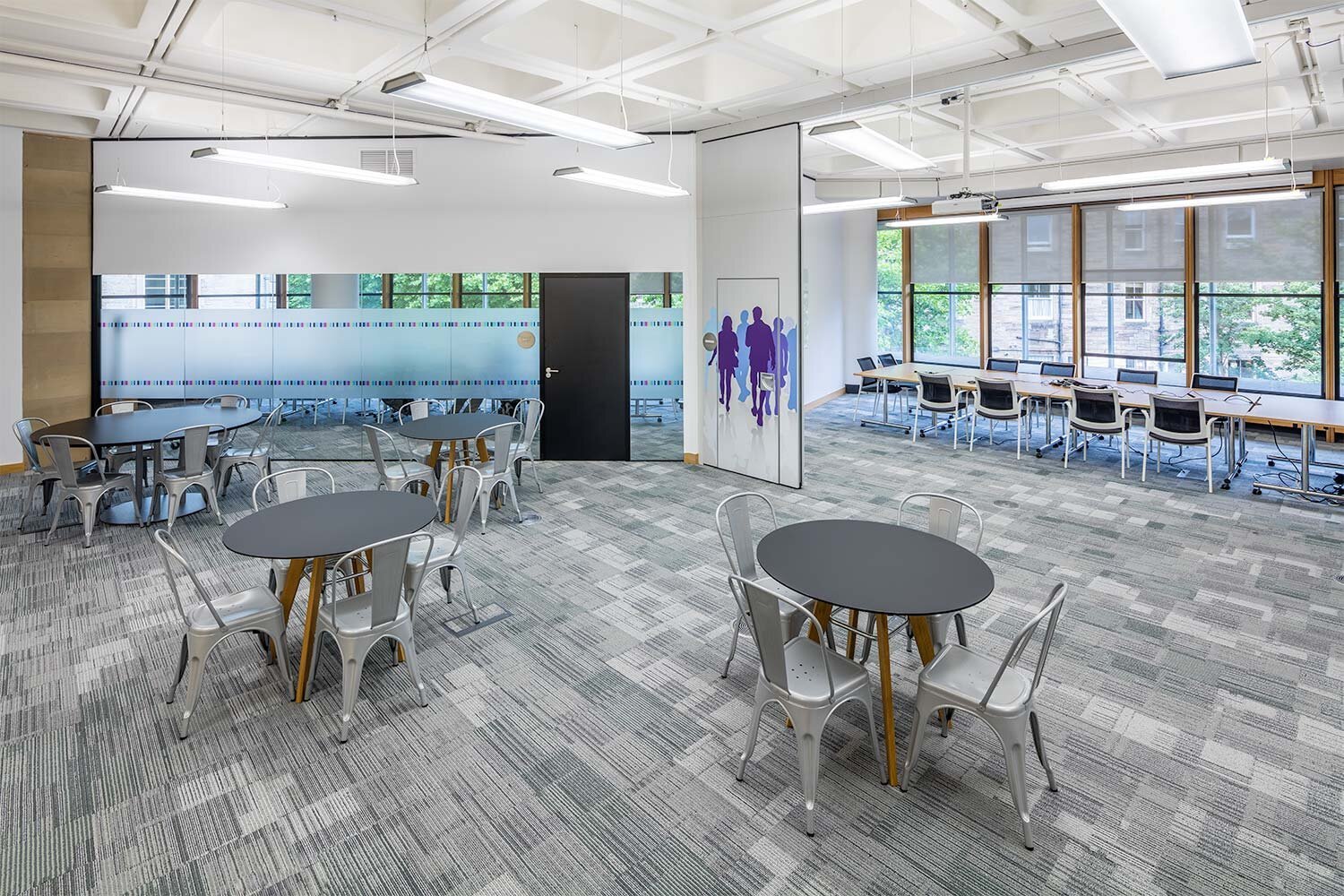
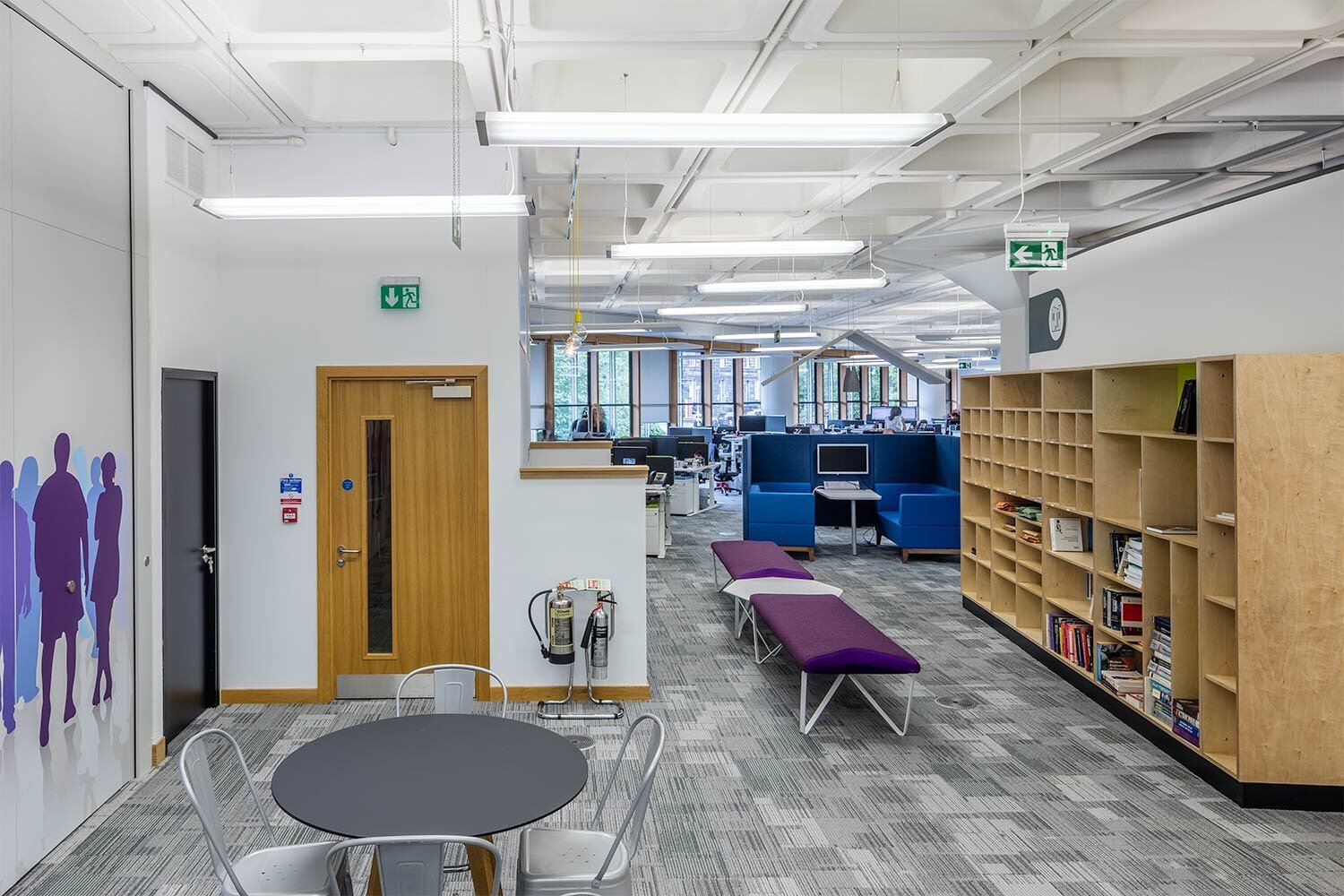
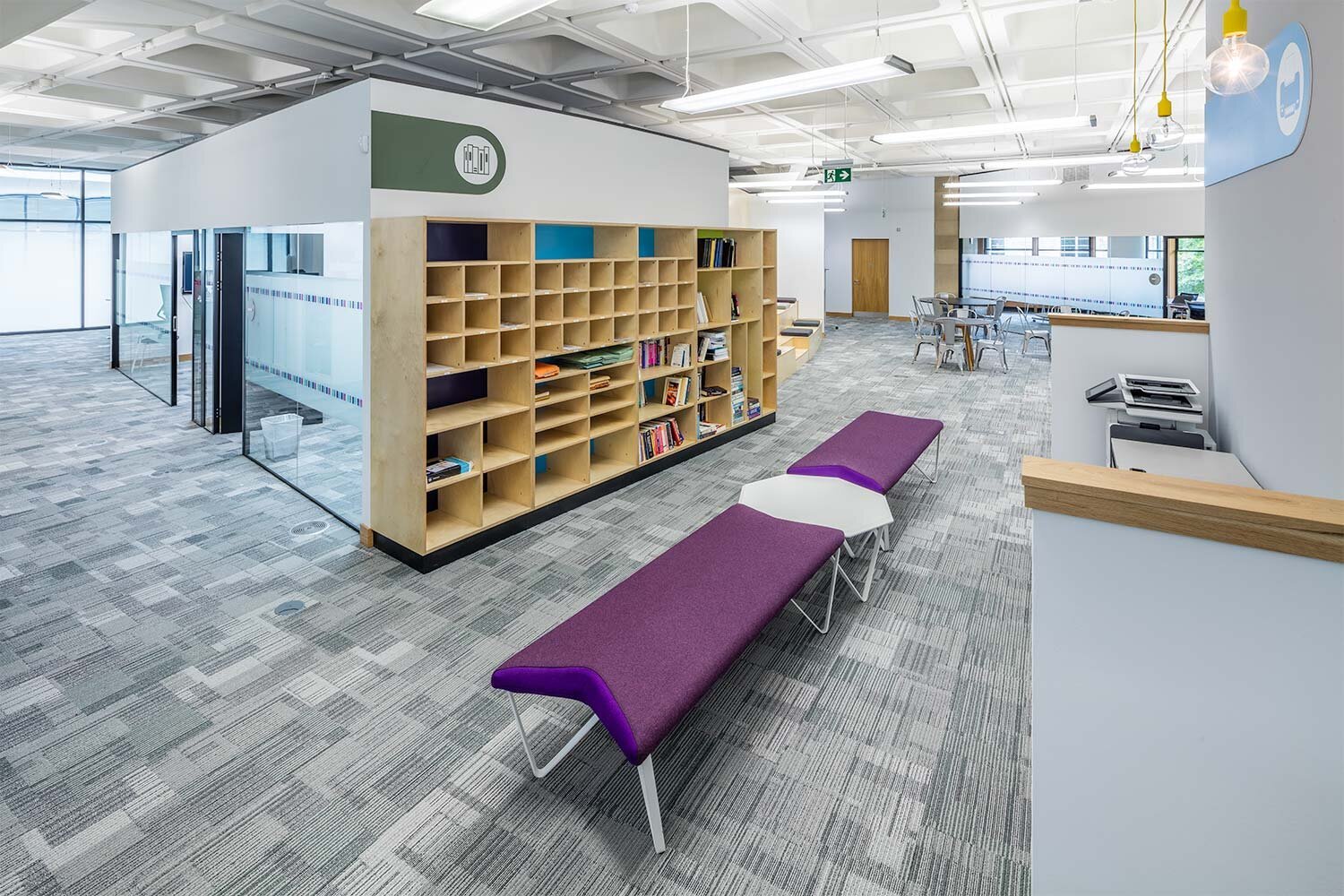
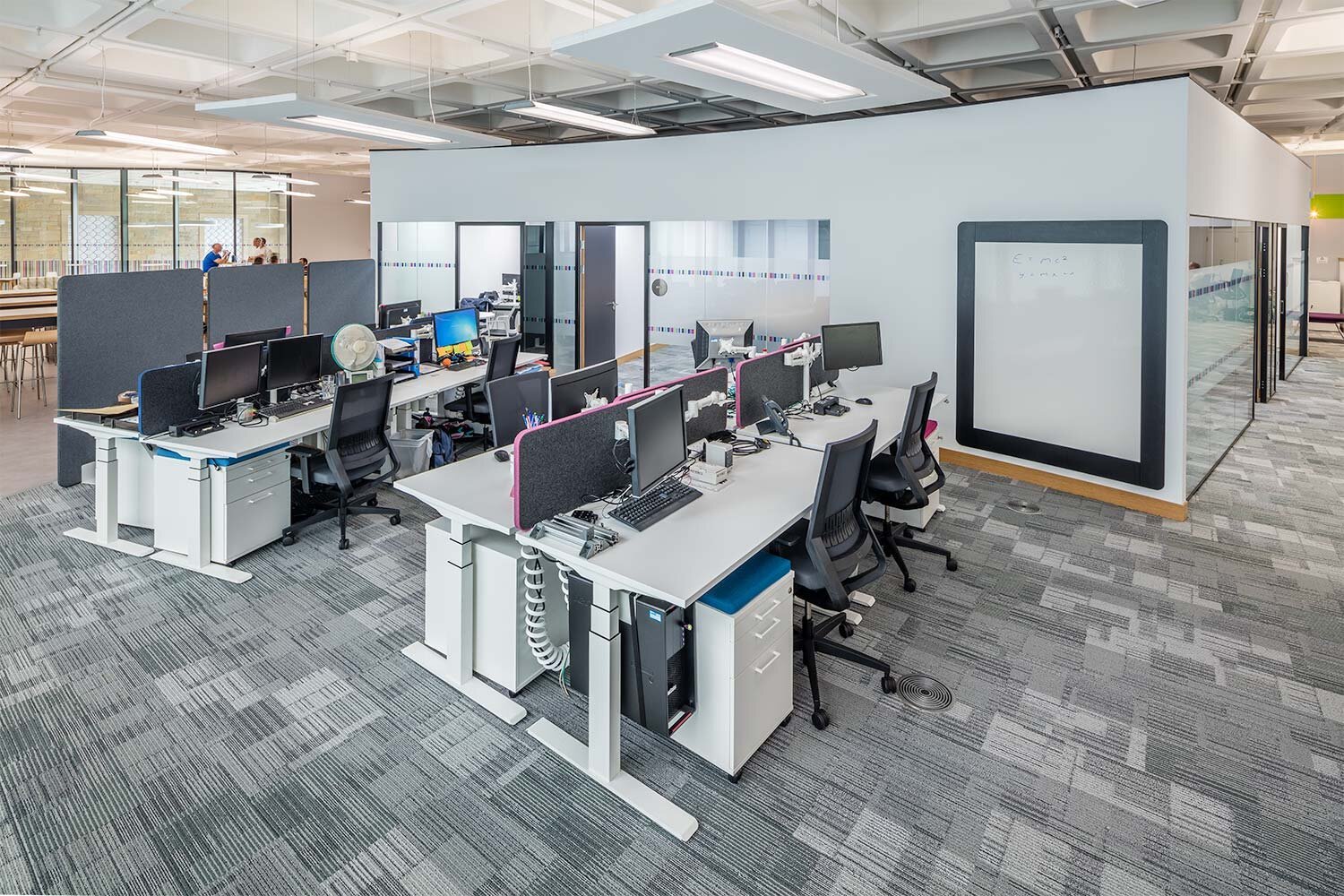
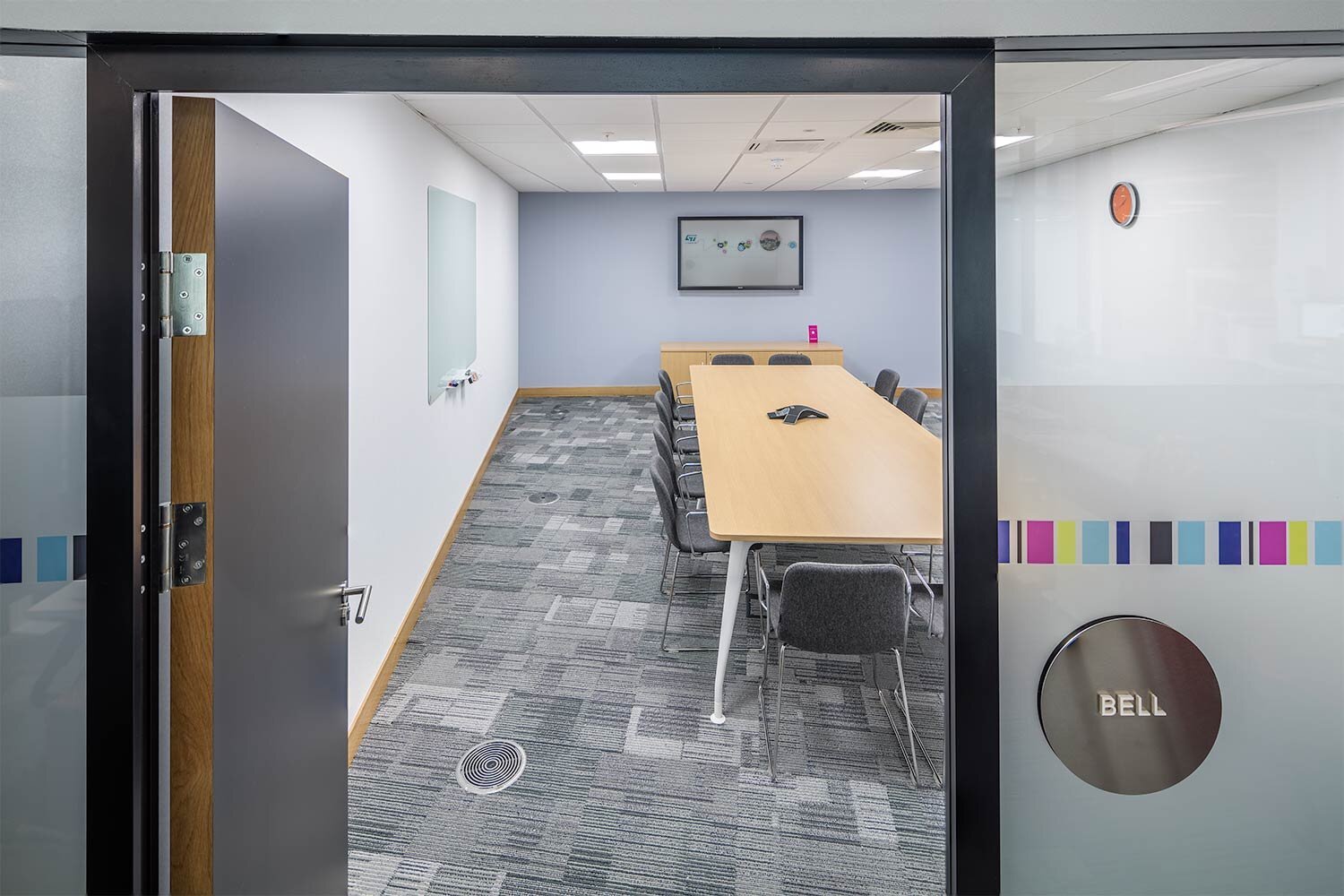
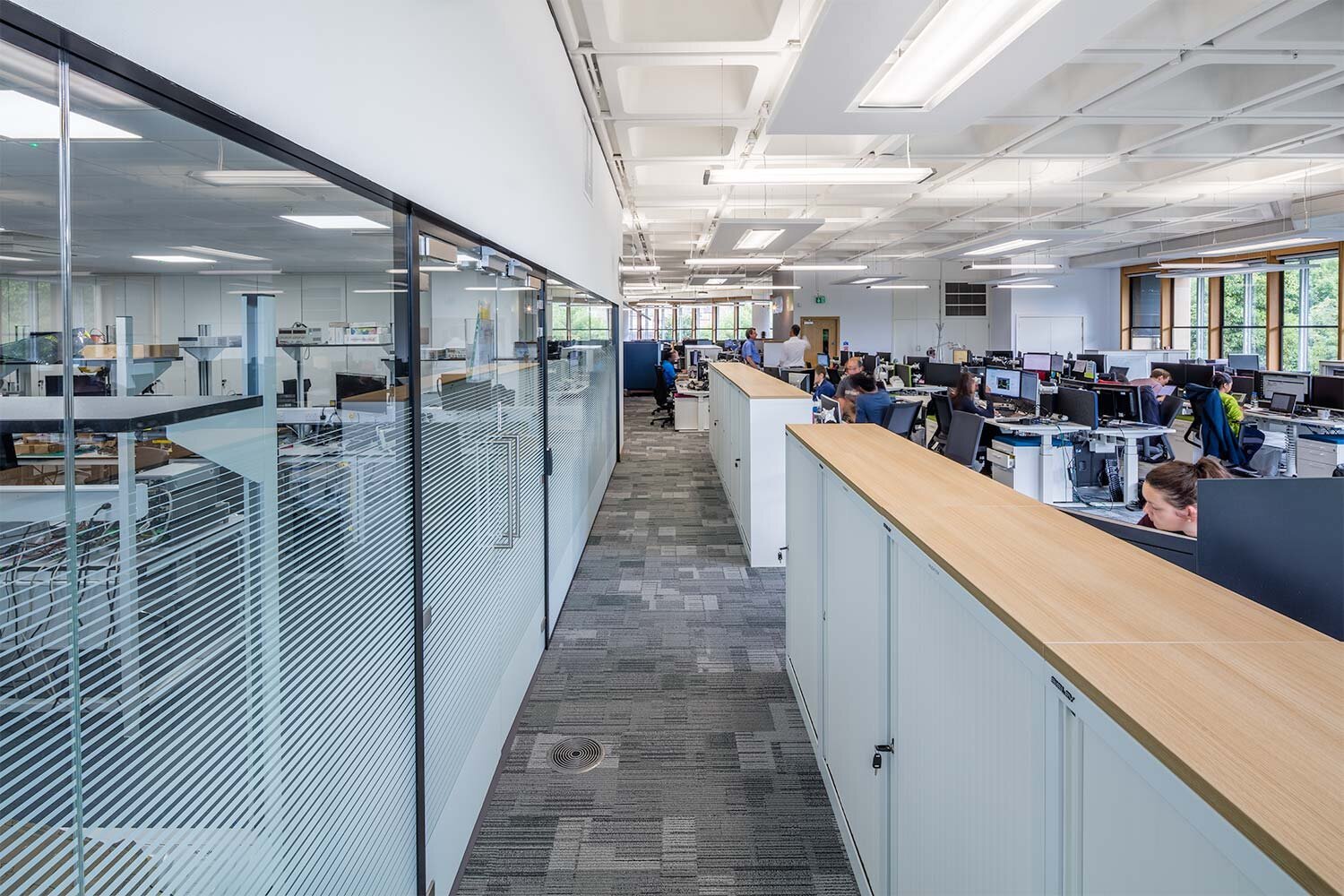
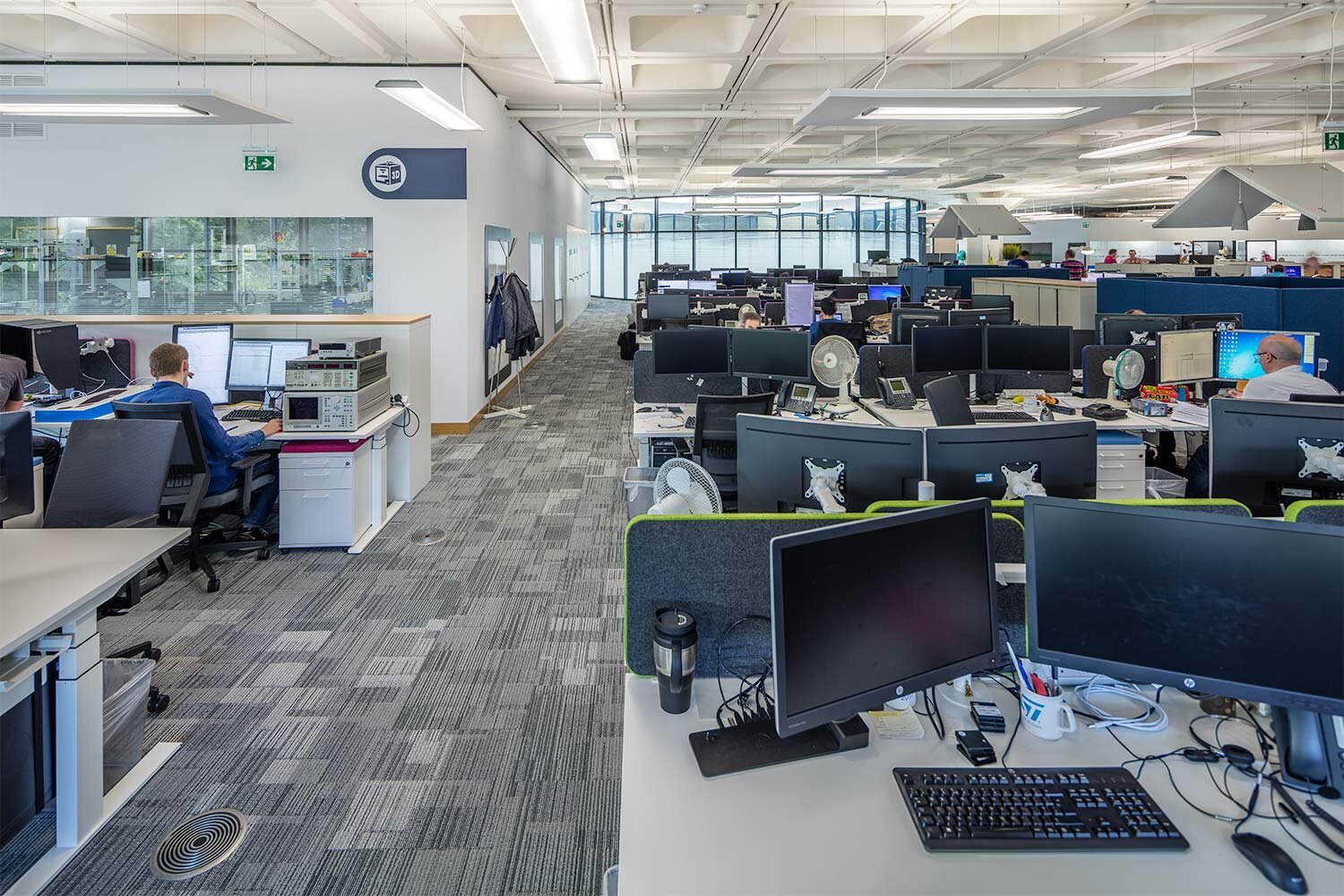
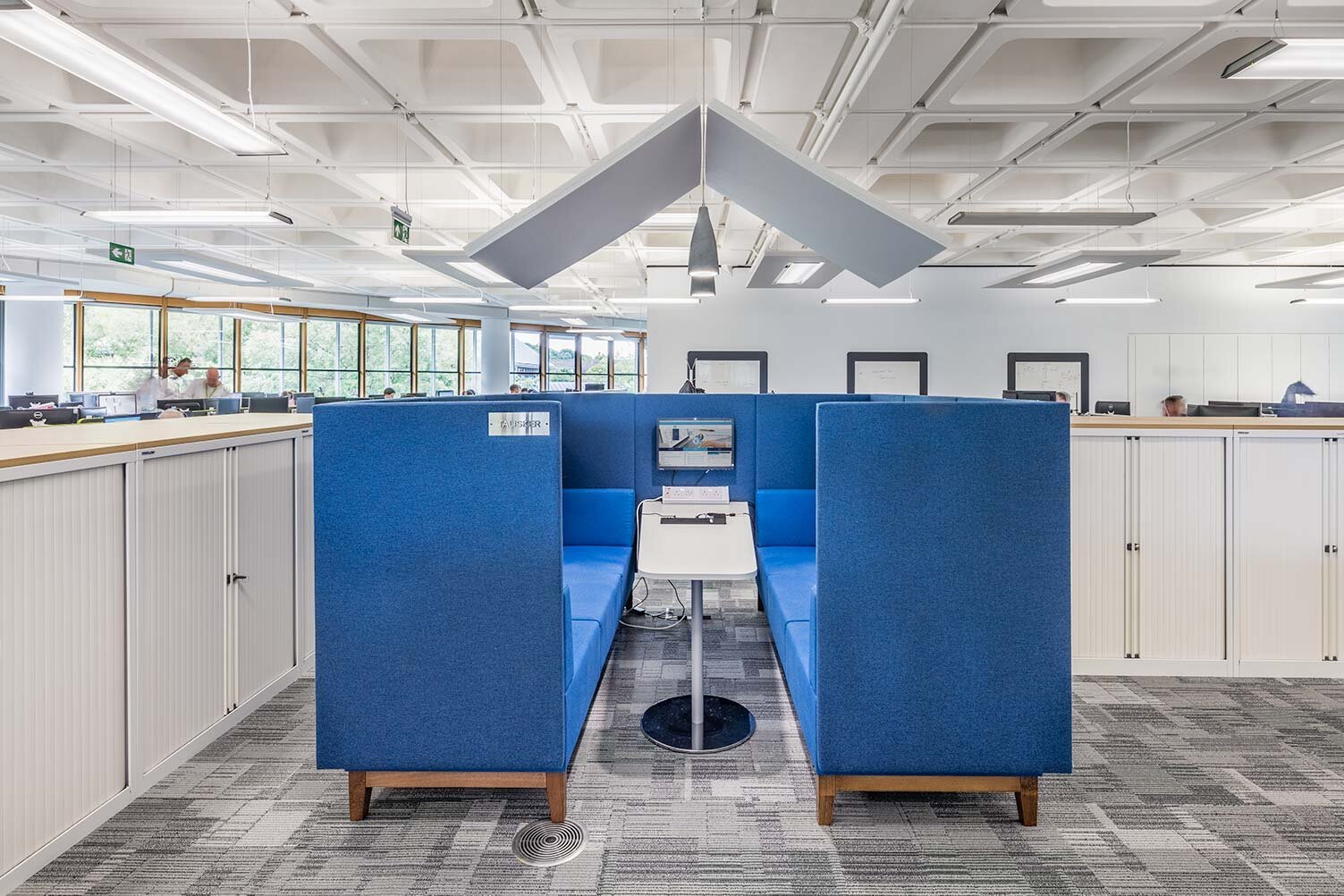
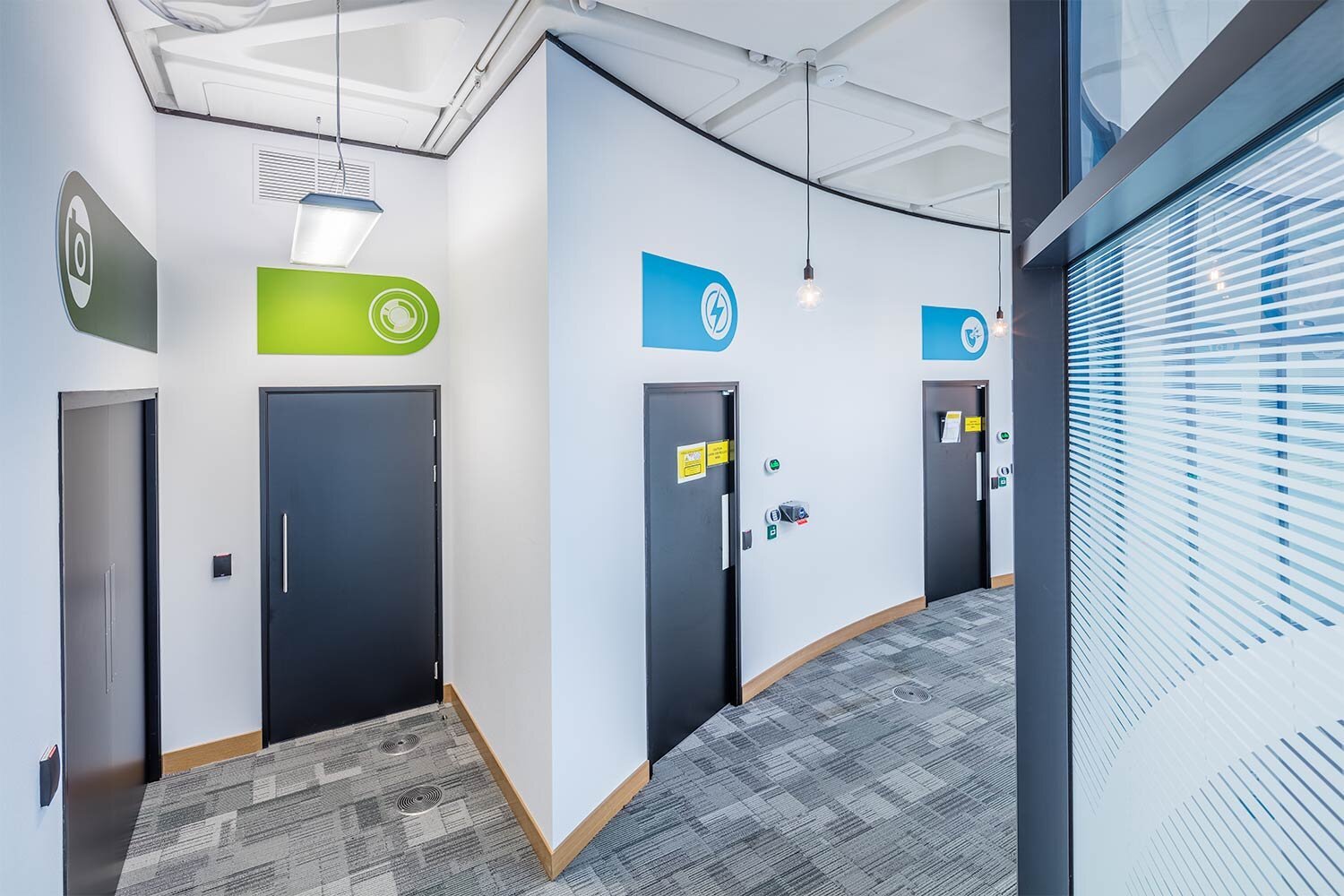
Industrial fit-out for Plexus, Bathgate
Plexus plays a key role in the realisation of their client concepts into branded products and deliver them to the market. They are a global electronics manufacturing company that solves the most complex product challenges in health care and life sciences, industrial, aerospace and defense.
In 2018 when Plexus were looking to expand their Livingston Design Centre. They once again turned to Amos Beech as their trusted partner for the design and construction works of this industrial fit out. With the European management team having making a commitment to the Board of Directors to deliver by March 19 this was no small achievement.
Industrial Fit Out in Bathgate Scotland
Tasked with building the cost schedule from the ground up whilst working with the ever-changing dynamic of a Hi-Tech electronic manufacturing facility we had our work cut out. With construction starting in October 2018, we managed to work around the existing production facility whilst creating new laboratory space for the engineers, new offices and alterations to the main services including HVAC, sprinkler, humidity, nitrogen, electrical and air to enable their manufacturing plant to be relocated in a seamless manner.
Before images
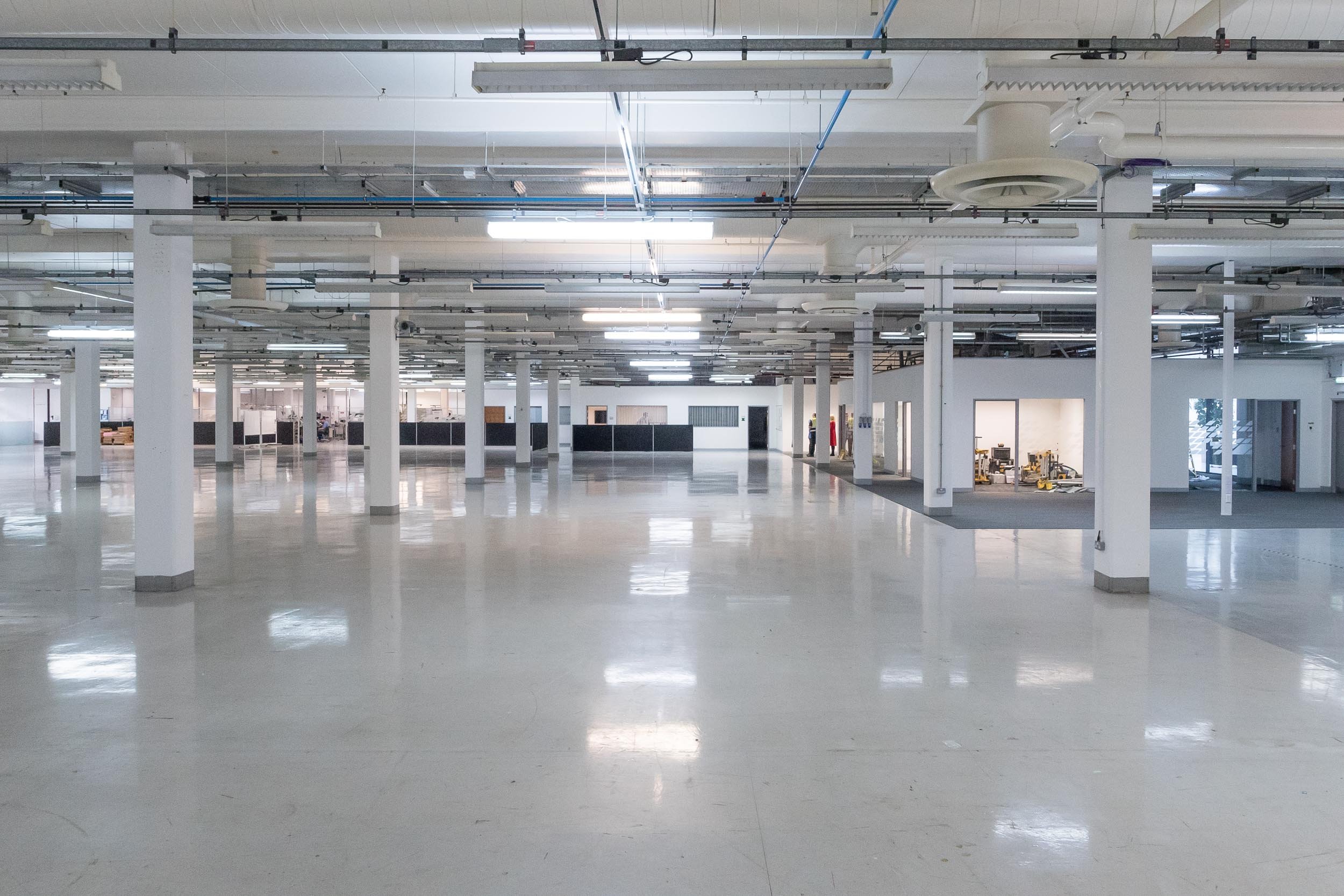
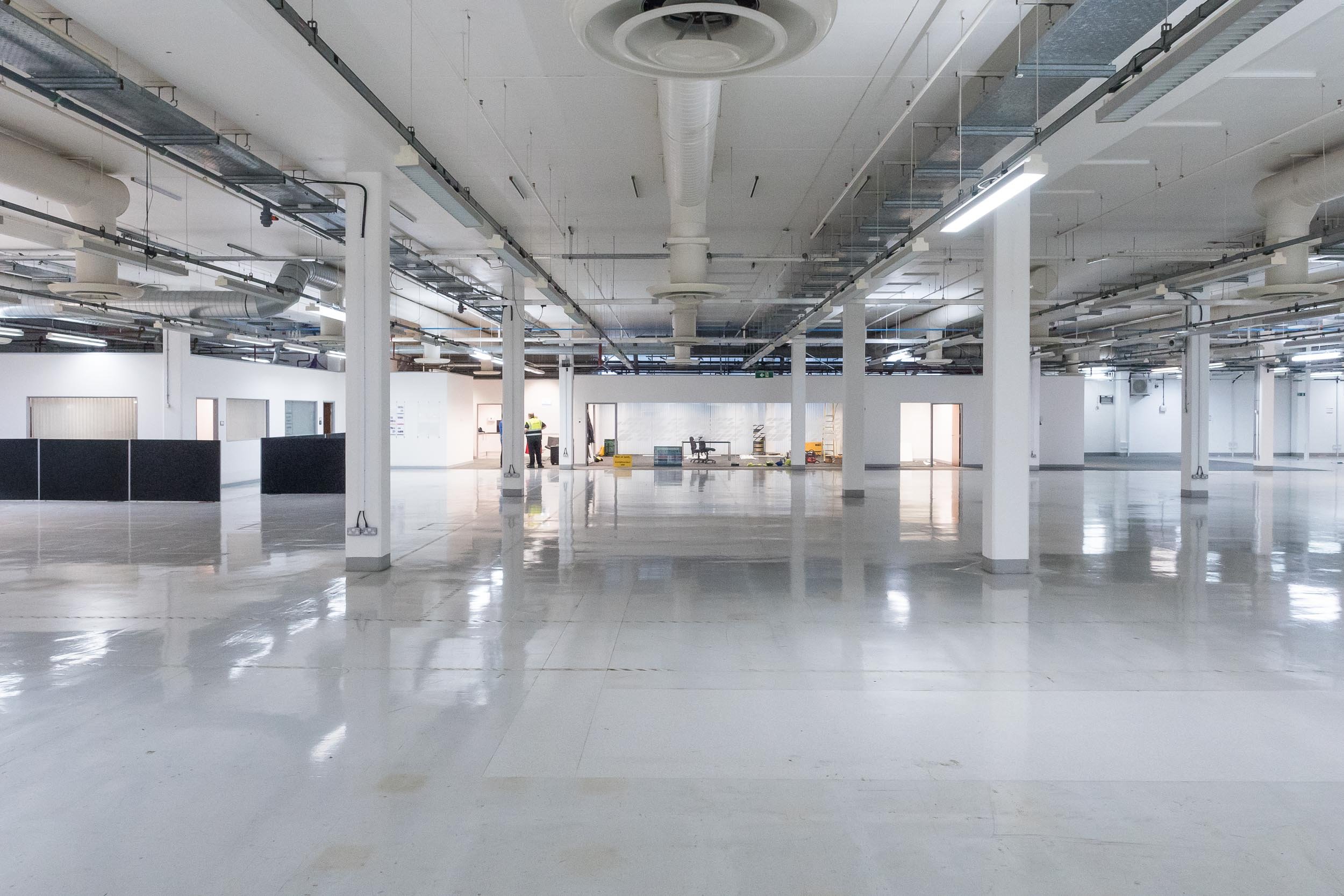
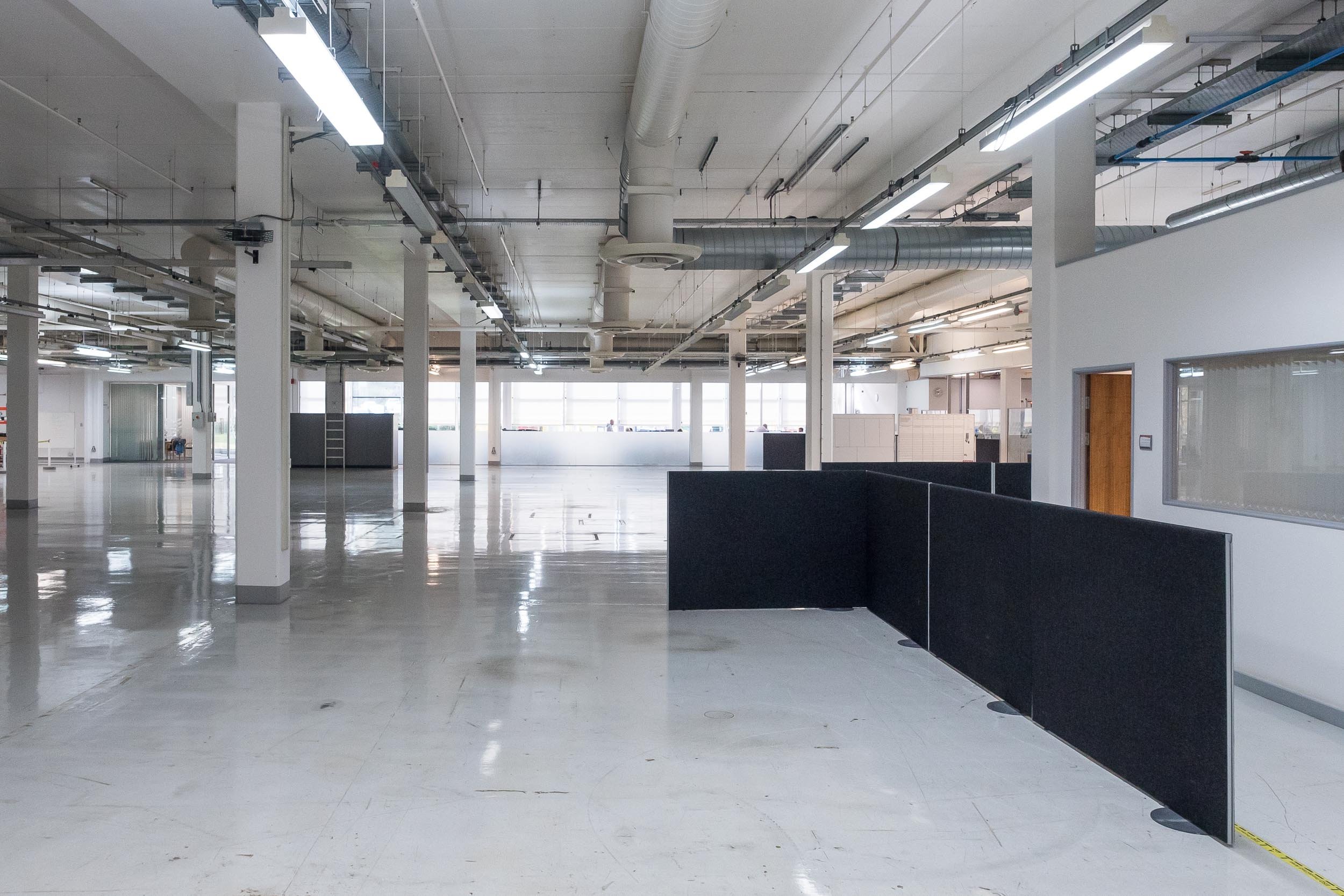
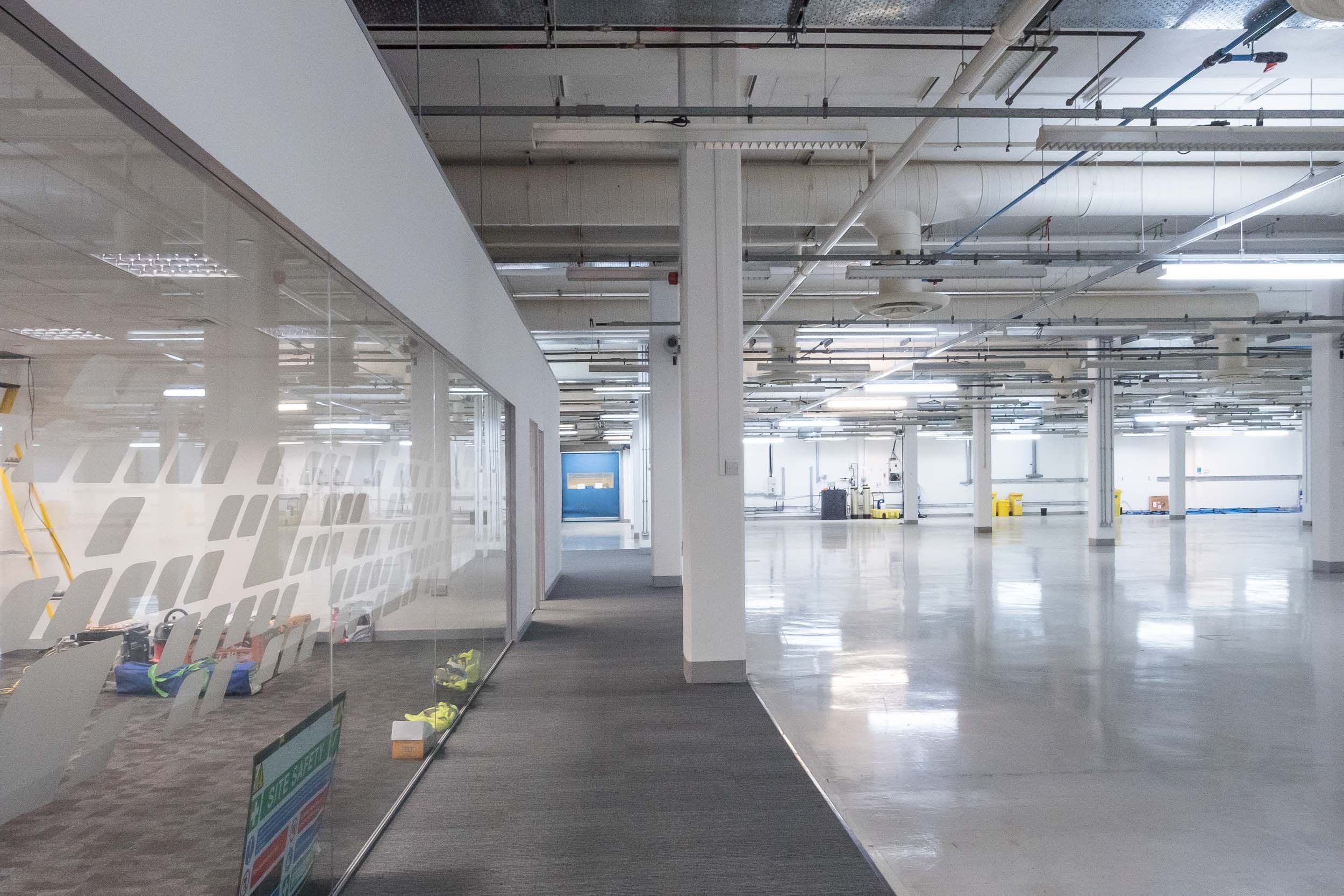
Along with the construction project there was an additional brief to lift the look and feel of the design centre to be more in line with Plexus’s other design centres throughout the world.
Plexus has a long track record of innovation and technology through its own in house resource so we rebranded all their internal meeting rooms and helped create a journey experience for their visiting customers.
The final result of this industrial fit out:
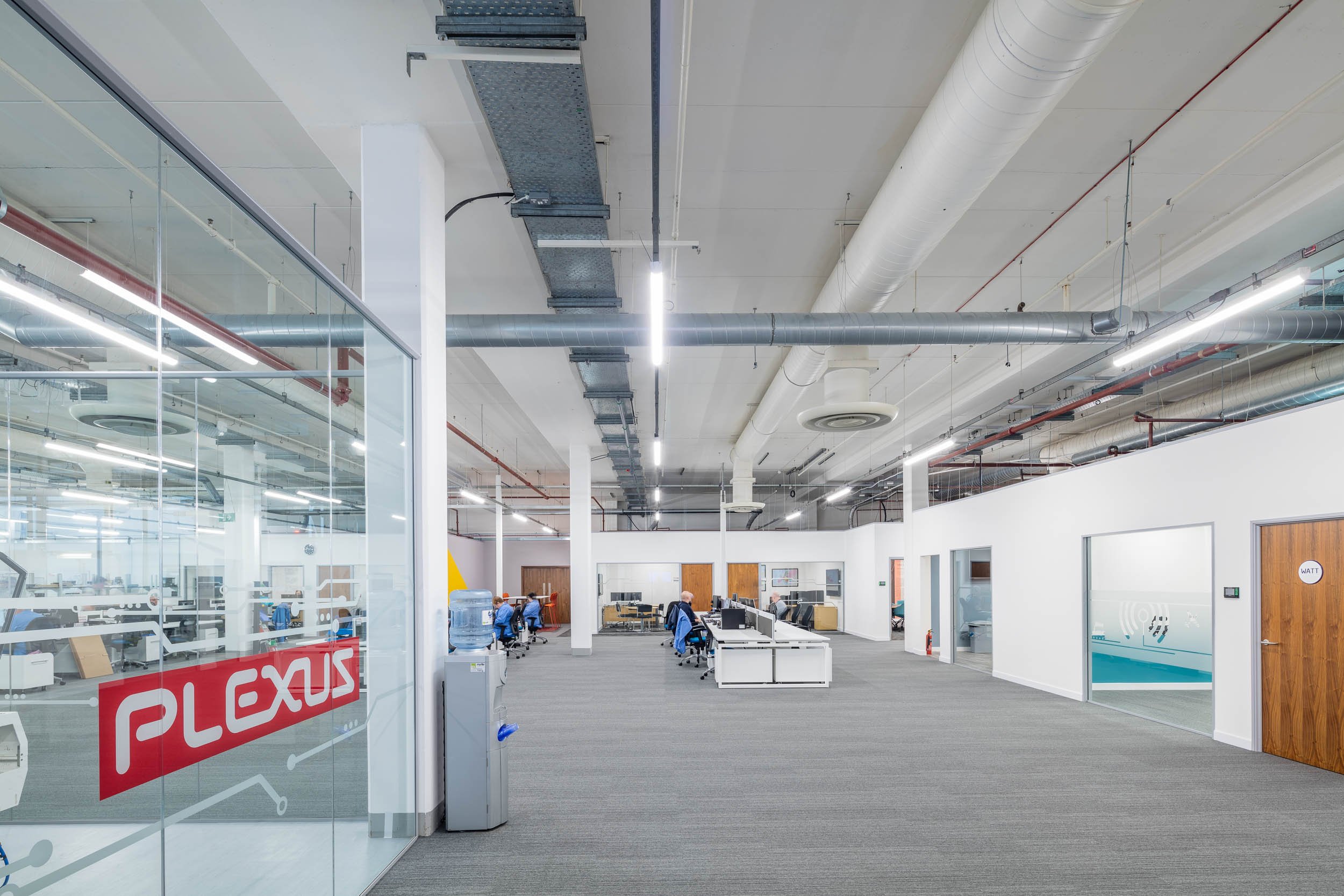
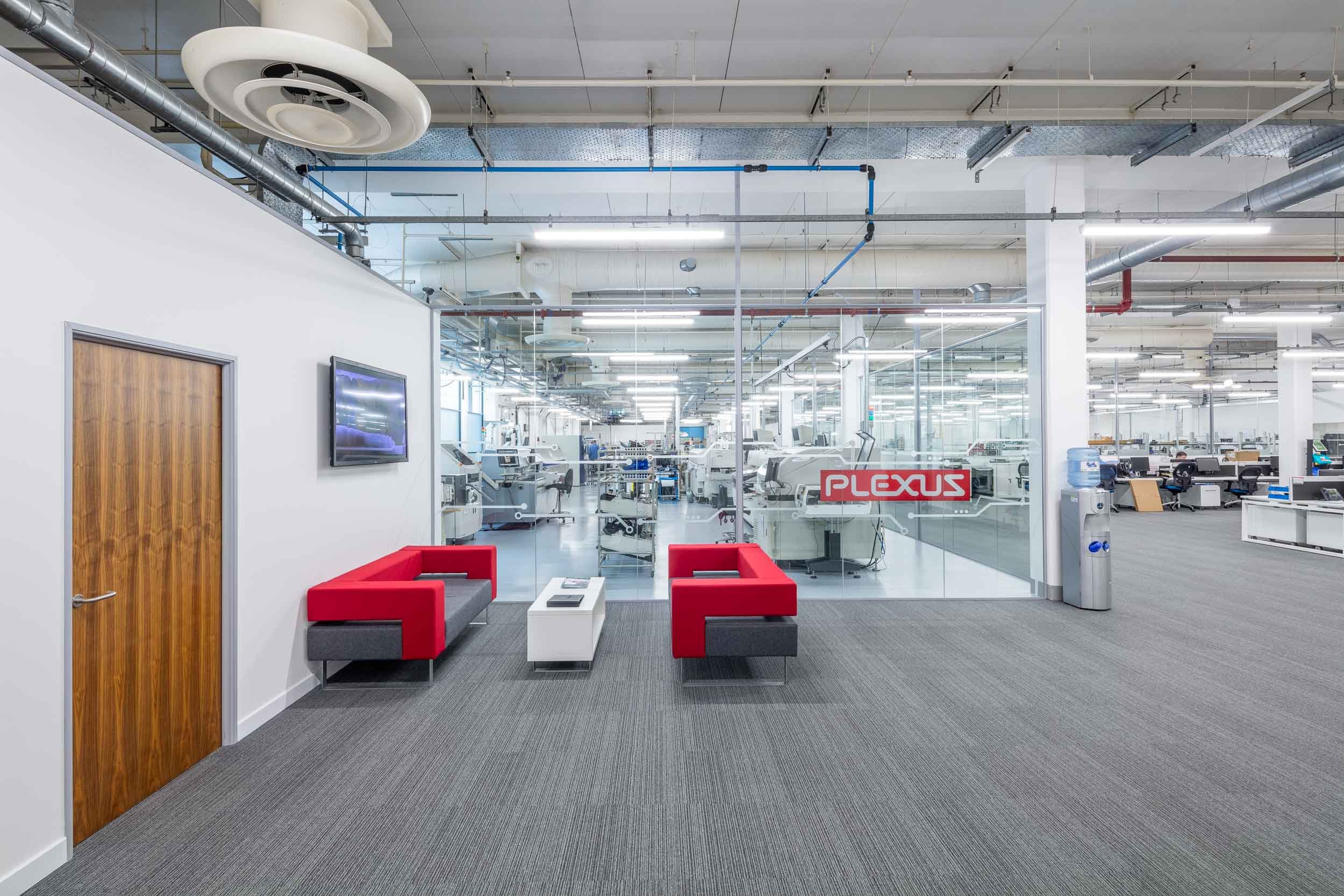
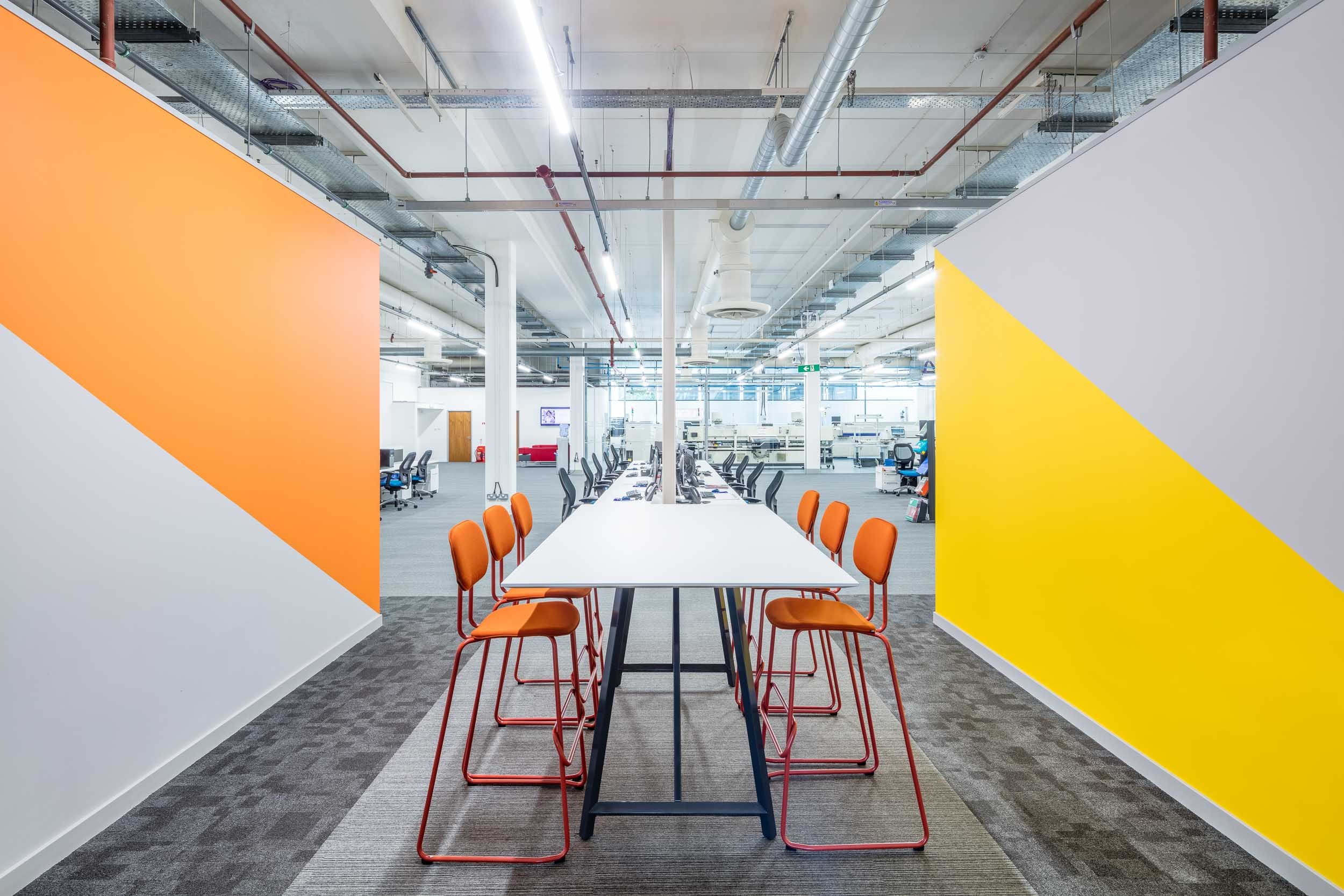
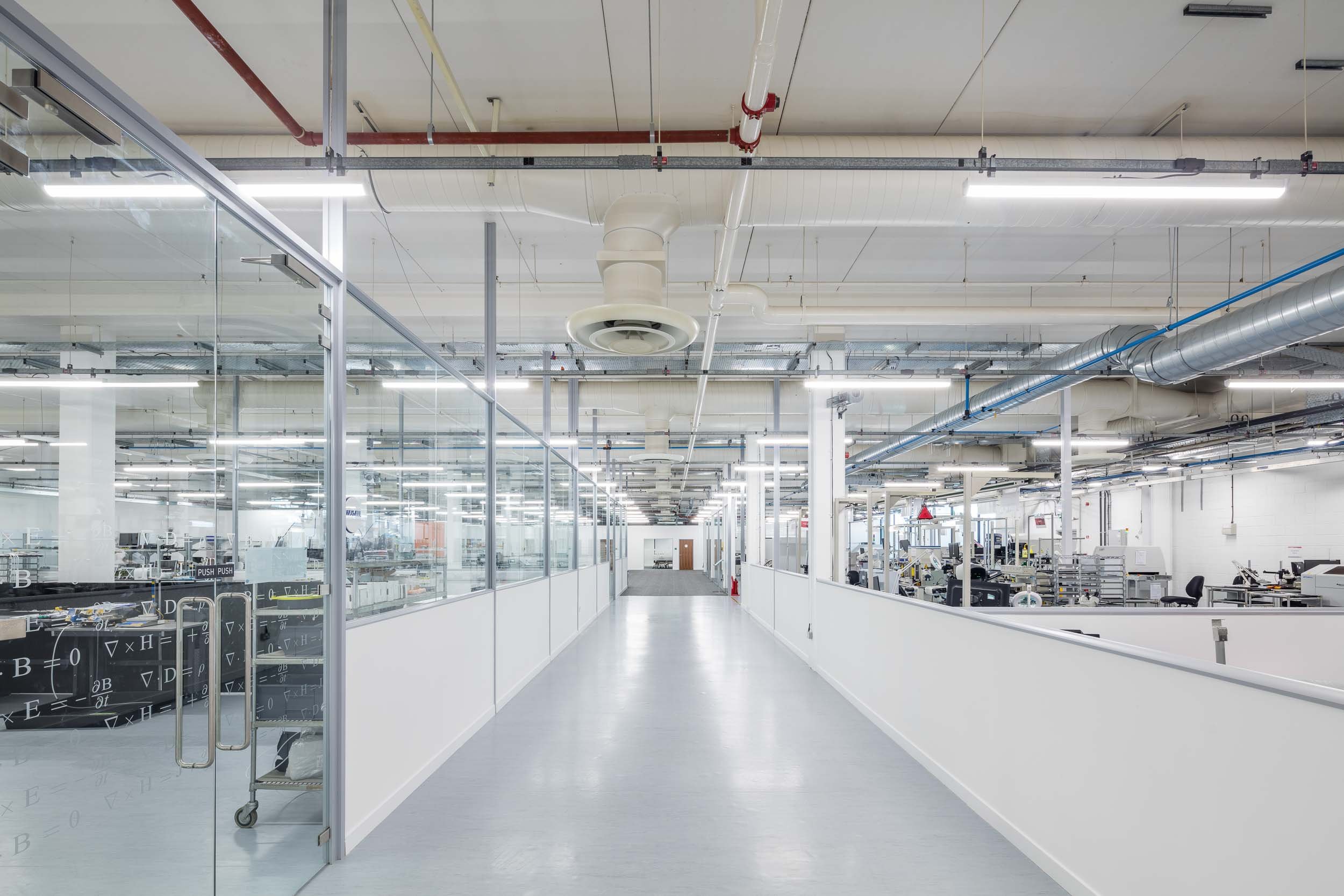
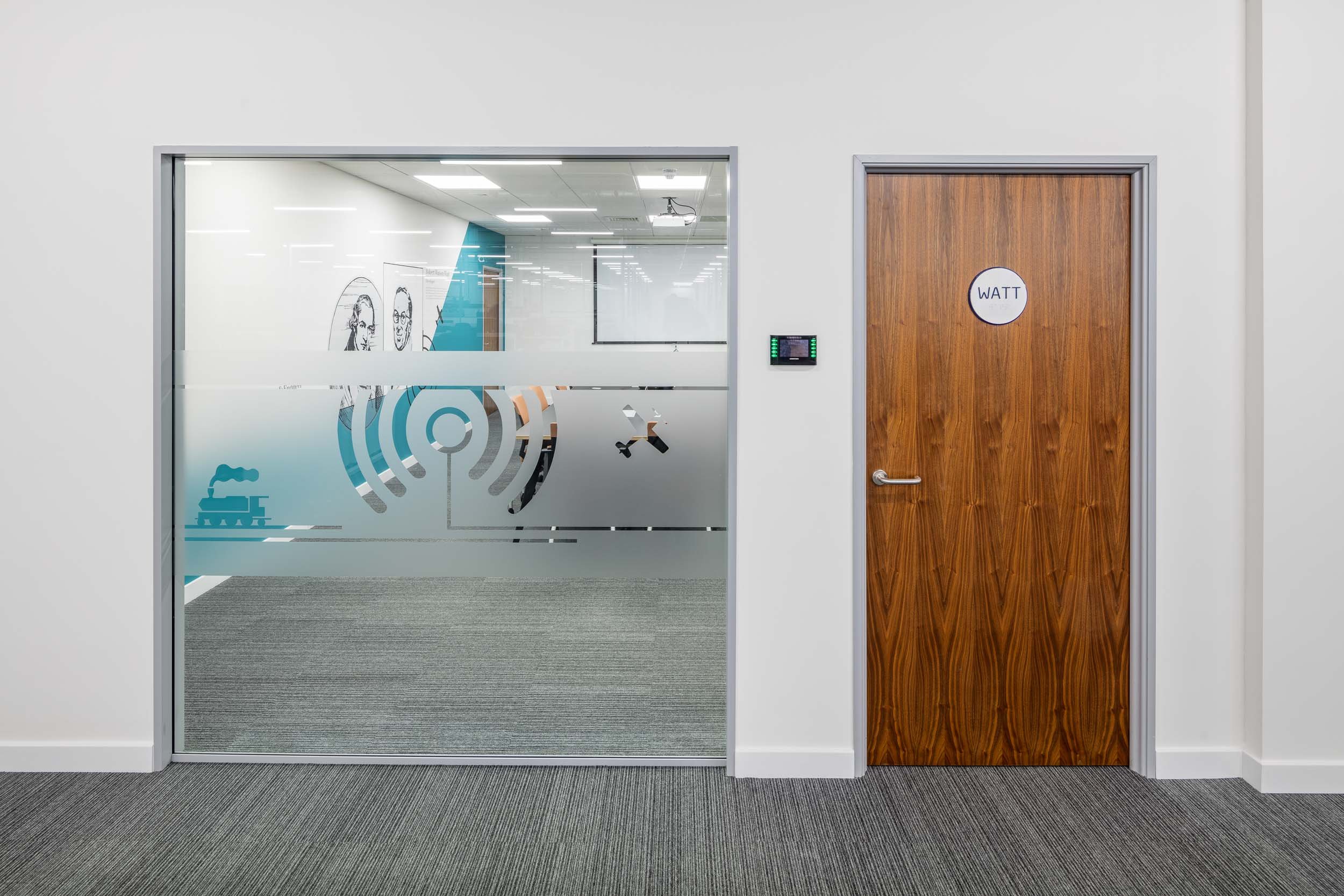
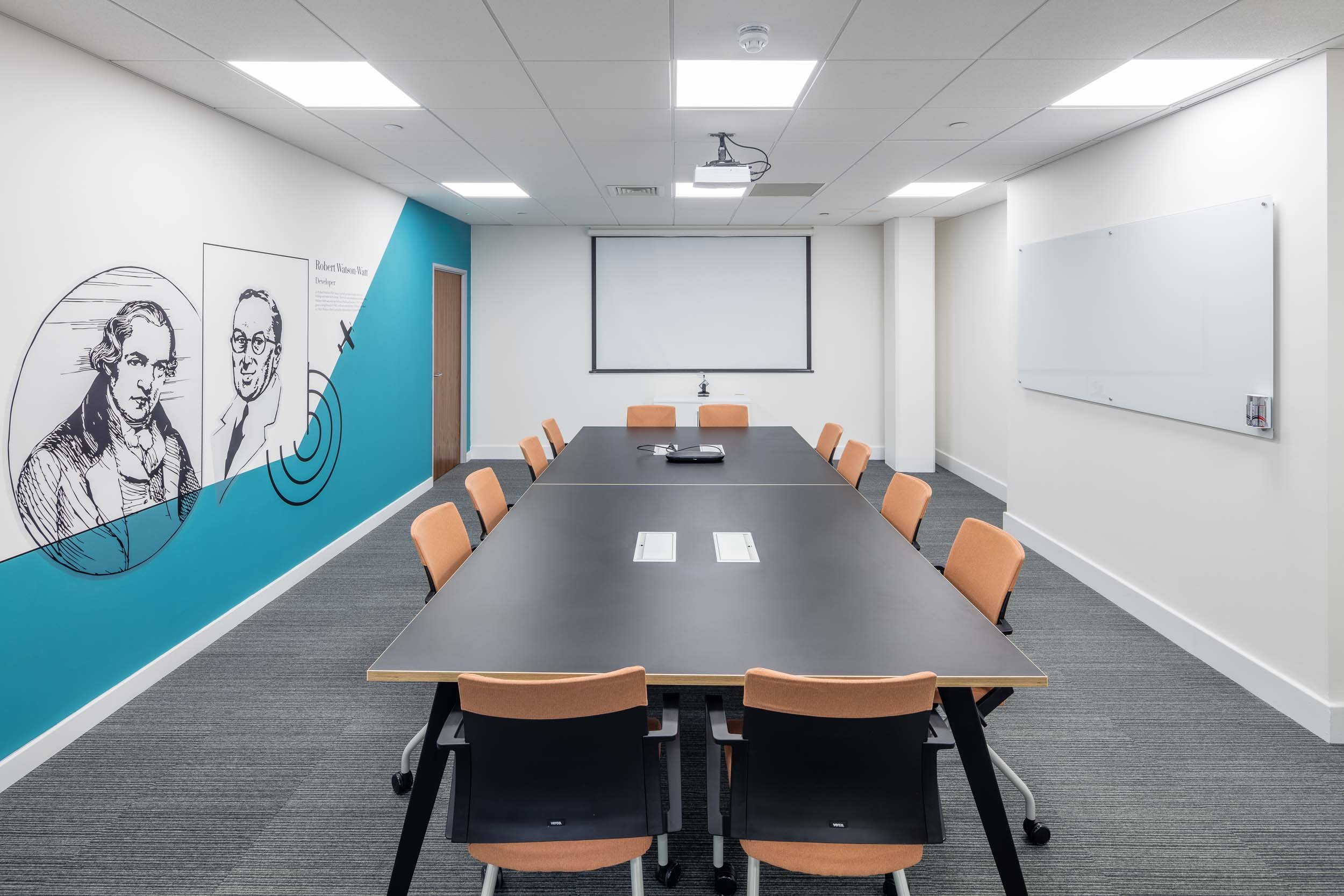
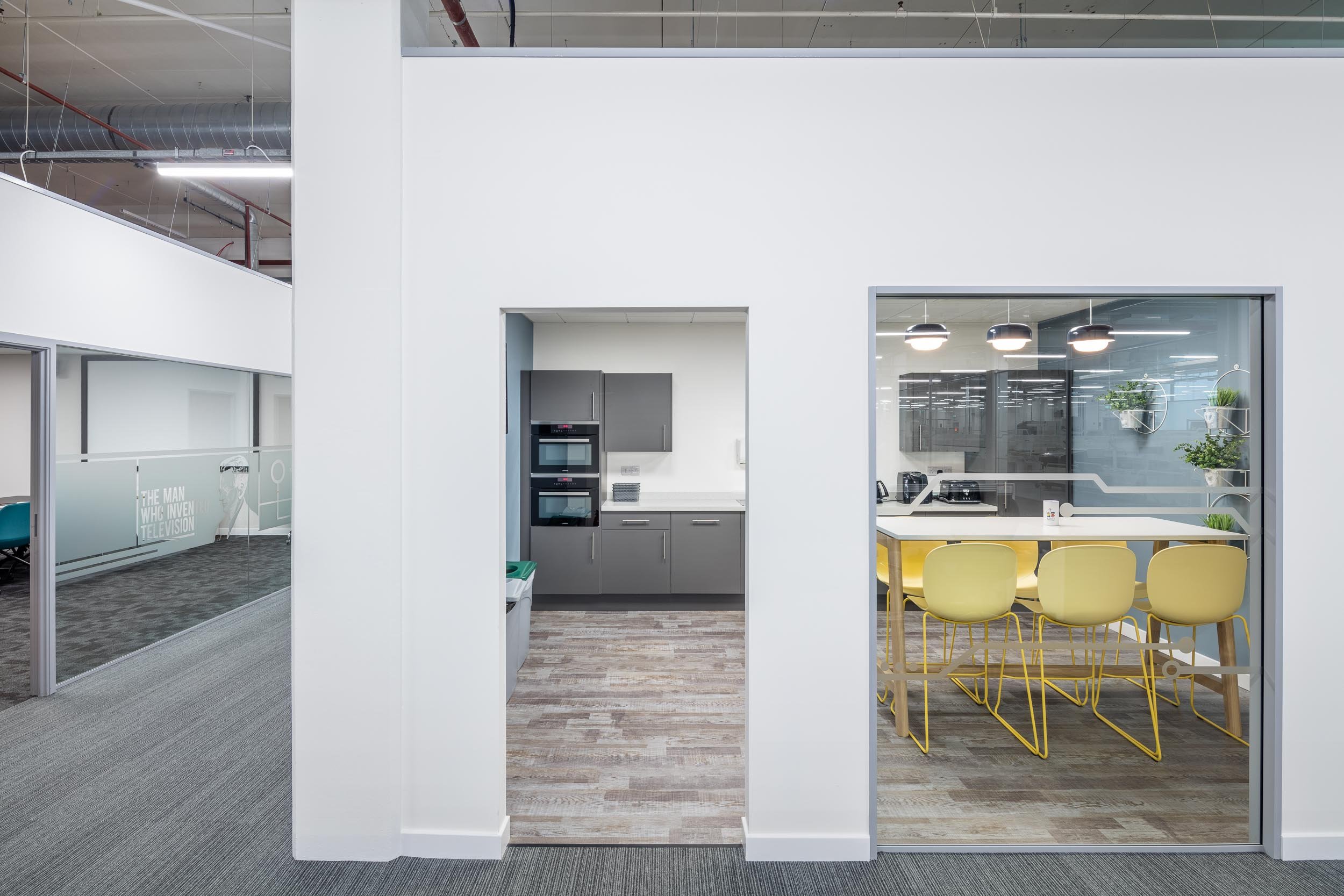
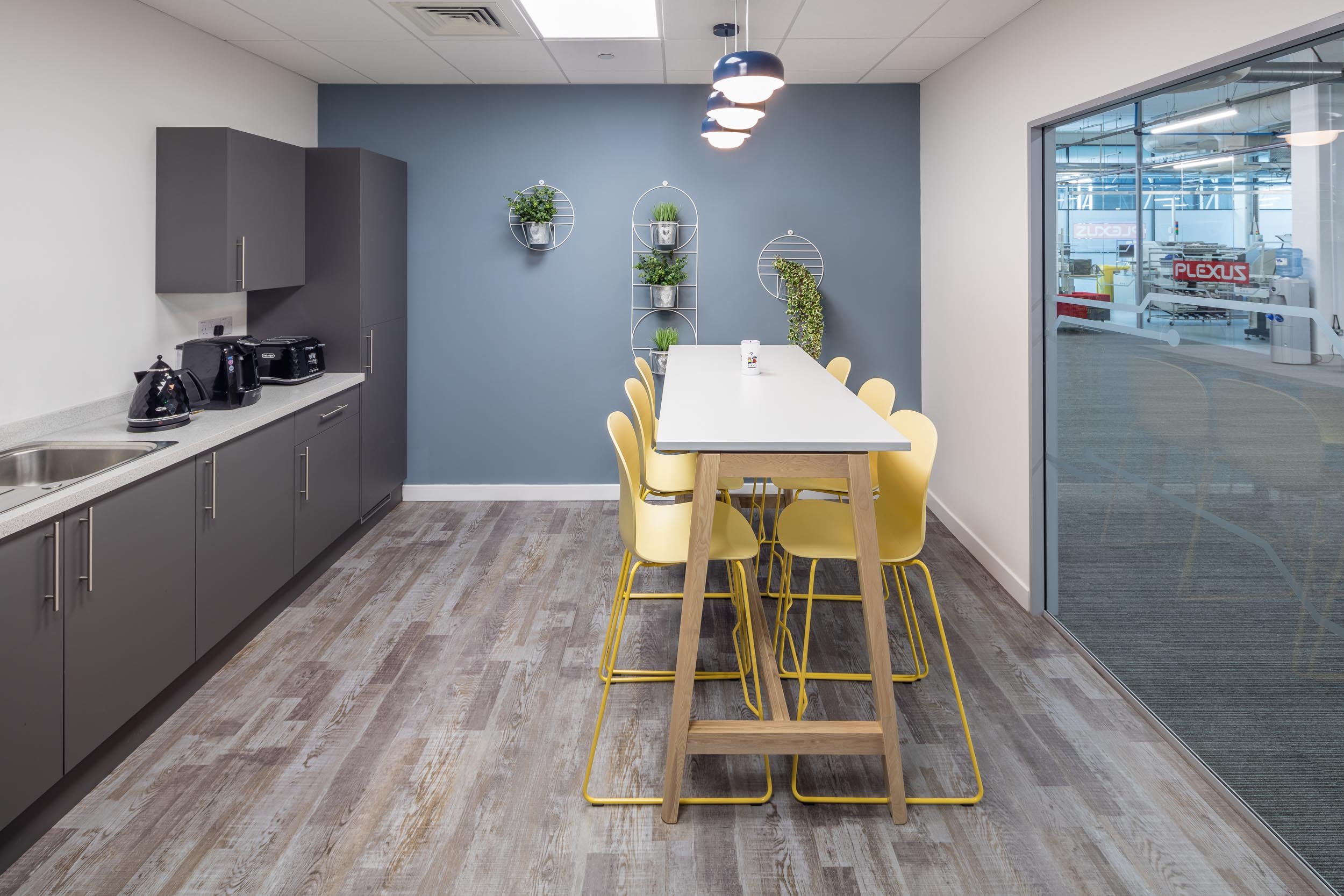
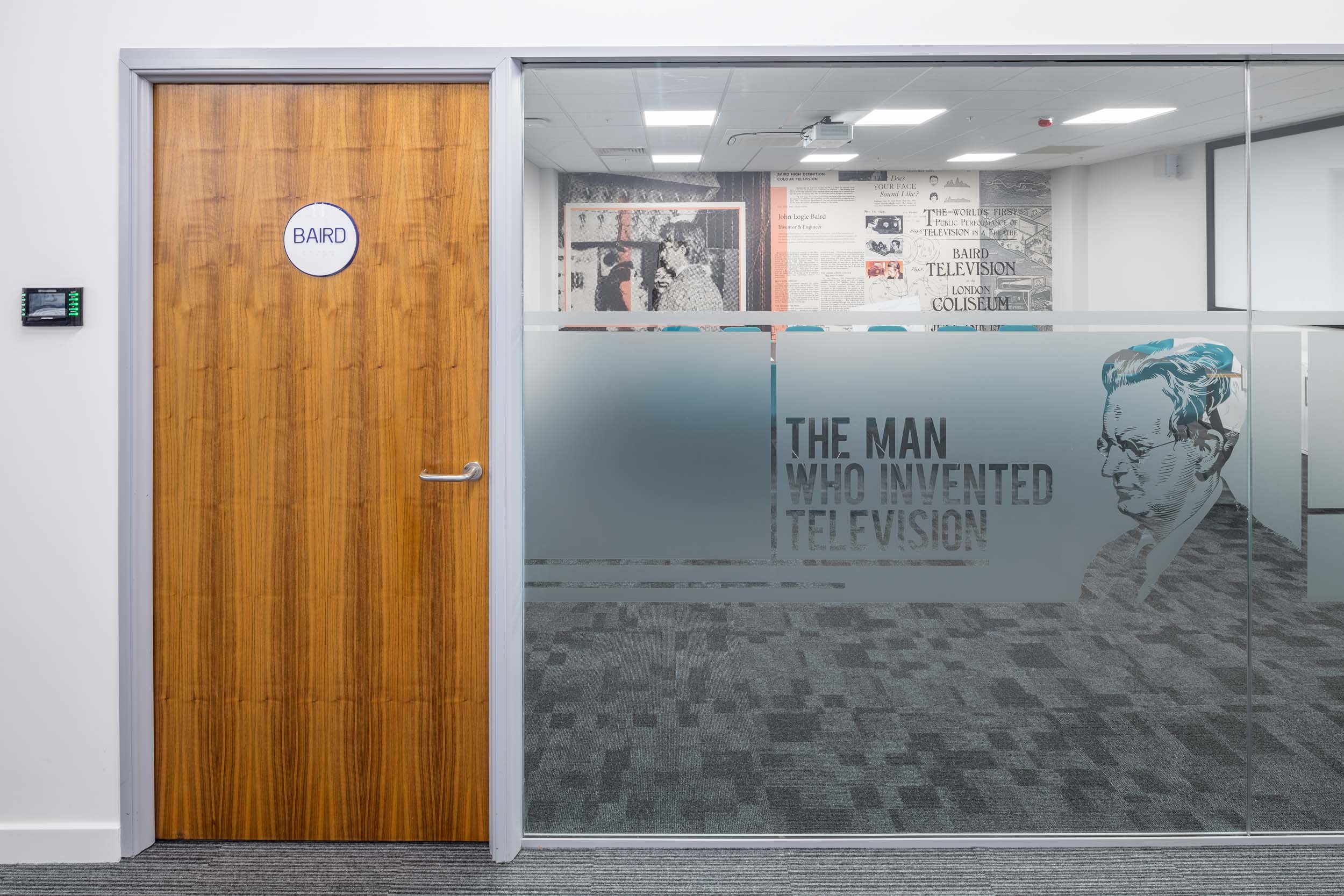
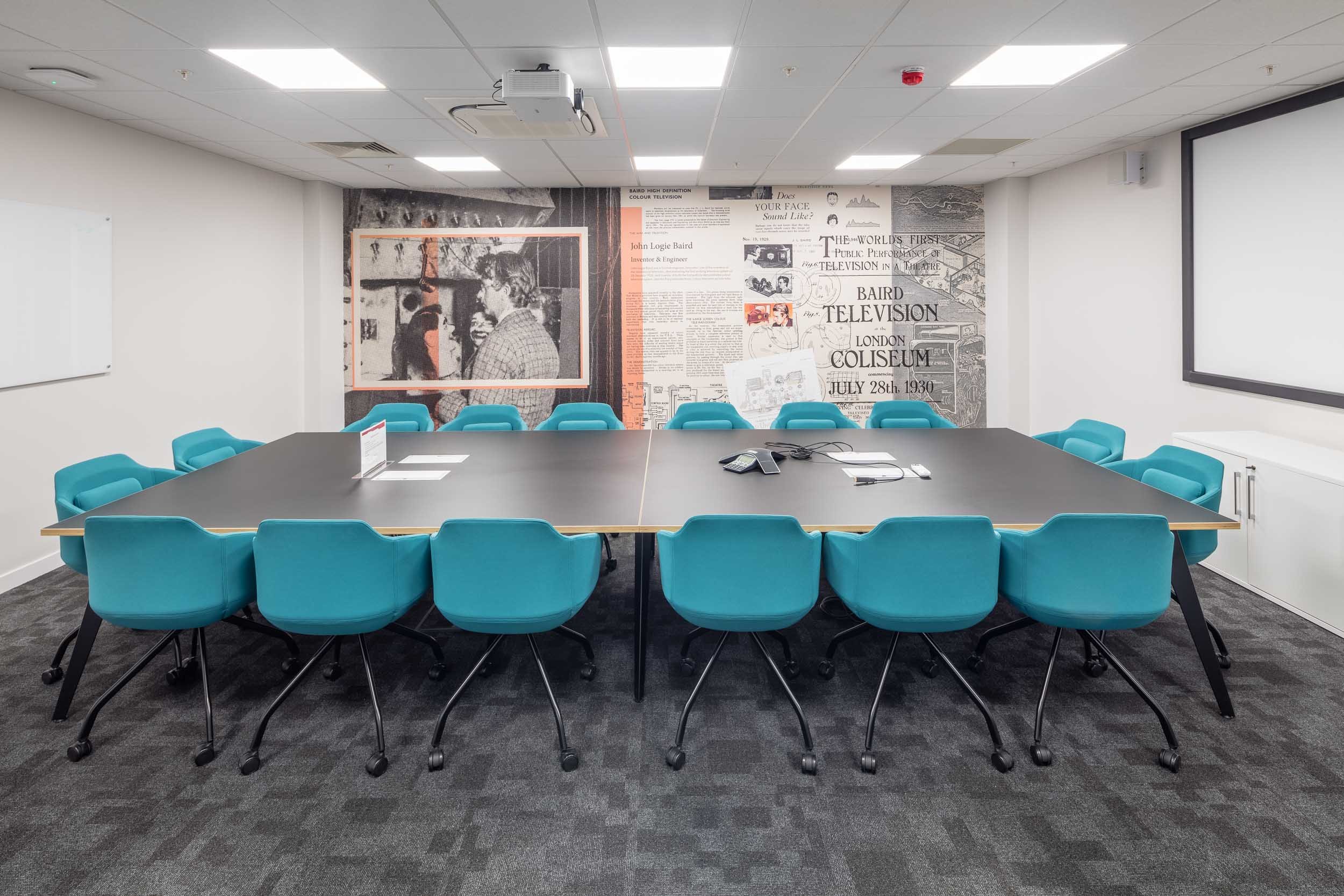
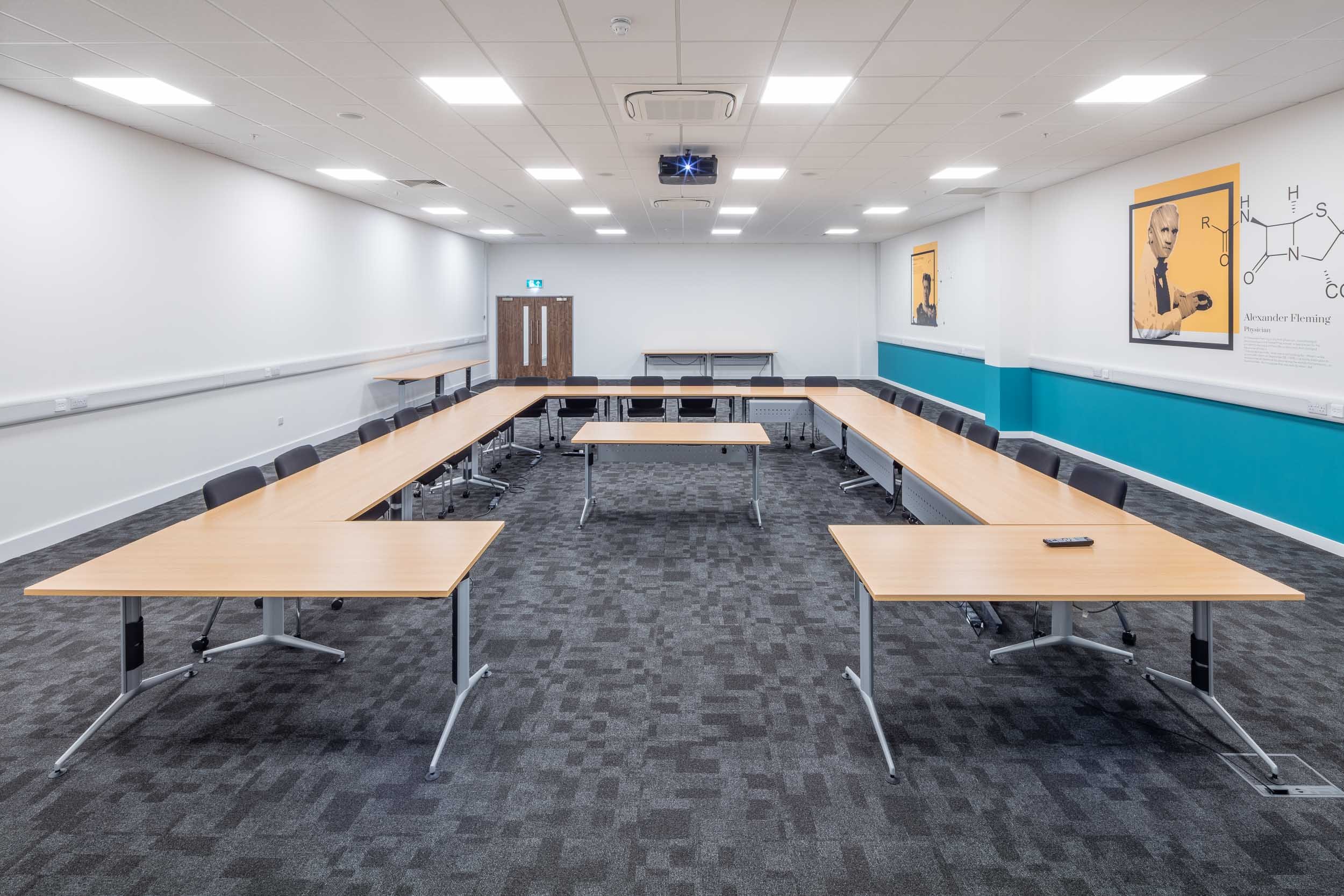
In addition to that we have upgraded the graphics and manifestation on the first floor and added a new kitchen area:

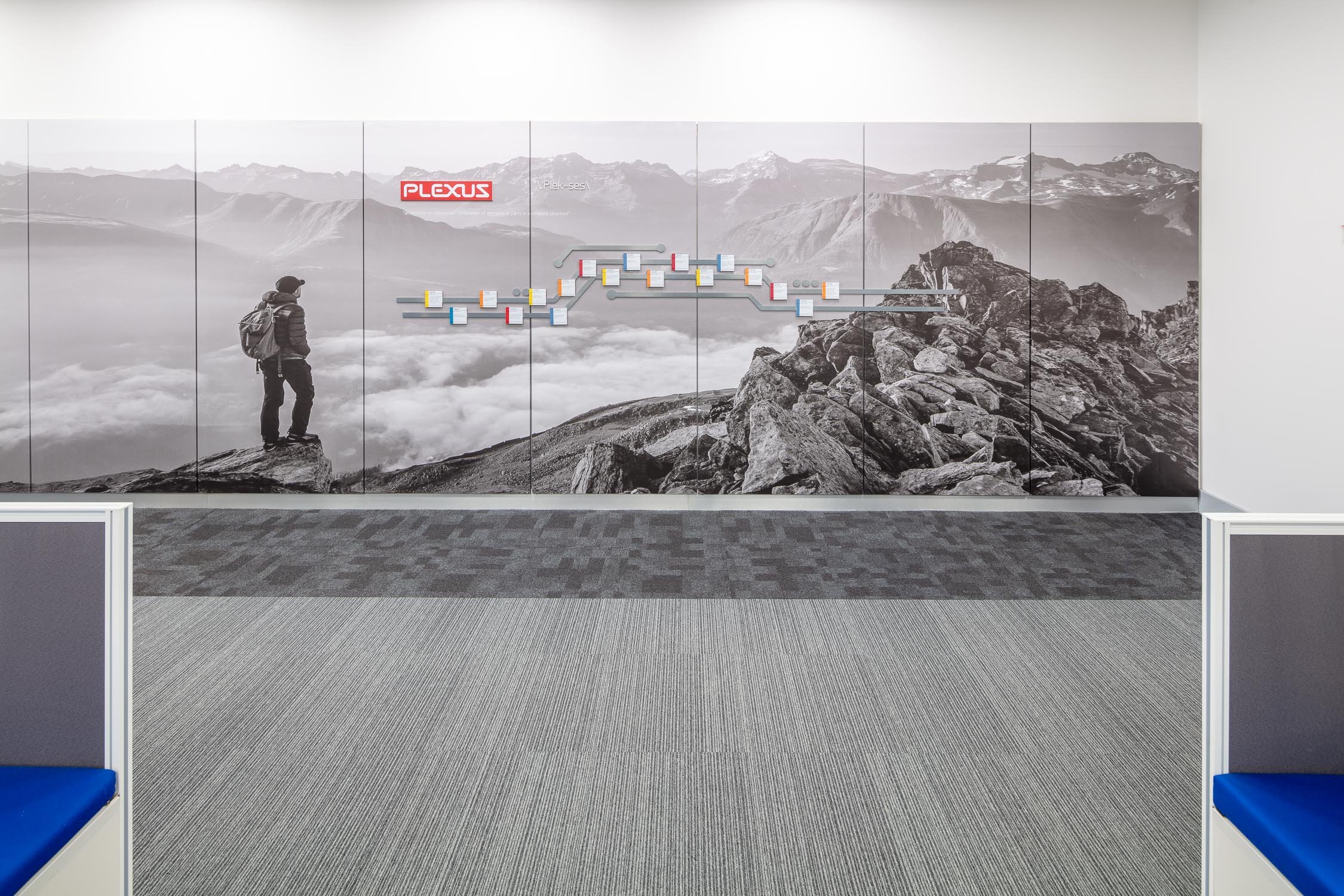
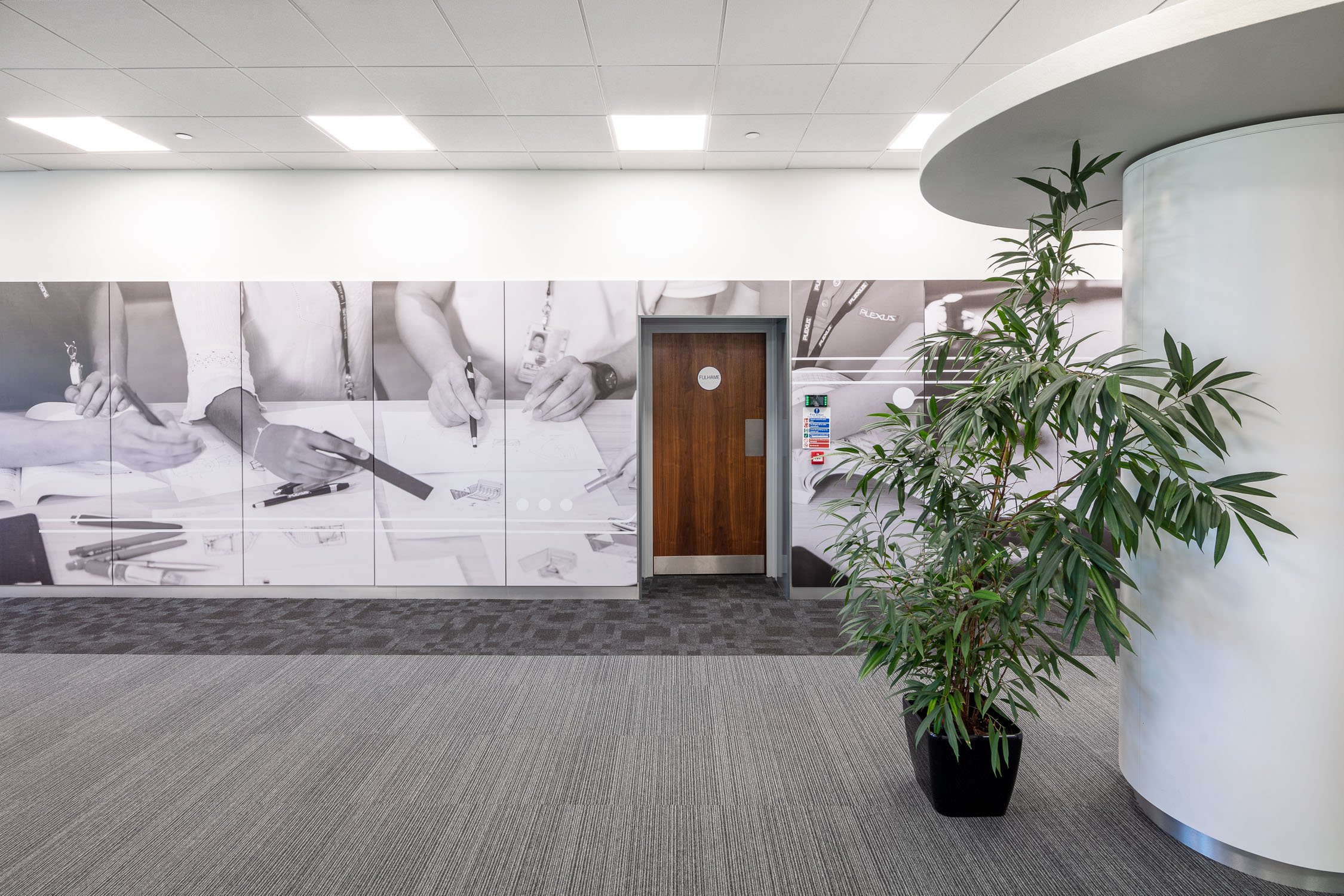
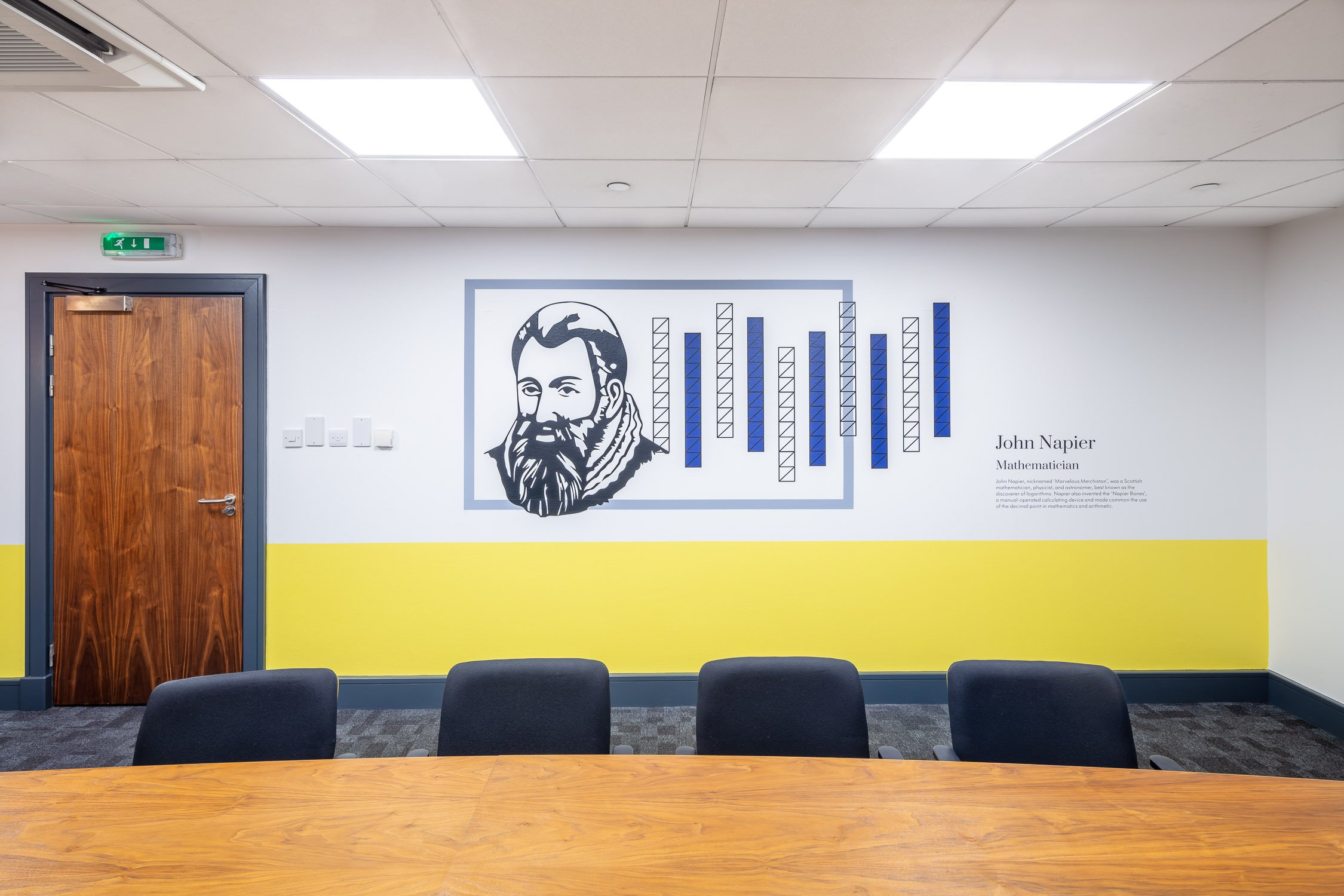
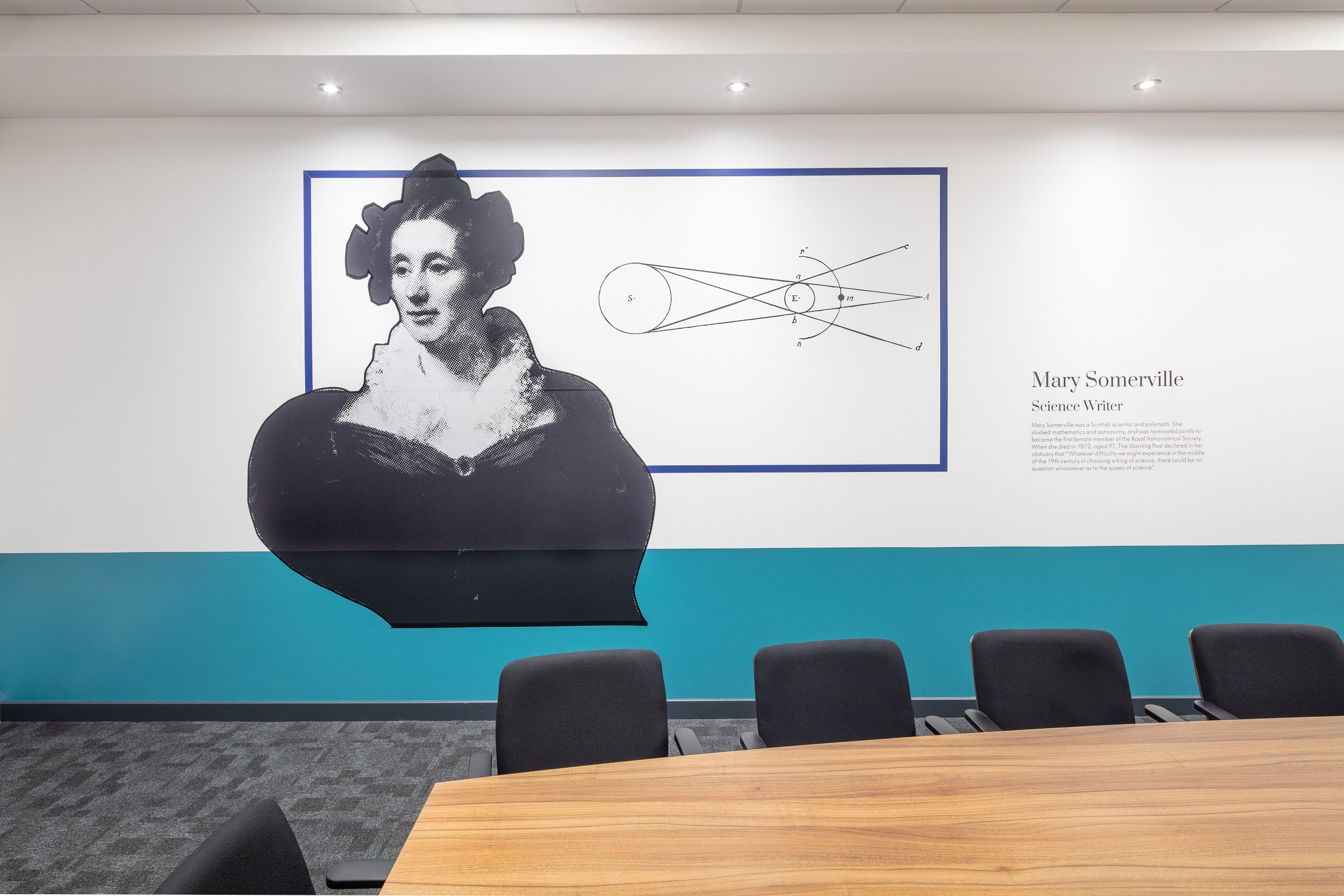
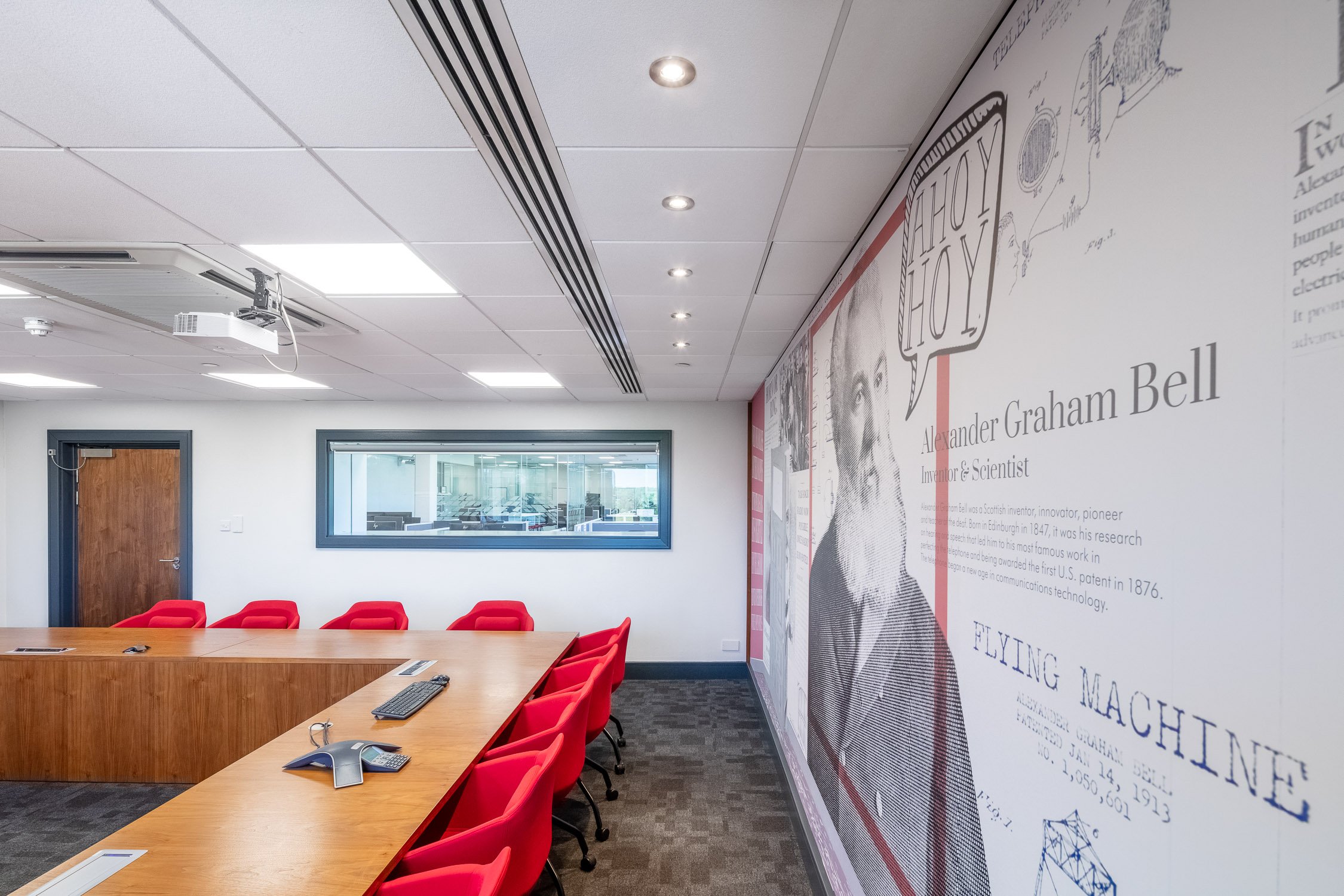
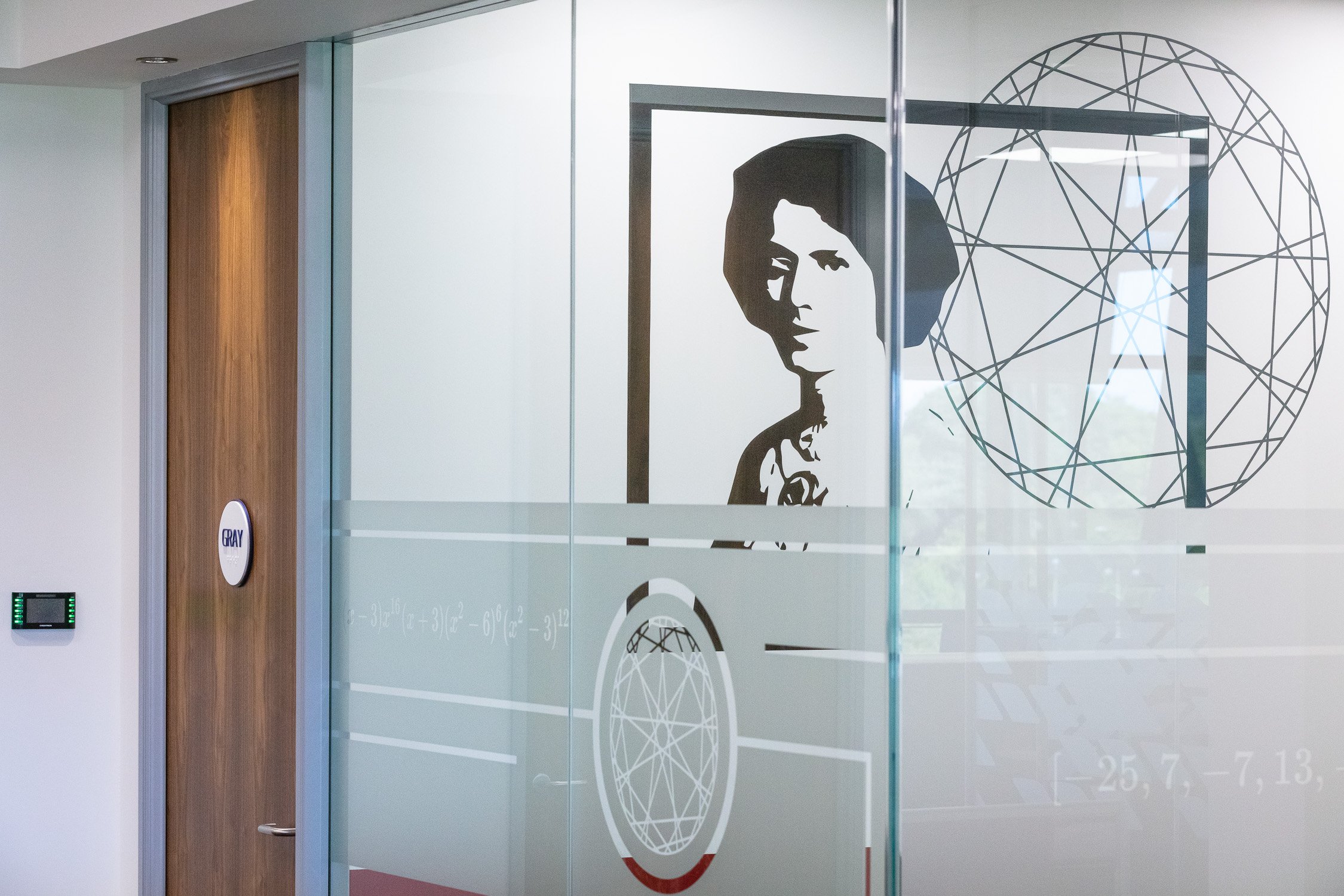
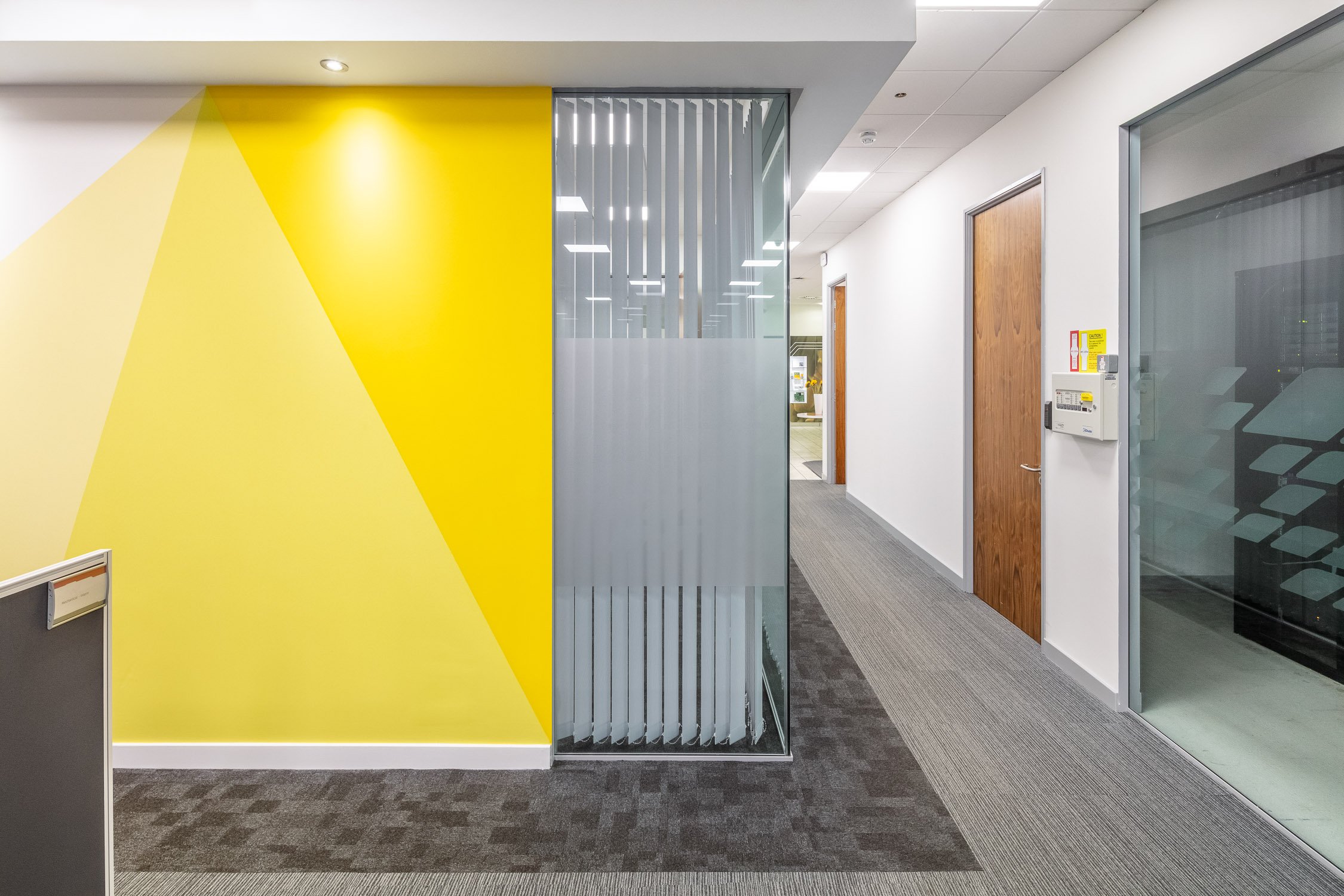
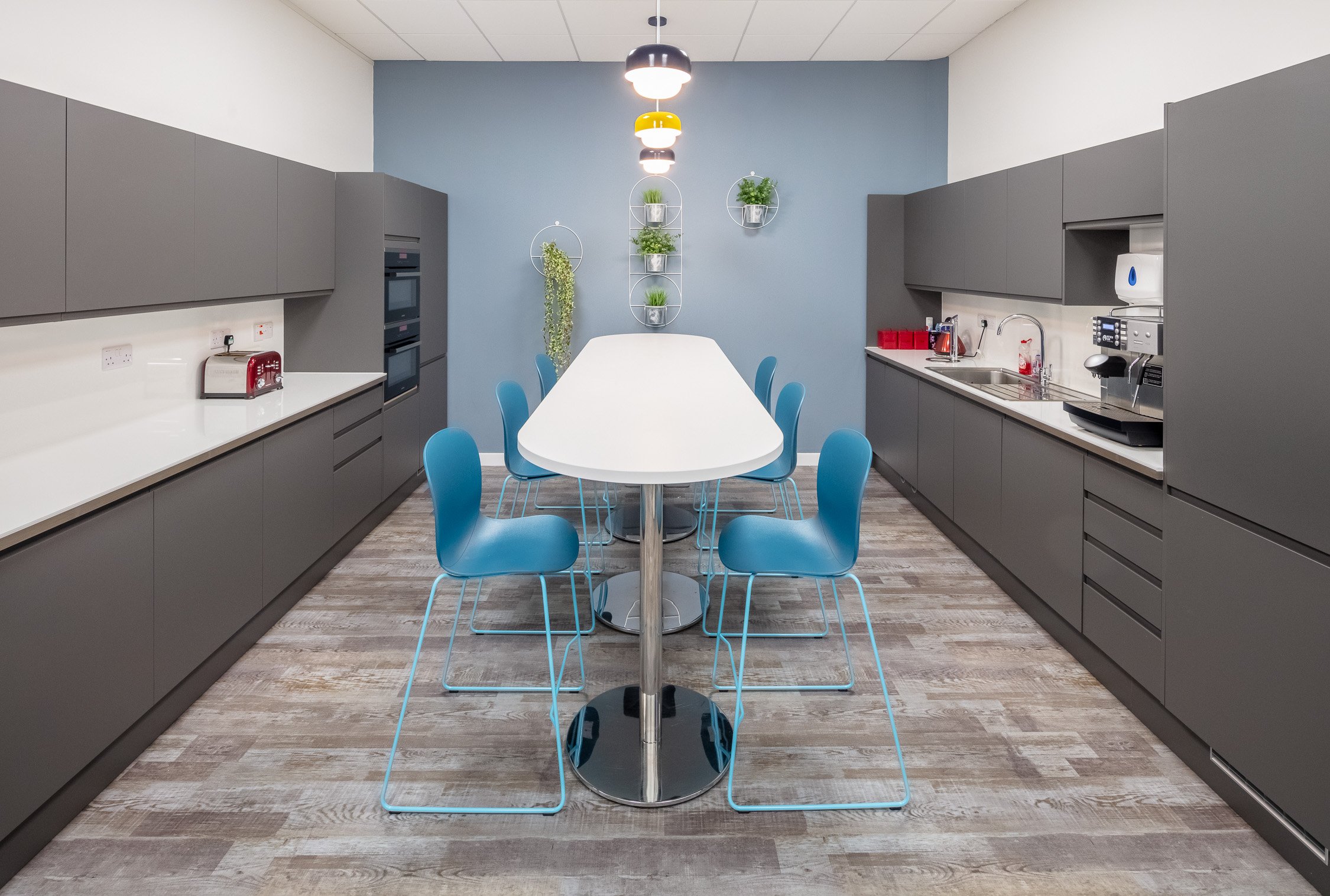
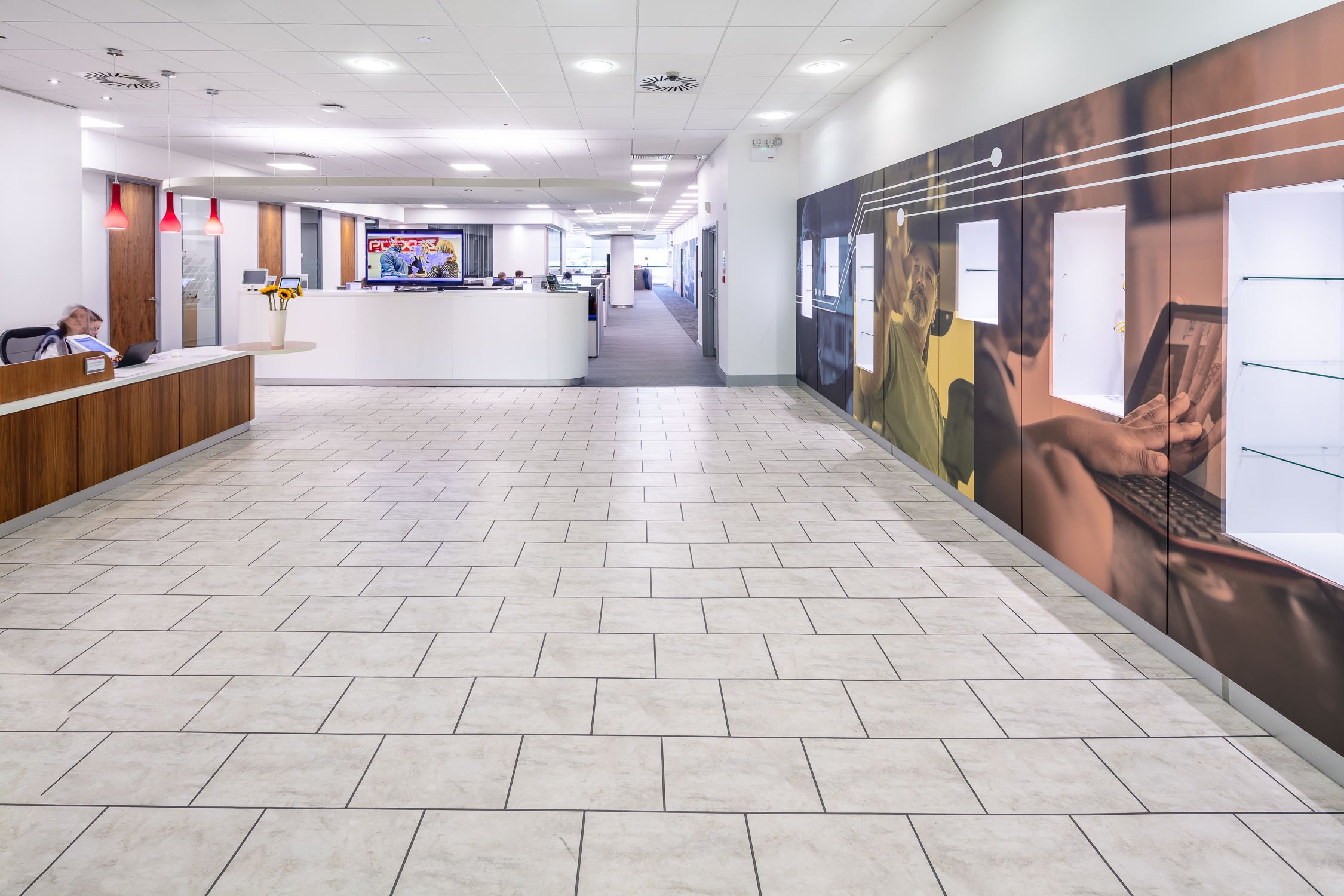
Publication date: 23 April 2019
Design, build, text and photography: The Amos Beech Team
Office fit out and refurbishment Dundee
When Scotland's only tyre manufacturer asked us to draft a plan for their office refurbishment and fit out in Dundee, the team here at Amos Beech set out to transform the 40 year old building.
Office fit out and refurbishment for Michelin Dundee
The Dundee plant has been transformed into a “state-of-the-art factory under the five-year investment programme. The Dundee factory opened its doors 43 years ago it is now the city's biggest industrial employer, with just 1000 staff. It manufactures more than seven million car tyres every year. The 'Bâtiment 10' or 'Building 10' hosts 70 office staff and every factory around the world has a 'Building 10' with office accommodation for similar office tasks.
Office fit out Dundee
The brief for this Dundee office refurbishment project
The need for this office refurbishment and fit out project in Dundee was clear from the outset. The building was old, uninspiring and even a depressing place to work. For a company of this stature, refurbishment was long overdue.
Michelin Dundee is Michelin’s best-in-class and is now topping the tables in efficiency and quality. Dundee was the first first Michelin factory in the world to embrace wind energy with two wind turbine generators helping to reduce environmental impact and energy bills.
It's standing attracts high profile visitors from across the world and needs an interior that you expect from a company like Michelin.
Also graduates were keen to start their career at Michelin, but the company struggled to keep staff on board. Michelin offers excellent training programs and career perspectives, but many talent left after a short period of time and when asked they mentioned the working environment was less then inspiring to say the least. You don't want that as an innovative and global company. After all “A better way forward” is the Michelin way:
The interior design and Lay-Out
The long rectangular building with cellular offices along corridors was to be transformed into a more open plan space with organic shapes. The desks were positioned off set from the walls and in the final design the wave desks were shaped nicely around the circular meeting pods.
Furniture specification
At Michelin 20 million euros are invested each year to develop new solutions for workstation ergonomics. Amos Beech have always been at the forefront of innovative seating and desking solutions and for this project sit-stand desking from Samuel Bruce, originally from Dundee was specified.
The days that working days were an important source for people's exercise are long gone for most people, especially for those that work in offices. Sedentary working applies to in between 4 and 6 hours per day in an average office and in total you are talking about 9 and 11 hours a day! A sit stand desk will bring in more variety in working posture during the day and reduces health risks. It also gives the flexibility in adjustment an international workforce like Michelin needs.
Changing between sitting and standing increases concentration and output which is essential for a best-in-class tyre manufacturing plant.
Office fit out project management
The office refurbishment was completed over two phases. We started on the ground floor and the initial works included the removal of part of the 1st floor to open up a more impressive staircase entrance reception area. A new staircase was manufactured to the designers specifications and all internal doors were replaced.
As the project was underway it was decided to build an entrance vestibule in front of the reception and despite the already tight time frame, this had to be completed within the timescales allowed.
Walls were opened up and replaced with glazed partitions to allow light to flood through the interior. These new glass partitions have been subtly branded with the iconic Bibendum and other Michelin marketing images.
The overall interior design scheme takes full cognisance of the Michelin brand and uses the approved branding colour palette to establish the Michelin identity whilst retaining a sense of belonging for the individuals who work in the space.
When the second phase started, we had to remove from the building a large safe that had been built in originally. Heavy lifting equipment and careful health and safety planning allowed this to happen without delays or damage to property or person.
As part of the overall scheme, all external single glazed windows were replaced by new double glazed units to improve the thermal efficiencies of the building and the heating and ventilations system was similarly upgraded to meet with the current standards.
The end result is a refreshing and modern interior which is already making a huge difference to the first impressions given to visitors on arrival. Going forward the Michelin management team are confident that the investment will reap rewards in terms of productivity and staff satisfaction.
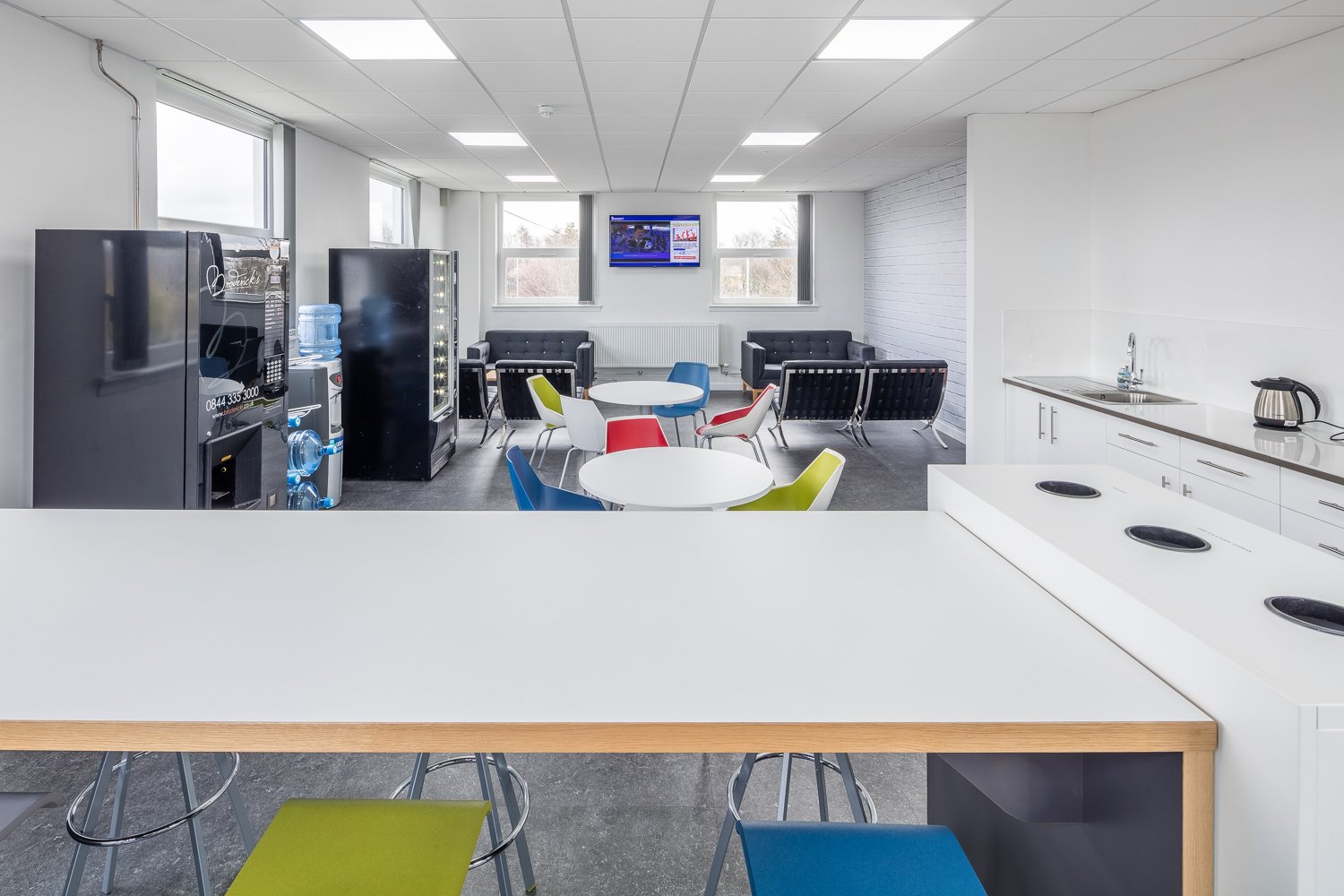
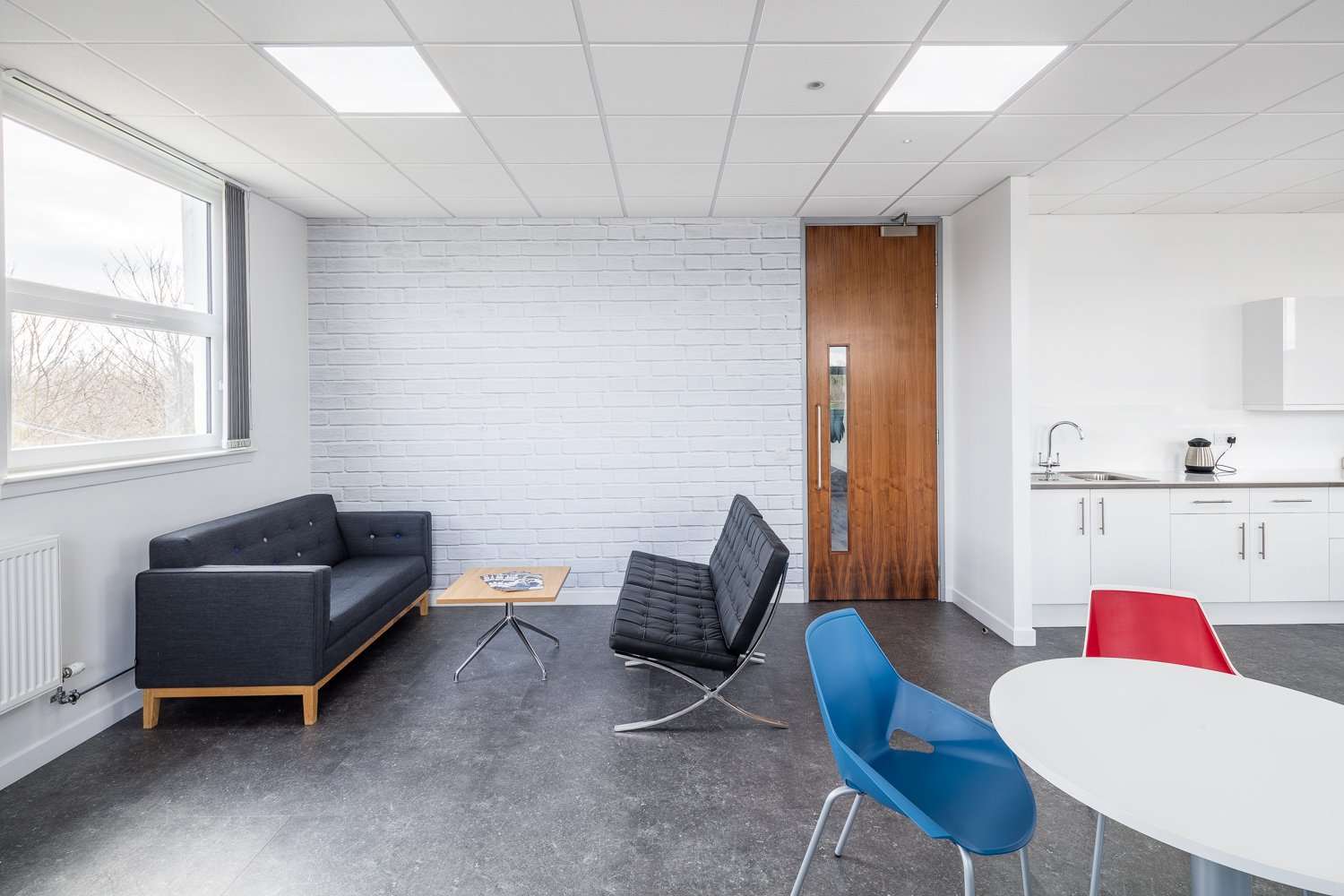
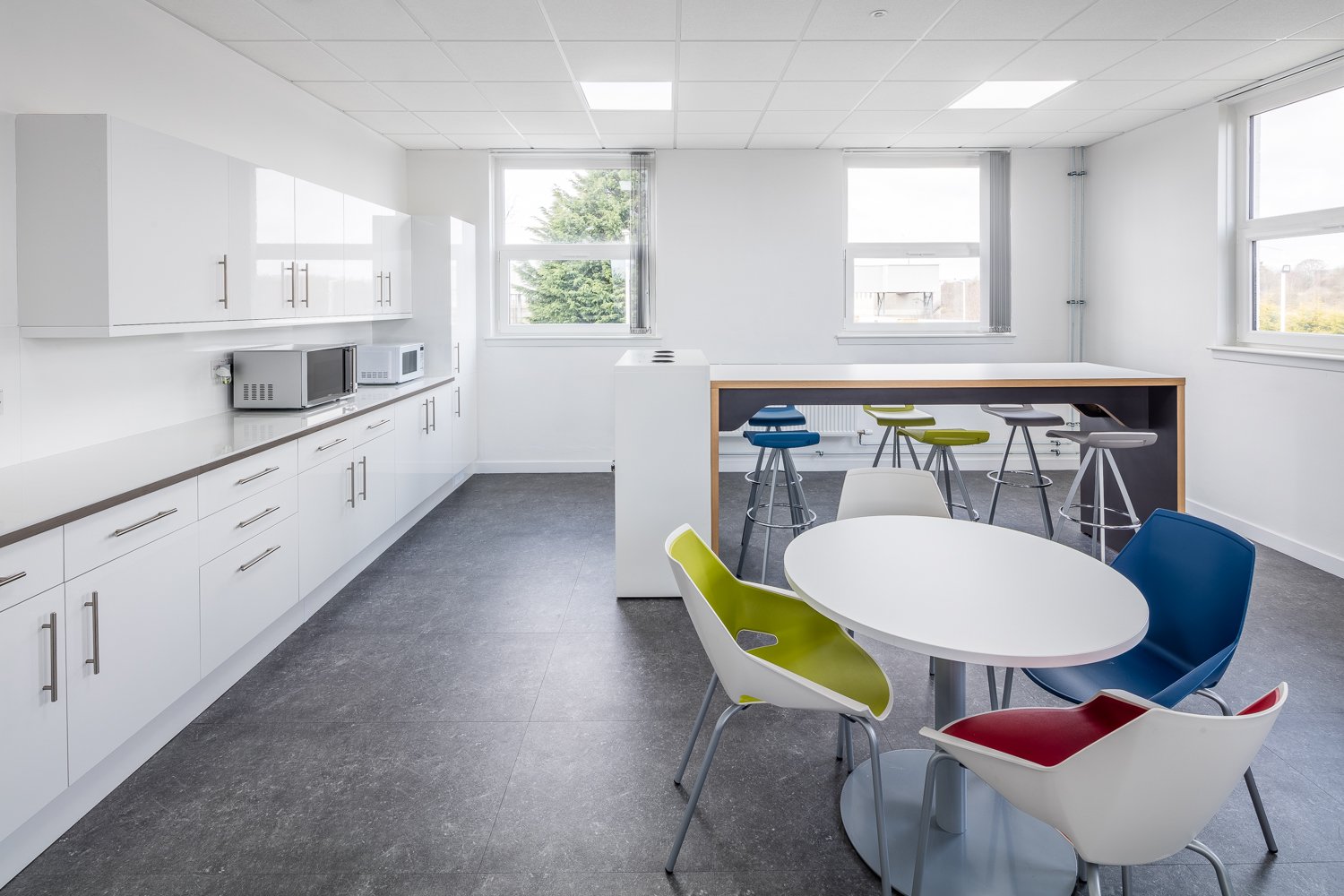
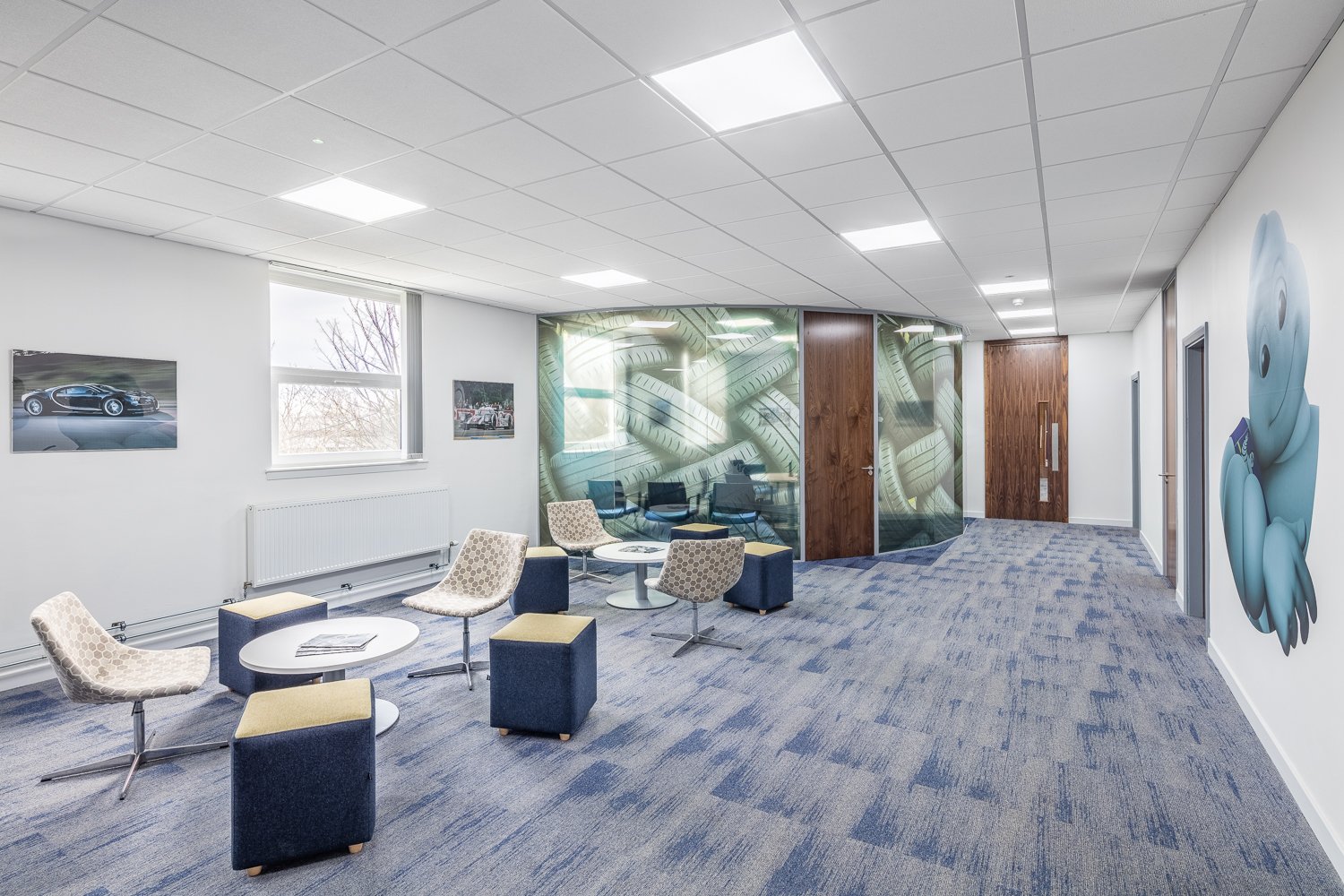
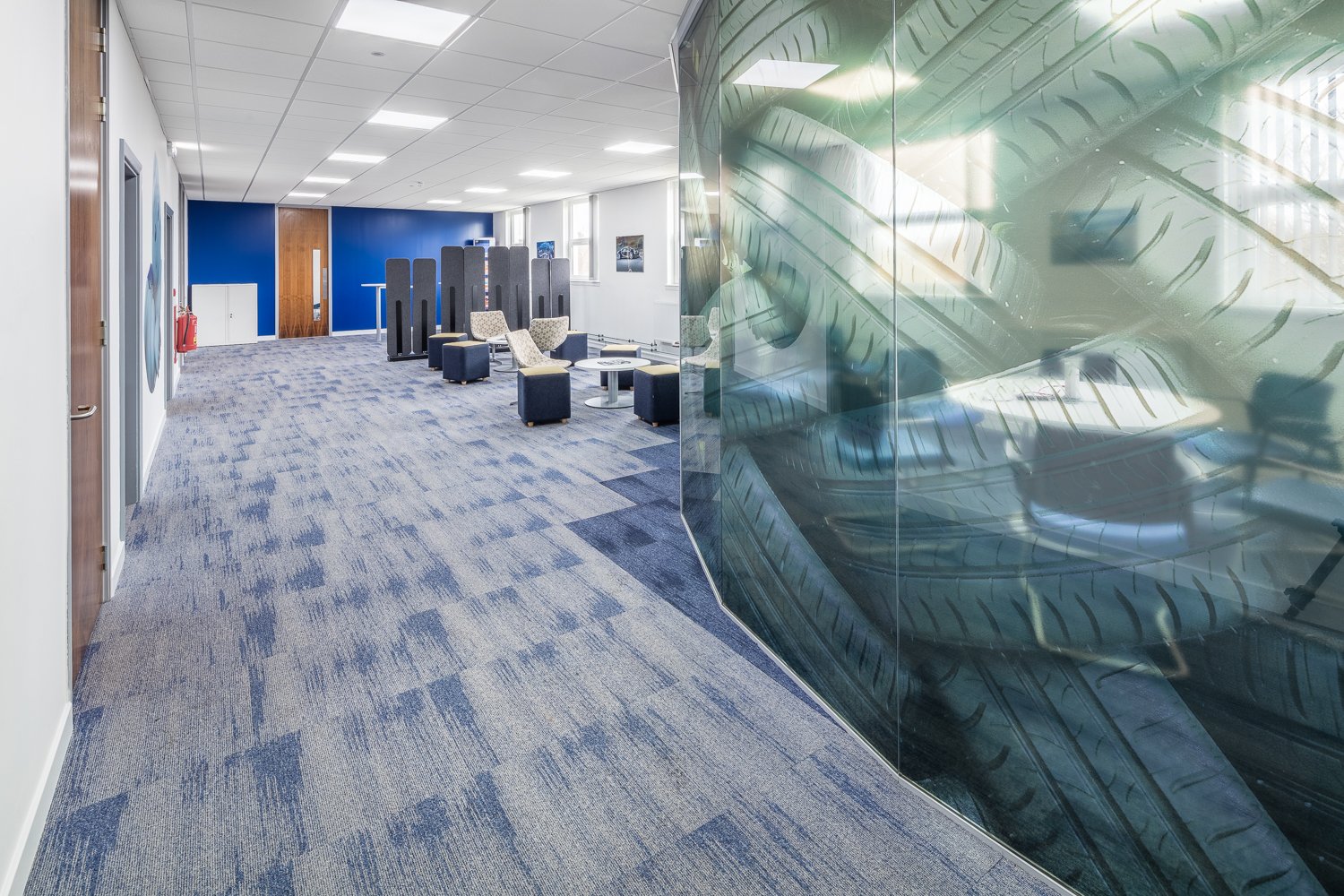
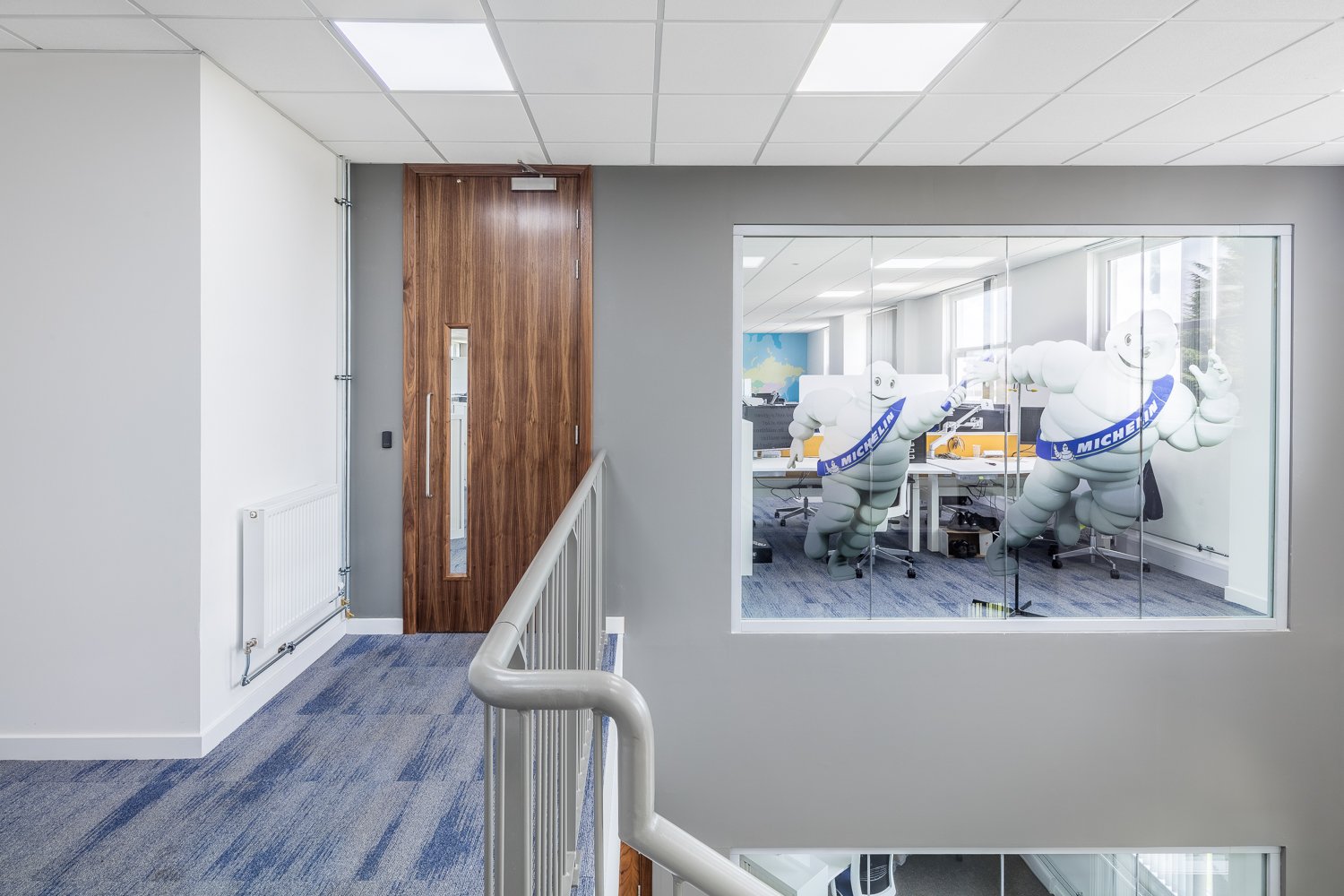
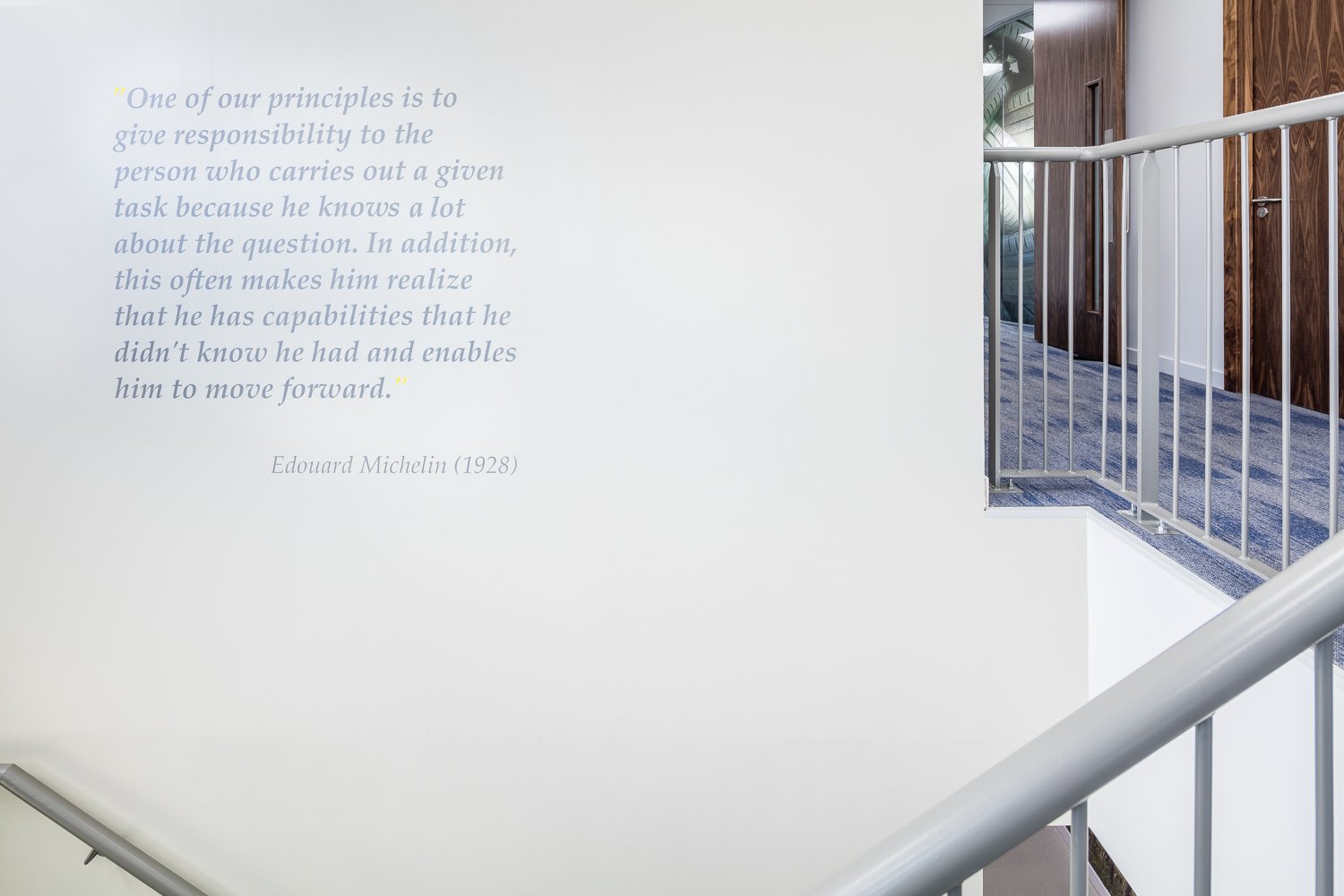
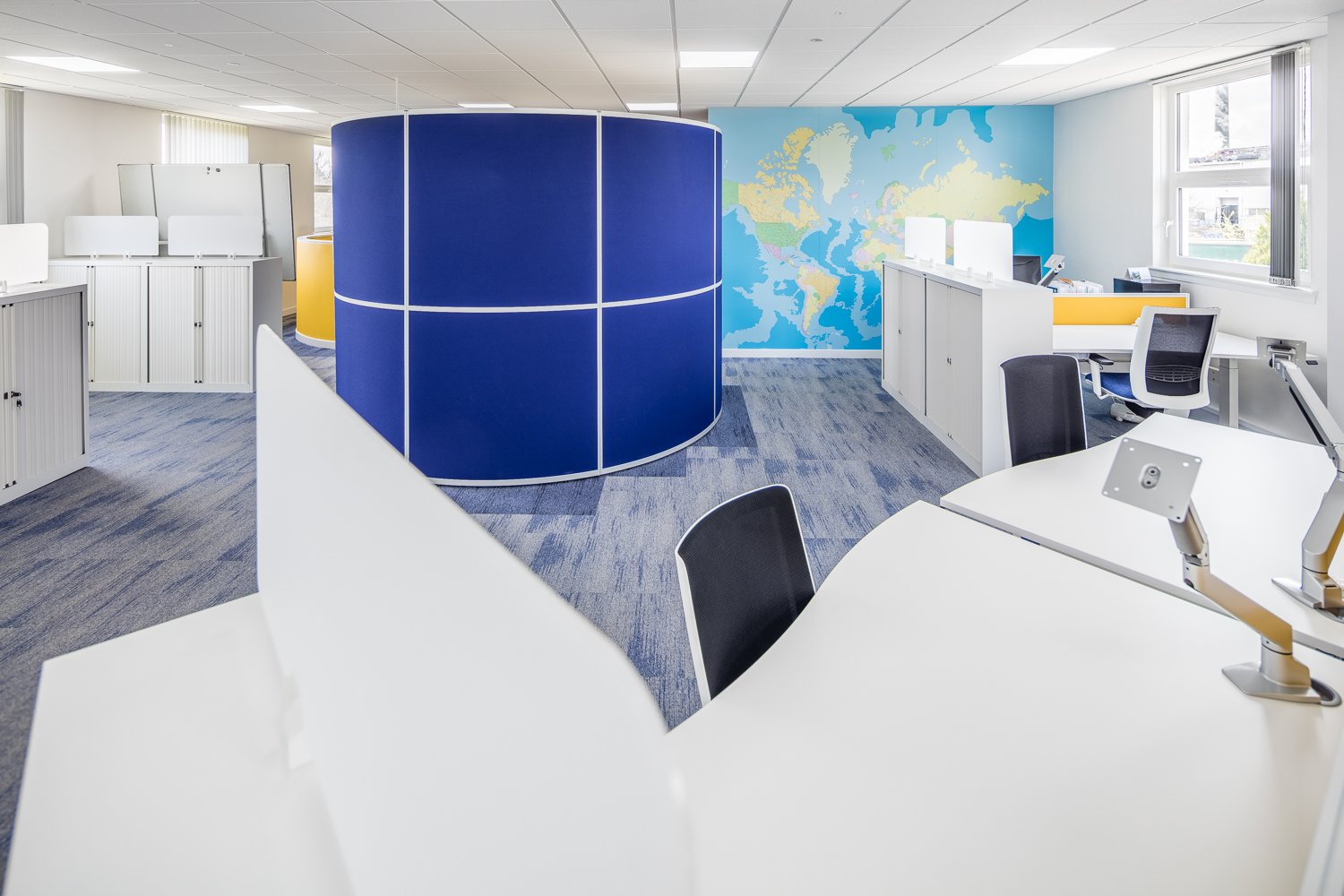
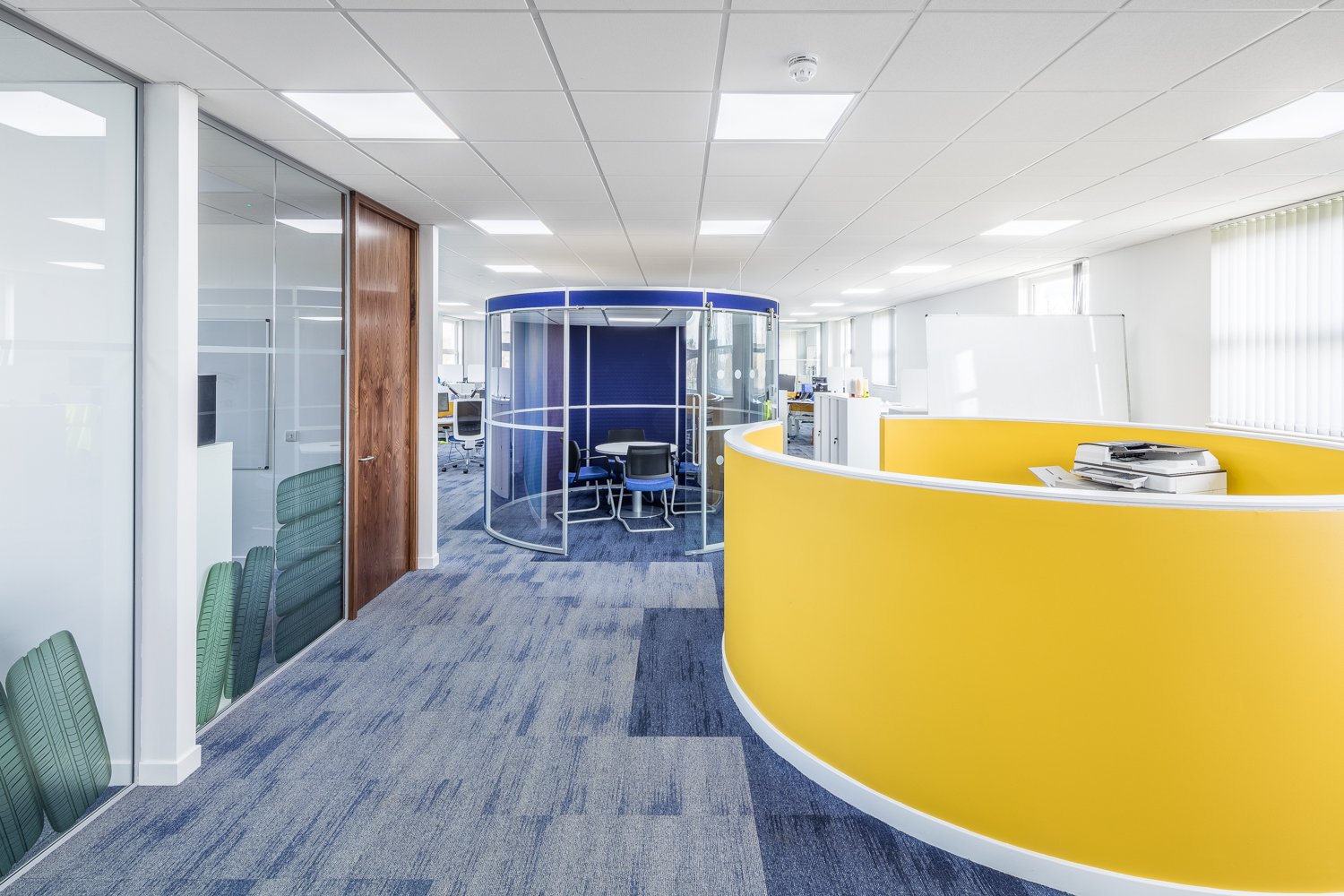
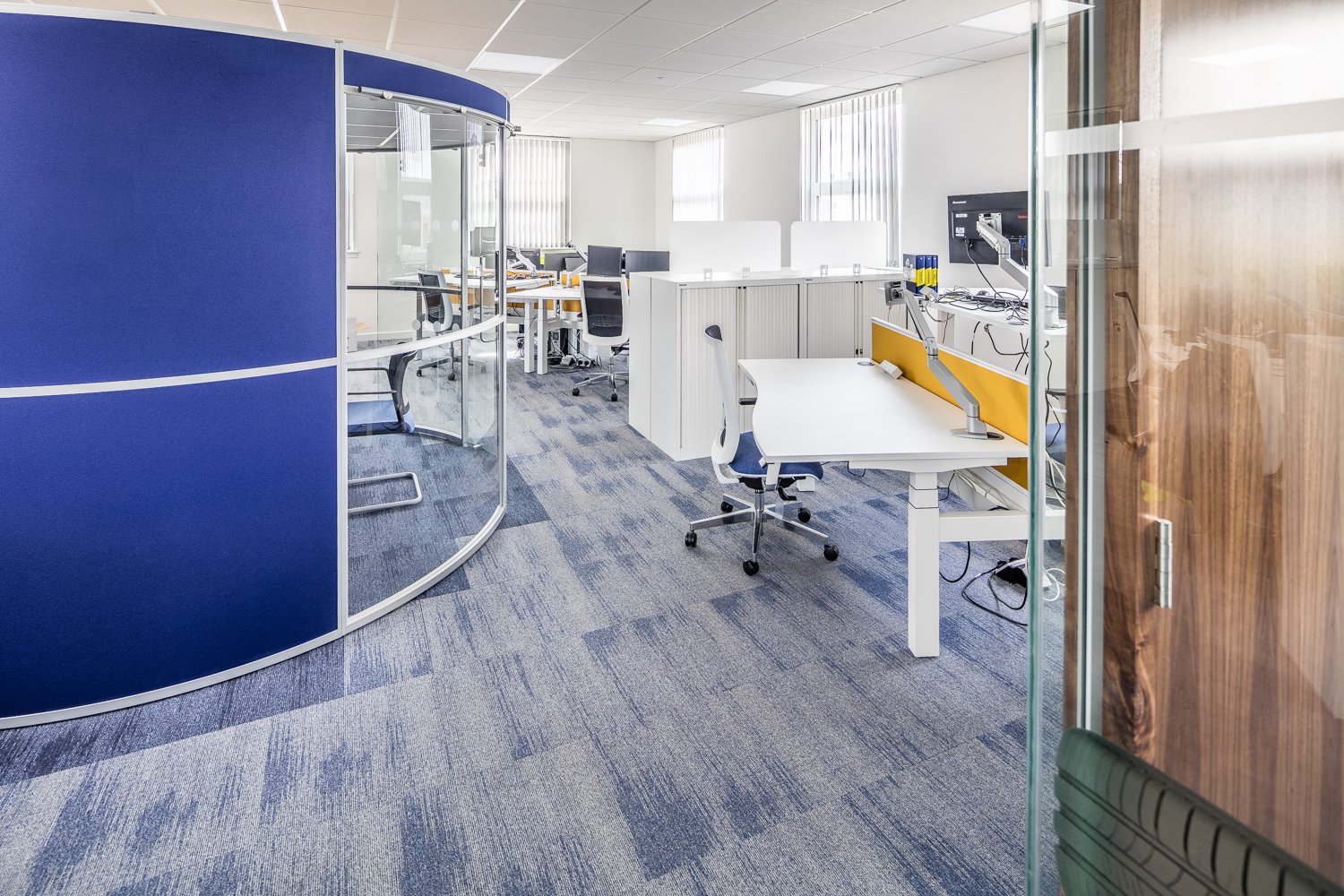
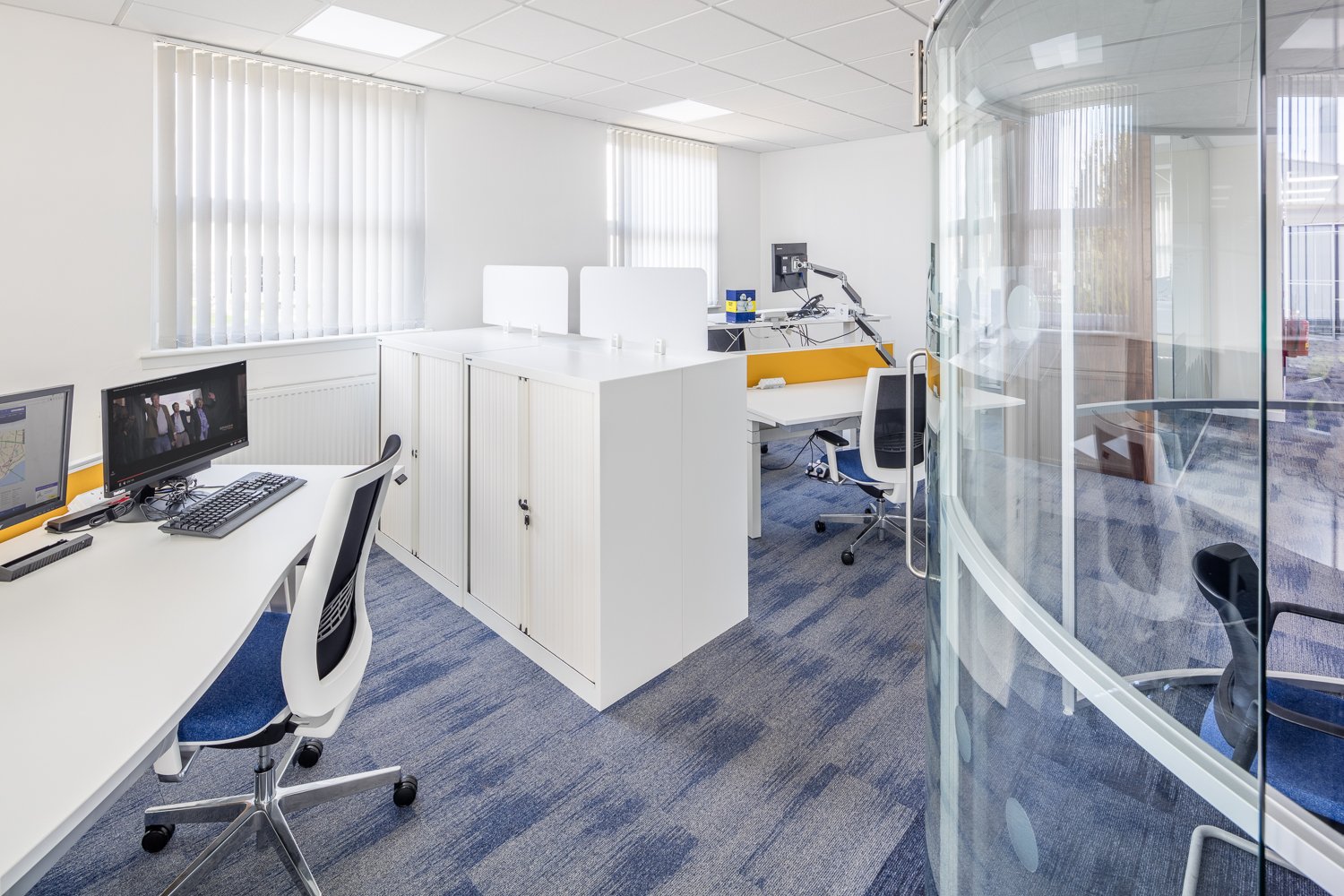
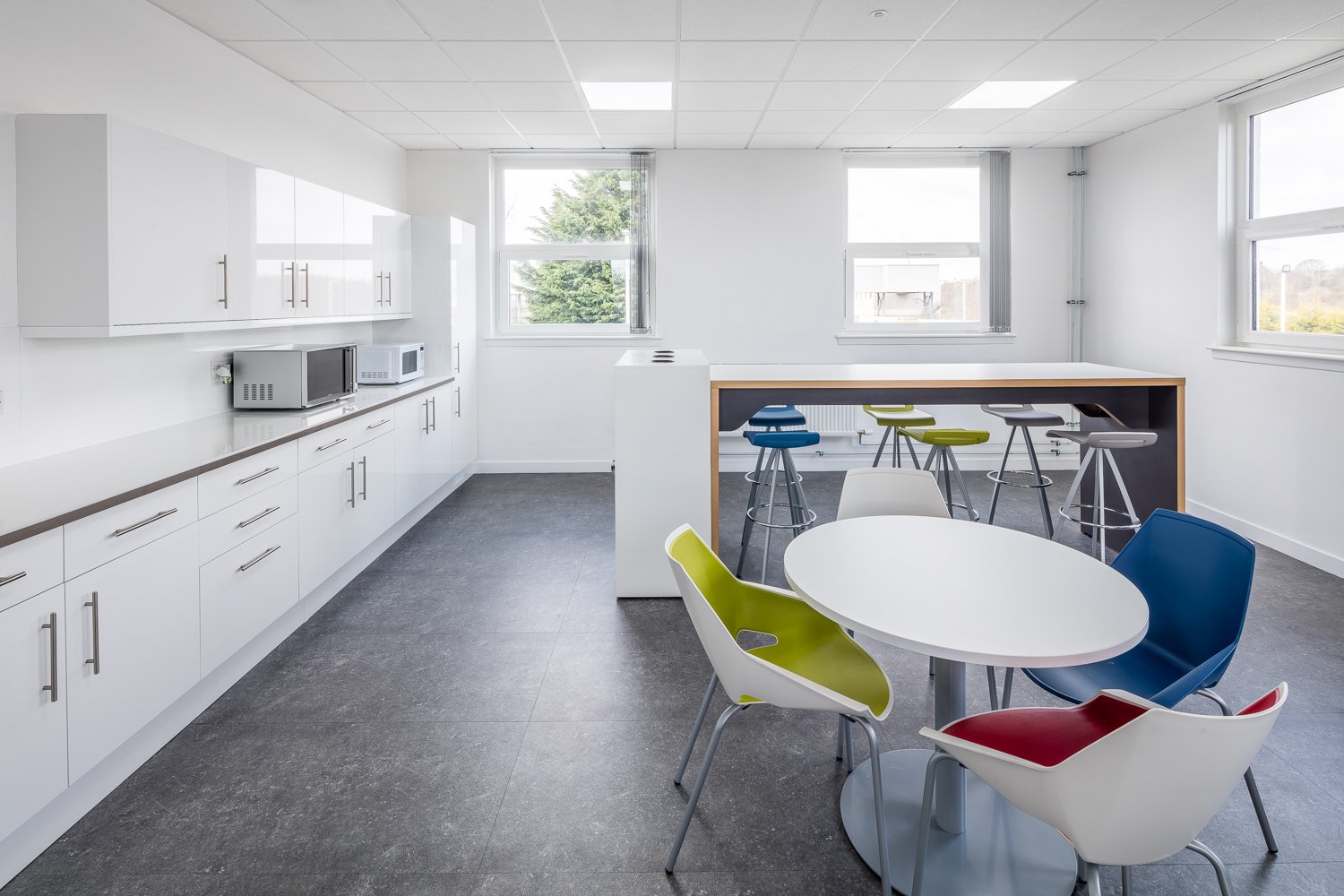
Publication date: April 11th, 2017
The office in the Blyth Building is currently in use as part of the Michelin Scotland Innovation Parc, after Michelin closed it’s operations in Dundee.
Text: Sam James
Photography: Architectural Photographer Edinburgh